What is a Proper Practice for a Lockout/Tagout Situation?
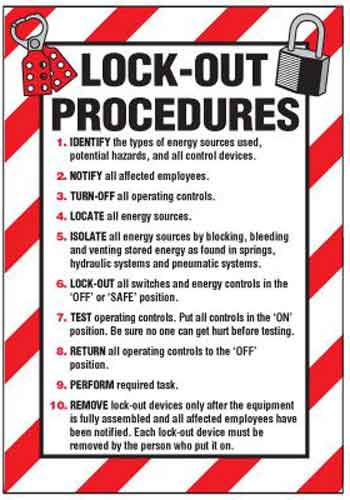
What is a proper practice for a lockout/tagout situation? This is one of the most important questions in workplace safety, especially in industrial environments where energized equipment poses serious risks. A proper lockout/tagout (LOTO) practice involves isolating energy sources, securing them with locks and tags, and verifying zero energy before any servicing or maintenance begins. The goal is to protect workers from unexpected startup or release of hazardous energy, which can lead to severe injury or fatality. In compliance with OSHA standard 29 CFR 1910.147, LOTO procedures must be clear, consistent, and enforceable to ensure worker safety.
Request a Free Training Quotation
Proper employee training is essential to ensure that all personnel understand the risks associated with hazardous energy sources and know how to follow the correct lockout tagout steps. The process of locking and tagging equipment must be carried out only by authorized workers who have been trained in compliance with standards set by the Occupational Safety and Health Administration (OSHA). Training helps prevent accidental energization and creates a safer environment during equipment maintenance and servicing by reinforcing procedural knowledge and hands-on practice. Read more here about OSHA LOTO.
Why Proper Lockout Tagout Practice Matters
A proper practice protects employees and ensures legal compliance with OSHA 29 CFR 1910.147 in the United States and CSA Z460 in Canada. Accidents resulting from releasing stored energy during servicing activities can cause severe injuries, fatalities, equipment damage, and legal penalties. By following established LOTO procedures, companies can demonstrate due diligence, reduce liability, and foster a culture of safety.
It is not just a regulatory requirement but a life-saving process that safeguards workers from hazardous energy during routine and emergency maintenance. Each step is vital in ensuring equipment remains safely de-energized from shutdown to verification. Implementing and maintaining these best practices can significantly reduce the risk of arc flash incidents, mechanical failures, and other workplace hazards.
Comprehensive Guide to Lockout Tagout Practices
Lockout Tagout refers to specific procedures designed to safeguard workers from the unexpected energization or startup of machinery and equipment, or the release of hazardous energy during service or maintenance activities. These procedures involve isolating energy sources and securing them with lockout devices and tags to prevent accidental operation.
Key Steps in Lockout Tagout Procedures
-
Preparation for Shutdown:
Before initiating LOTO, authorized personnel must identify all energy sources associated with the equipment and understand the types and magnitudes of energy involved. This preparation ensures that appropriate measures are taken to control hazardous energy effectively. -
Notification of Affected Employees:
Inform all affected employees about the impending lockout/tagout operation. Clear communication helps prevent misunderstandings and ensures everyone knows about maintenance activities. -
Equipment Shutdown:
Follow the manufacturer's recommended procedures to shut down the machinery or equipment safely. This step is crucial to ensure that the equipment is in a zero-energy state before maintenance begins. -
Isolation of Energy Sources:
Locate and isolate all energy sources using appropriate energy-isolating devices such as circuit breakers, valves, or disconnect switches. This step ensures that the equipment is completely de-energized and incapable of accidental startup. -
Application of Lockout/Tagout Devices:
Attach lockout devices to each energy-isolating device to prevent re-energization. Additionally, tagout devices should be placed to indicate that the equipment is under maintenance and should not be operated. Only authorized employees should apply and remove these devices. -
Release of Stored Energy:
Even after energy sources are isolated, equipment may still contain stored energy in the form of electrical charge, hydraulic pressure, compressed air, or thermal energy. A critical Lockout Tagout practice is safely releasing or restraining this energy to ensure the machine cannot move or activate during servicing. Examples include bleeding off hydraulic lines, discharging capacitors, or securing moving parts. -
Verification of Isolation:
Before any servicing or maintenance begins, the authorized employee must verify that all energy sources have been effectively isolated. This may include attempting to start the machine using its normal operating controls (a test start) to confirm it will not activate. Once verified, controls must be returned to the "off" position. -
Performing Servicing Activities:
Maintenance or servicing work begins after the above steps have been completed and verified. Throughout the process, no unauthorized employee should attempt to remove devices or restore power. -
Removing Lockout/Tagout Devices and Restoring Equipment:
Once maintenance is complete and the equipment is ready to return to service, a specific process must be followed. All tools and non-essential parts must be removed. Guards or safety devices must be reinstalled. Only the same authorized employee who applied the devices may remove them. After removal, notify affected employees and restore power safely and under control.
Best Practices for Effective Lockout Tagout Implementation
To maximize the effectiveness of Lockout Tagout practices in the workplace, employers should:
- Develop written LOTO procedures for each type of machine or equipment.
- Ensure that all energy sources—including electrical, mechanical, hydraulic, pneumatic, chemical, and thermal—are clearly identified and controlled.
- Provide thorough LOTO training for both authorized and affected employees.
- Conduct periodic audits and retraining to maintain compliance.
- Use standardized lockout devices, tags, and identification labeling across the facility.
Training and Authorization
Only trained and authorized employees should perform LOTO procedures. Workers must understand their role — whether they are authorized, affected, or other personnel — and follow written policies. Regular refresher training ensures consistent application and helps prevent complacency.
Documentation and Written Procedures
OSHA requires documented procedures for complex systems. These instructions should outline the exact sequence of LOTO steps, including shutdown, isolation, device application, and verification. Documentation helps maintain consistency and provides legal compliance.
Reenergization After Maintenance
After maintenance is complete:
- Inspect equipment for readiness
- Remove tools and replace guards
- Notify employees that energy is being restored
- Only the person who applied the lock should remove it
Following a structured restart process is just as important as the initial isolation.
Consequences of Improper Lockout/Tagout Practices
Failure to follow proper LOTO practices is one of the leading causes of industrial accidents. Consequences include electrical shock, crushing injuries, amputation, or death. Beyond personal harm, companies risk regulatory fines, equipment damage, and lost productivity.
Frequently Asked Questions
Who is responsible for ensuring proper LOTO practices?
Employers are responsible for establishing and enforcing lockout/tagout programs. However, employees are also responsible for following procedures and reporting unsafe practices.
Does every energy source need to be locked out?
Yes. Every source of hazardous energy must be isolated, including secondary sources like stored pressure or spring tension.
Are tags alone sufficient?
No. Tags are only warning devices. OSHA requires both lock and tag for full compliance.
How often should LOTO training be conducted?
Initial training is mandatory, with retraining required every 12 months or whenever there is a change in equipment, process, or personnel.
Proper practice for a lockout/tagout situation involves more than locking a switch—it’s a comprehensive safety strategy built on clear procedures, training, documentation, and verification. When followed correctly, LOTO procedures protect workers, prevent injury, and ensure compliance with OSHA regulations. In high-risk environments, lives depend on them.
Read More About Lockout Tagout
Return to the Lockout Tagout Overview Page
On-Site Training
Interested in cost effective, professional on-site electrical training?
We can present an Electrical Training Course to your electrical engineering and maintenance staff, on your premises, tailored to your specific equipment and requirements. Click on the link below to request a Free quotation.
EF PARTNER MEDIA
Product Showcases
Shared Media