TBM Consulting Group launches “Lean Energy Practice”
Through its “Lean Energy Process,” which enables companies to rapidly achieve energy productivity, TBM will help clients conserve resources such as water, gas, compressed air, oil and electricity. The process has already helped manufacturing clients worldwide achieve improvement on energy costs. McCain Foods Limited, a global frozen foods company with over $6 billion in sales, had an energy savings of $300,000 at a single facility.
In addition to tracking energy flow, the Lean Energy Practice will also provide maintenance and sustainability initiatives for long-term savings. Its Total Productive Maintenance Services, a critical adjunct to “lean” manufacturing, is focused on waste elimination, preventing deterioration and reducing equipment breakdowns – a proactive approach that prevents any kind of process interruption before maintenance is needed.
Doug Kiss, a lean consultant at TBM with over 30 years manufacturing experience, will lead the practice. He has been certified in Total Productive Maintenance by the Japan Institute of Plant Maintenance. Formerly a corporate quality consultant for United Technologies, he led the operationÂ’s transformation initiative involving more than 50 facilities and the supply base. Trained in Japan in 3P and in kaizen, Doug has led lean programs for facilities worldwide. The practice will monitor the flow of energy through a breakthrough process called an energy kaizen (a Japanese word with two roots: kai meaning change and zen meaning good). By identifying and then eliminating waste, the kaizen creates immediate change, improving the flow to the companyÂ’s bottom line.
A one-week energy kaizen event focused on a single source of energy can typically generate a cost reduction of four to eight percent annually for a company, resulting in a savings of $200,000 - $500,000 or more a year.
Wasted energy, says Kiss, often results from improper machine conditions, lack of standard work, excessive inventories and unnecessary processing.
“The manufacturing community has an urgent need to exert control over rising energy costs,” said Anand Sharma, CEO, TBM Consulting Group. “To improve financial performance particularly during turbulent times, it’s crucial for manufacturers to conserve their energy resources.”
According to the National Association of Manufacturers (NAM), more than 40 percent of all U.S. energy is used by industry, including transport of manufactured goods. It also reports that U.S. manufacturers can save the equivalent of $10.4 billion if it reduces energy consumption by just 10 percent.
Related News
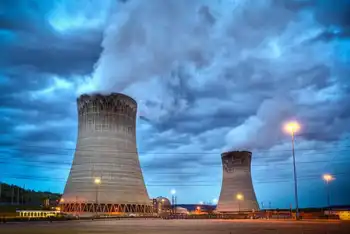
Nuclear plants produce over half of Illinois electricity, almost faced retirement
CHICAGO - Nuclear plants have produced over half of Illinois electricity generation since 2010, but the states two largest plants would have been retired if the state had not created a zero emission credit (ZEC) mechanism to support the facilities.
The two plants, Quad Cities and Clinton, collectively delivered more than 12 percent of the states electricity generation over the past several years. In May 2016, however, Exelon, the owner of the plants, announced that they had together lost over $800 million dollars over the previous six years and revealed plans to retire them in 2017 and 2018.
In December 2016, Illinois passed the Future Energy Jobs Bill, which established a…