Cow patties producing clean, green power
Then, as you draw near, another sensation takes hold - the oppressively pungent odour of cow manure.
On this day, the enveloping fog is making the smell worse than usual, explains Bern Kotelko, the mastermind behind this olfactory assault. But this is, after all, a feedlot, and the odour, he maintains, is actually the sweet smell of Canada's energy future.
The domes are Mr. Kotelko's monument to manure, the first stage in an ambitious power plant and bio-refinery based on animal waste that is taking shape beside his beef feedlot a 90-minute drive east of Edmonton. The goal, he says, is to "move manure off the balance sheet as a liability and turn it into an asset."
Mr. Kotelko is among the leaders in a manure-to-megawatt movement which, at its most visionary, lays on pie-in-the-sky rhetoric as thickly as the stuff collecting in cattle pens. Yet he is no wide-eyed dreamer operating on the fringes of capitalism, but a hard-headed cattleman.
The planned $100-million venture, which he hopes to complete in two years, will convert cattle excrement - whose disposable is a chronic challenge in large farming operations - into green power. The facility will also fuel an ethanol plant, turn out valuable cattle feed, and produce a more efficient cocktail of nutrients to spread on the land.
With dung as feedstock, "we don't have to worry about the hurricane that's going through Houston or someone having a hissy fit in the Middle East," Mr. Kotelko says.
This highly integrated operation, Mr. Kotelko predicts, offers up an alternative to an energy base tied to the vagaries of hydrocarbons.
Mr. Kotelko, part of a long line of Ukrainian farmers who came to Canada in the early 20th century, has two children working in the business, and he sees the plant as a role model to help arrest the long sorry trend of rural decline. "If you don't make the agriculture interesting, young people aren't interested in working at the bottom of the food chain," he says.
From a small homestead in 1918, the Kotelko family's Highland Feeders Ltd. has grown to 6,000 acres, 50 employees, a feedlot of 36,000 cattle - considered about the sixth largest in Canada - and $60-million in annual revenue from operations that include an antibiotic-free, non-hormone beef brand, Spring Creek Ranch, run by his daughter Kirstin.
Yet Mr. Kotelko, 55, insists his core product is information. He holds an agriculture science degree from University of Alberta. Brother Mike is a farm engineer, and MBA graduate Page Stuart runs their feedlot operations. For the biogas plant, they are working with a team of scientists at U of A, led by Xiaomei Li, a soil specialist born in China.
These days, their primary focus is on the Highland Feeders' cattle pens that extend over two kilometres. The cattle are kept in what are, by industry standards, clean, spacious corrals, where feed is continually replenished with computer-aided monitoring. "I think these cattle are comfortable for their time in this world," Bern Kotelko says.
About 20 per cent of the feedlot manure is being fed into the dome-like anaerobic digester that function like a high-tech version of a cow's stomach. A large biogas plant by North American standards, it transfers methane and carbon dioxide to a small power plant linked to the power grid - enough now to electrify a village of 1,200 people.
When the plant is completed, Mr. Kotelko expects it will take 80 per cent of his manure, enough to power a town the size of Vegreville, population 5,500, which lies 20 kilometres to the south.
Mr. Kotelko insists the process also solves the tricky economics of ethanol fuel, whose production typically eats up a lot of external energy. In his model, biogas from the feedlot will also power an ethanol refinery on the site, providing big energy savings.
The refinery, using cattle-feed wheat as an input, will also turn out distillers' grains that go back to the feedlot for cattle nourishment. Thus, the plant operates as a closed loop - from manure to energy to cattle feed back to manure. Mr. Kotelko says it will take the ethanol plant four years to be weaned off government support.
While ethanol's detractors often cringe at its profligate use of energy and precious wheat and corn, Mr. Kotelko argues ethanol is a key piece in the food production puzzle. It will help feed the world, he says, because it will stabilize demand for grain, thus protecting farmers from volatile markets.
There are other manure-based power operations in North America, but observers say this plant will stand out for its size and integration. "I don't think there will be anything like it in Canada,' says Bruce Bowman, a retired Agriculture Canada scientist, who runs ManureNet, an information website.
Another model is advanced by Toronto-based Stormfisher Ltd., which is planning a centralized digester in London, Ont., that will take biowaste from Loblaw supermarkets and from food processing firms, as well as manure from dairy farms.
The plant, scheduled for completion at the end of 2010, will cost about $20-million, and will feed into Ontario's power grid, capitalizing on an attractive tariff structure for alternative energy providers. Stormfisher, with about $350-million to invest, is backed by Boston-based Denham Capital, a private equity group.
Meanwhile, the Kotelkos have raised equity from local producers and an undisclosed energy company, as well taking on debt. They have already spent about $30-million, and expect green incentives to provide about 20 per cent of the total $100-million cost. For help with technology and business development, they teamed up with Evan and Shane Chrapko, Alberta brothers who made a killing in computers in the 1990s.
Mr. Kotelko points out that the Alberta oil sands were heavily financed by governments 30 years ago, but today, they stand on their own. And the oil sands, he argues, are simply a stop-gap on the way to more sustainable energy solutions, such as his biogas plant.
The strength of the Kotelko model lies in its holistic nature, says Joseph Doucet, professor of energy policy at University of Alberta. The operation uses cow manure to generate electricity and fertilizer, and even the excess water will be recycled back to the cattle. "So they are not only getting the electrical value but reducing the waste problem."
The Kotelko operation is marginal in the big picture of electricity and energy in Alberta, he says, "but it is possibly the door opening to a broader suite of technologies and solutions."
Other feedlots in Alberta are interested, and the Kotelkos and Chrapkos are working out a joint venture with a public power authority in Karachi, Pakistan.
"They have a city of 18 million and they have 400,000 dairy cattle in the city limits," Bern Kotelko says. Most of the waste is hauled to a river. "It is just a mess," he says excitedly - and nothing gets this farmer more excited than a mess of manure.
Related News
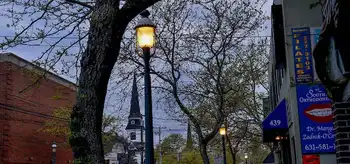
Announces Completion of $16 Million Project to Install Smart Energy-Saving Streetlights in Syracuse
SYRACUSE - Governor Andrew M. Cuomo today announced the completed installation of energy-efficient LED streetlights throughout the City of Syracuse as part of the Governor's Smart Street Lighting NY program. Syracuse, through a partnership with the New York Power Authority, replaced all of its streetlights with the most comprehensive set of innovative Smart City technologies in the state, saving the city $3.3 million annually and reducing greenhouse gas emissions by nearly 8,500 tons a year--the equivalent of taking more than 1,660 cars off the road. New York has now replaced more than 100,000 of its streetlights with LED fixtures, a…