Plant earns high-powered honor: Coal group lauds safety, efficiency
And as of February, the high-powered operation's 120 employees recorded 1 million work hours without suffering a single accident that would force someone to miss a shift, a streak that's still running today. "Right now this is the best plant in America," said Randy Rahm, chief operating officer for Ethanex Energy and a board member for the PRB Coal Users' Group.
Leaders of the group, a coalition connected with coal supplied from Wyoming's massive Powder River Basin, gathered in Lawrence to celebrate the naming of Westar's Lawrence Energy Center as the group's 2007 Plant of the Year. About 90 representatives from the group, other utilities and Westar Energy toured the plant and gathered for lunch.
The honor, the third for a Westar plant in the past six years, honors the Lawrence operation for its clean safety record, focused risk-management efforts and expansive equipment upgrades designed to improve the plant's environmental performance. The moves all came while burning PRB coal, the raw material that fuels 70 percent of the coal-fired energy production in the United States, itself a process that accounts for half of the electricity filling the nation's energy grid. The Lawrence plant topped about 150 other plants to secure the group's No. 1 honor. "It means a lot because it does come from our peers," said John Bridson, executive director for the Lawrence plant, which occupies 600 acres at 1250 N. 1800 Road.
The Lawrence plant, which saw its first generator come on line in 1938, had been burning coal from the eastern United States until 1998. That's when the operation switched to PRB coal, a less-expensive fuel that burns cleaner - it contains less sulfur - but heightens complications resulting from ash, coal dust and other byproducts.
That led Westar to embark on a list of equipment upgrades, including replacement of conveyors and a crusher to boost coal consumption. Electrical circuits were upgraded to provide "explosion-proof" service, and systems to detect and suppress fires also ere upgraded.
The upgrades and other projects - costing $22.4 million, according to Westar - have given employees more time to clean and perform maintenance on the plant's coal-handling equipment, which Westar considers as crucial for effective use of the coal. "We're proud of this," said Karla Olsen, a Westar spokeswoman. "We're able to keep things safe and clean."
Related News
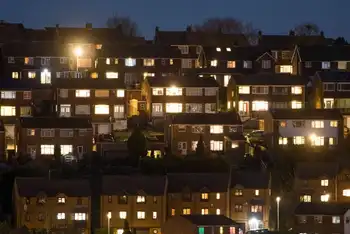
Power Demand Seen Holding Firm In Europe’s Latest Lockdown
BERLIN - European power demand is likely to hold up in the second round of national lockdown restrictions, with fluctuations most likely driven by changes in the weather.
Traders and analysts expect normal consumption this time around as home heating during the chilly season replaces commercial demand.
Last week electricity consumption in France, Germany and the U.K. was close to business-as-usual levels for the time of year, according to BloombergNEF data. By contrast, power demand had dropped 16% in the first seven days of the springtime lockdown.
How power demand performs has significance outside the sector. It’s often seen as a proxy for…