Transformer Mounting Pad Explained
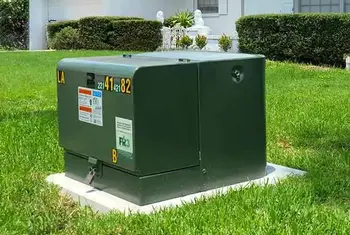
A transformer mounting pad is a crucial element in the electrical distribution system, especially for pad-mounted transformers. These pads ensure the electrical infrastructure's stability, safety, and efficiency, whether in urban settings, customer service areas, or specialized environments like data centers.
A transformer mounting pad is an often overlooked yet crucial component of electrical infrastructure, providing the foundation for installing transformers. These platforms serve multiple critical functions, ensuring electrical power distribution systems' safe, reliable, and efficient operation.
Electrical Transformer Maintenance Training
Substation Maintenance Training
Request a Free Training Quotation
What is a Transformer Mounting Pad?
A mounting pad is a specially designed platform constructed to support a transformer. It's typically made of sturdy materials like concrete, polymer concrete, or fiberglass, chosen for their strength, durability, and electrical insulating properties. The pad's dimensions and specifications are carefully engineered to accommodate the specific transformer it will house.
Purpose of a Transformer Mounting Pad
Mounting pads fulfill several key purposes:
- Structural Support: They provide a stable and level base for the transformer, ensuring it remains securely in place even under heavy loads or environmental stresses.
- Electrical Insulation: Pads act as an insulating barrier between the transformer and the ground, protecting personnel and equipment from electrical hazards.
- Environmental Protection: They shield the transformer from moisture, debris, and other environmental factors that could compromise its operation.
- Thermal Management: Some pad designs incorporate features to facilitate heat dissipation, ensuring that the transformer operates within safe temperature limits.
- Safety: A stable mounting pad prevents the transformer from tipping or shifting, which could lead to dangerous high and low voltage connections becoming exposed or damaged.
- Protection: It shields the transformer from ground moisture and contaminants, such as mineral oil leaks, which could cause deterioration or failure.
- Accessibility: Mounting pads elevate transformers to a height that makes maintenance and inspections easier, ensuring customer service personnel can perform their duties safely and efficiently.
Materials Commonly Used for Transformer Mounting Pads
Various materials are employed in the construction of mounting pads, each with its own advantages:
- Concrete: This is the most widely used material due to its strength, durability, and resistance to environmental factors.
- Polymer Concrete: A composite material that offers similar strength to traditional concrete but with added resistance to chemical and environmental damage.
- Steel-Reinforced Concrete: For applications requiring additional strength, such as data centers or high-capacity installations, steel reinforcement provides extra durability and load-bearing capacity.
Factors to Consider When Designing a Transformer Mounting Pad
Designing a mounting pad requires careful consideration of several factors:
- Transformer Size and Weight: The pad's dimensions and load-bearing capacity must be adequate to support the specific transformer's weight and footprint.
- Soil Conditions: The pad's foundation must be engineered to account for the soil's load-bearing characteristics and potential for settling or shifting.
- Environmental Factors: The pad's material and design should be resistant to moisture, temperature fluctuations, chemicals, and other environmental factors prevalent in the installation area.
- Electrical Requirements: The pad must meet electrical insulation standards to ensure safety for personnel and equipment.
- Accessibility: If the pad will house padmounted transformers with high and low voltage connections, accessibility for maintenance and repairs should be factored into the design.
Types of Transformer Mounting Pad Configurations
Mounting pads come in various configurations to suit different installation scenarios:
- Slab-on-Grade: This is the most common and simplest type, consisting of a solid concrete slab poured directly on the ground.
- Pier Foundation: Elevated pads supported by concrete or steel piers are used in areas with poor soil conditions or potential for flooding.
- Precast Concrete Pads: These are prefabricated pads that offer quick and easy installation, ensuring consistent quality.
- Custom-Designed Pads: For unique site conditions or large transformers, custom pads can be designed and fabricated to meet specific requirements.
Maintenance of Transformer Mounting Pads
Regular maintenance is essential to ensure the longevity and effectiveness of transformer mounting pads:
- Inspection: Periodic inspections should be conducted to check for cracks, settling, or other structural issues that could compromise the pad’s integrity.
- Cleaning: Remove debris, dirt, and vegetation from around the pad to prevent moisture buildup and ensure clear access for maintenance personnel.
- Sealant Application: Applying sealants can help protect concrete pads from moisture infiltration and chemical damage, particularly in areas where mineral oil leaks are a concern.
- Repair: Any identified damage, such as cracks or spalling, should be promptly repaired to prevent further deterioration and maintain the pad's stability.
Transformer mounting pads are unsung heroes in electrical power distribution. They provide the vital foundation for transformers, ensuring their safe and reliable operation, protecting valuable equipment, and ultimately contributing to uninterrupted customer service. Whether it's a simple slab-on-grade pad for a residential distribution transformer or a custom-designed platform for a large industrial installation, mounting pads play a critical role in powering our modern world.
As technology advances and the demand for electricity grows, mounting pads will continue to evolve, incorporating new materials and design features to meet the challenges of an increasingly complex electrical grid. Understanding their purpose, design considerations, and maintenance requirements is essential for ensuring the safe and efficient delivery of electrical power for years to come.
On-Site Training
Interested in cost effective, professional on-site electrical training?
We can present an Electrical Training Course to your electrical engineering and maintenance staff, on your premises, tailored to your specific equipment and requirements. Click on the link below to request a Free quotation.
EF PARTNER MEDIA
Videos
Product Showcases
Shared Media