Lockout Tagout Training
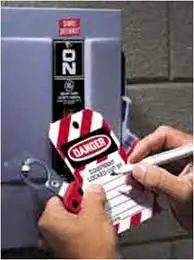
Effective lockout tagout training is more than just a regulatory requirement—it's a critical component of a robust safety culture. Under OSHA 1910.147(c)(7), employers are responsible for ensuring that employees are trained to understand and safely apply energy control procedures. For safety managers and EHS professionals, this means developing a structured, role-specific educational program that evolves with your equipment, processes, and workforce.
Under 29 CFR 1910.147, the control of hazardous energy is a critical component of workplace safety, and the lockout tagout standard outlines specific training requirements to ensure employees can perform energy isolation safely and effectively. The Occupational Safety and Health Administration requires all authorized, affected, and other employees to receive instruction tailored to their roles, including instruction on lockout and tagout procedures. Employers must verify that each worker understands the program and demonstrate successful completion of the instruction through practical evaluation and documentation. For a full summary of OSHA's training requirements, see our OSHA Lockout Tagout Training page.
This guide outlines best practices for implementing and maintaining a successful in-house LOTO training program.
Structuring Your Internal Lockout Tagout Training Program
A well-structured LOTO training program should be both comprehensive and role-specific. Begin by identifying the employees who fall into the three OSHA-defined categories:
-
Authorized employees – those who perform LOTO procedures.
-
Affected employees – those who operate or use the equipment being serviced.
-
Other employees may be in the area where LOTO is applied but are not directly involved.
Each group requires a different level of instruction. The program should include a mix of theoretical instruction, equipment-specific demonstrations, and practical assessments to ensure workers can perform tasks correctly.
Components of a solid structure:
-
Classroom or online instruction on energy control concepts
-
Hands-on practice with actual lockout devices used on-site
-
Written or verbal testing for knowledge retention
-
Performance evaluations by supervisors or trainers
-
Refresher instruction based on audits or operational changes
Tailoring Training by Equipment or Industry
No two facilities are alike. Your LOTO training program must reflect the specific types of hazardous energy present in your operation. For example, manufacturing environments often require mechanical and pneumatic isolation instruction, while electrical utilities may focus heavily on breaker lockouts and high-voltage disconnects.
Customize instruction to include:
-
Common equipment shutdown procedures unique to your plant
-
Specific energy isolating devices and tags used
-
Differences between electrical, hydraulic, pneumatic, and thermal energy risks
-
Job-specific risks and lockout points for maintenance vs. operations roles
Industry-specific instruction examples:
-
In food processing: Emphasis on sanitation cycles and shift changes
-
In construction: Focus on mobile equipment and multi-employer job sites
-
In manufacturing: Detailed walkthroughs for conveyor systems, presses, or CNC machines
Documentation and Compliance Tracking
Thorough documentation is not just a best practice—it’s a compliance requirement. You must keep accurate records showing that employees have received the correct instruction for their roles and that they understand and can safely apply the procedures.
Maintain documentation for:
-
Course dates and frequency
-
Names of trained employees and their job classifications
-
Instructors or course providers
-
Content covered (slides, manuals, quizzes, checklists)
-
Results of knowledge checks and performance evaluations
Make sure records are easily accessible during audits or inspections. Use a digital Learning Management System (LMS) or organized paper system, depending on your facility’s size and structure.
Schedules and Refresher Plans
While OSHA does not mandate a specific frequency for refresher instruction it does require retraining whenever:
-
Job duties change
-
New machines or processes are introduced
-
An employee demonstrates inadequate understanding or fails to follow procedures
-
Annual LOTO audits reveal knowledge gaps
Best practice: Implement a recurring refresher cycle—such as every 12 or 24 months—for all authorized and affected employees. Use toolbox talks, short quizzes, or scenario-based exercises to reinforce learning between formal sessions.
Suggested course plan:
-
New hires: Full LOTO training within the first 30 days
-
Annual audit follow-ups: Immediate retraining if deficiencies are noted
-
Refresher sessions: Every 12–24 months, with role-specific focus
-
Post-incident reviews: Mandatory retraining if an energy control failure occurs
Training for New Hires, Contractors, and Temporary Workers
New employees and temporary staff are often at higher risk of injury due to lack of familiarity with procedures. Your program should include a fast-track but thorough onboarding process for these individuals.
Tips for onboarding:
-
Include LOTO awareness in all new-hire safety orientations
-
Ensure that only trained and authorized employees apply or remove LOTO devices
-
Provide written job aids, diagrams, or short videos for equipment-specific procedures
-
Supervise new workers closely during their first LOTO tasks
For contractors, ensure your company’s LOTO program is clearly communicated and that their procedures are compatible with yours. Written coordination and pre-job meetings are essential.
Designing an effective in-house LOTO training program requires more than covering OSHA’s minimum requirements—it demands customization, structure, and consistency. By tailoring instruction to your equipment, workforce, and industry risks, and by maintaining strong documentation and retraining protocols, you can create a program that not only keeps your operation compliant but also saves lives.
A successful LOTO course program reflects your organization’s commitment to safety and operational excellence—starting with the people who power your facility daily.
Read More About Lockout Tagout
On-Site Training
Interested in cost effective, professional on-site electrical training?
We can present an Electrical Training Course to your electrical engineering and maintenance staff, on your premises, tailored to your specific equipment and requirements. Click on the link below to request a Free quotation.
EF PARTNER MEDIA
Product Showcases
Shared Media