What Are You Responsible for When Working with Power Lines?
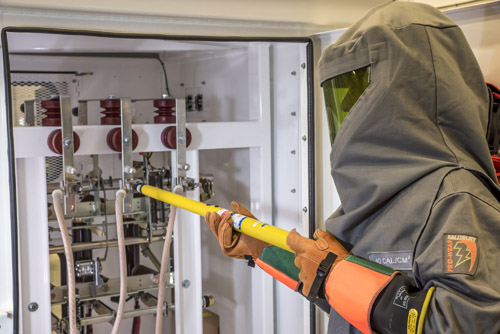
Working with power lines requires strict adherence to safety guidelines to prevent serious injury or even fatalities. Both workers and employers share the responsibility of ensuring that proper procedures are followed when working around live wires or performing maintenance on de-energized lines. Let's address key responsibilities and safety precautions to protect workers from electrical hazards and maintain compliance with industry standards.
Request a Free Training Quotation
What Safety Precautions Must You Take When Working Near Overhead Power Lines?
When working near overhead lines, maintaining a safe distance is critical to avoid accidental contact with energized conductors. According to established safety standards, the minimum distance should be at least 10 feet for lines carrying up to 50 kV, with greater distances required for higher voltage lines.
The following are essential safety precautions to take:
- Establish safe working distances: Workers should always maintain safe clearance, especially when using equipment such as cranes, ladders, or aerial lifts that can reach overhead lines.
- Stay aware of the surroundings: Workers should assess the work area for potential hazards, such as nearby trees or structures, that could interfere with power lines.
- Use barriers and signs: When necessary, use non-conductive barriers and signs to alert workers and the public to the presence of power lines.
- Do not touch any object in contact with lines: Never attempt to move or touch objects that are in contact with live lines, such as ladders or scaffolding. Workers must assume that all lines are energized unless proven otherwise.
Who Is Responsible for Ensuring That Power Lines Are De-Energized Before Work Begins?
The responsibility for de-energizing power lines before work begins is a shared one. Employers are required to coordinate with utility companies or the power provider to ensure the lines are properly shut down and grounded. Workers must be informed and trained to confirm that the de-energization process has been completed before commencing any work.
Before work begins, the following steps should be taken:
- Notify the utility company: Employers should contact the local utility provider to arrange for lines to be de-energized.
- Verify the status of the lines: Workers must use testing devices to ensure that the lines are not live. Visual checks alone are not sufficient.
- Use grounding equipment: After de-energizing, grounding equipment should be applied to prevent unexpected re-energization.
It is essential that only authorized and trained personnel manage this process, and it should never be left to workers without proper knowledge or certification.
What Personal Protective Equipment (PPE) Is Required When Working Around Energized Power Lines?
Using the correct personal protective equipment (PPE) is vital to protect workers from electrical hazards, such as electrocution or burns from arc flashes. The PPE required for working near or on energized lines includes:
- Insulated gloves: These gloves should be rated for the voltage being worked on, providing protection against electrical shock.
- Insulated boots: Workers must wear boots with dielectric soles to reduce the risk of electric shock, particularly when working in wet conditions or near grounded surfaces.
- Hard hats and face shields: These are essential for protecting workers from falling debris, sparks, or arc flashes.
- Flame-resistant clothing: This clothing helps protect against burns from electrical arcs. The materials should be arc-rated to provide adequate protection based on the incident energy level.
- Safety harnesses and lanyards: When working at heights, such as on utility poles, fall protection is necessary to prevent injuries from falls.
Each piece of PPE must be inspected regularly to ensure it is in good working condition, free from damage or defects.
How Do You Ensure Compliance with Safety Standards When Working with Power Lines?
Compliance with safety standards is critical for preventing accidents and maintaining a safe work environment. Both employers and workers must follow guidelines set by organizations such as OSHA to ensure proper procedures are in place. Key elements of compliance include:
- Adhering to OSHA guidelines: Employers are responsible for providing training on OSHA's safety standards for working around power lines, including lockout/tagout procedures and the use of PPE.
- Implementing lockout/tagout procedures: These procedures ensure that any equipment being repaired or maintained is completely de-energized and cannot accidentally be re-energized. This involves isolating the power source, locking controls, and tagging them to prevent activation.
- Regular inspections and maintenance: Employers should conduct regular inspections of all equipment and lines to identify potential hazards before they become dangerous. This also includes verifying that all PPE is in good condition.
Failing to comply with these standards can result in severe penalties for the employer and increased risks for the workers.
What Are the Responsibilities of a Worker and Employer in Preventing Electrical Hazards When Working with Power Lines?
Preventing electrical hazards is a joint effort between workers and employers. Employers are responsible for providing a safe working environment, proper equipment, and adequate training. Workers, on the other hand, are responsible for following the safety procedures and using the equipment provided correctly.
The responsibilities of employers include:
- Providing proper PPE: Employers must ensure that workers have access to the necessary PPE for their tasks and that it is maintained and inspected regularly.
- Conducting safety training: Workers should receive regular training on the risks associated with working near live lines and how to avoid them.
- Ensuring de-energization and lockout/tagout procedures: Employers must coordinate with the utility company to de-energize lines and ensure proper lockout/tagout procedures are followed.
The responsibilities of workers include:
- Using PPE correctly: Workers must wear the provided PPE at all times and ensure that it is properly maintained.
- Following safety protocols: Workers should adhere to all training and safety protocols, such as maintaining safe distances from lines and using non-conductive tools.
- Reporting hazards: Any hazards or concerns, such as damaged PPE or faulty equipment, should be reported to supervisors immediately.
By working together, both employers and workers can significantly reduce the risk of accidents and injuries when working with power lines.
Working near power lines involves inherent risks that can be mitigated by following proper safety precautions, using the correct PPE, and adhering to de-energization and lockout/tagout procedures. Both employers and workers share responsibility in ensuring these safety standards are maintained. By staying compliant with industry regulations, conducting regular inspections, and fostering a culture of safety, the risk of electrical hazards can be greatly reduced.
On-Site Training
Interested in cost effective, professional on-site electrical training?
We can present an Electrical Training Course to your electrical engineering and maintenance staff, on your premises, tailored to your specific equipment and requirements. Click on the link below to request a Free quotation.
EF PARTNER MEDIA
Product Showcases
Shared Media