Industrial Automation and Communication Networks
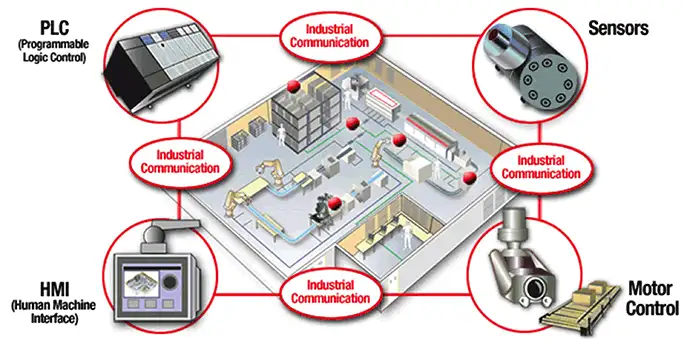
In the early 20th century, process control systems and the manufacturing systems were designed based primarily on the mechanical technology and with analog devices. After the period, the pneumatic control technology and the hydraulic power were introduced. The pneumatic control technology made it possible to control remote systems by a centralized control system. These technologies are still very common.
At the beginning of 1960, a digital computer was for the first time really applied as a digital controller. The term direct digital control (DDC) was used to emphasize that the computer directly controls the process. In the 1960s, the application of a minicomputer was still a fairly expensive solution for many control problems. In the meantime, programmable logic controller (PLC) was developed and it replaced the conventional, relay-based controller, having relatively limited control functions. In addition, many technologies were developed for machine tools and discrete production processes. The numerically controlled (NC) machine tool became to be controlled by computers and the robot was developed in this period.
With the more widespread use of digital computers and the associated technologies, industrial communication networks became to be developed with or converted to digital transmission. Proprietary digital communication networks for industrial use started in the 1960s as computers for automation systems were first linked together.
In mid 70s, the first distributed computer control system (DCCS) was announced by Honeywell as a hierarchical control system with a large number of microprocessors. Since its introduction in mid 1970s, the concept of the DCCS spread widely in many industrial automation systems such as power plant control systems, manufacturing systems, etc. The installation of distributed control systems in the newly planned plants or replacement of existing analogue or centralized control systems is presently a common decision of enterprise management.
The use of local area networks to interconnect computers and automation devices within an industrial automation system has become popular since 1980. The high capacity low cost communication offered by local area networks has made distributed computing a reality, and many automation services. The
industrial automation systems are often implemented as an open distributed architecture with communication over digital communication networks.
It is now common for users connected to a local area network to communicate with computers or automation devices on other local area networks via gateways linked by a wide area network.
As the industrial automation systems becomes large and the number of automation devices increases, it has become very important for industrial automation to provide standards which make it possible to interconnect many different automation devices in a standard way. Considerable international standardization efforts have been made in the area of local area networks. The Open Systems Interconnection (OSI) standards permit any pair of automation devices to communicate reliably regardless of the manufacturer.
Industrial networks span many manufacturing applications. Standard industrial networks using digital communication technologies cover a wide range of manufacturing applications. In many applications, the types of devices and performance determine the type of network. Contrast the needs of two devices -- a proximity sensor used on a conveyor belt compared to a control valve used in a petroleum refinery. The proximity sensor has a single function - to transmit a Boolean on/off signal indicating the proximity of an object. We can accommodate this signal in a few bits of data. Diagnostic information from the sensor is probably limited to a single "health" indicator, which again requires very little data. However, we can expect the control valve to provide very sophisticated control functions and diagnostics, such as number of cycles since last servicing, packing friction, and ambient operating temperature. These parameters can be extremely critical in an environment such as a refinery -- failures can result in dangerous situations and costly downtime. Clearly, the proximity sensor and the control valve have different network requirements. Therefore, different types of industrial networks must address a variety of different needs. We must select the right network to address our specific application requirements.
What is an Industrial Network? By definition, an industrial network requires geographical distribution of the physical measurement I/O and sensors or functional distribution of applications. Most industrial networks transfer bits of information serially. Serial data transfer has the advantage of requiring only a limited number of wires to exchange data between devices. With fewer wires, we can send information over greater distances. Because industrial networks work with several devices on the same line, it is easier to add a new device to existing systems.
To make all this work, our network must define a set of rules -- a communication protocol -- to determine how information flows on the network of devices, controllers, PCs, and so on. With improved communication protocols, it is now possible to reduce the time needed for the transfer, ensure better data protection, and guarantee time synchronization, and real-time deterministic response in some applications. Industrial networks also ensure that the system sends information reliably without errors and securely between nodes on the network.
For the lower level communication network for industrial automation, the industrial local area network solutions such as MAP are too expensive and/or do not reach the required short response times, depending on the application. The fieldbuses have been, therefore, developed to meet these requirements, and many efforts are now being made to make fieldbus standards for industrial automation applications.
Read More: Hierarchical Levels in Industrial Communication Networks
On-Site Training
Interested in cost effective, professional on-site electrical training?
We can present an Electrical Training Course to your electrical engineering and maintenance staff, on your premises, tailored to your specific equipment and requirements. Click on the link below to request a Free quotation.
EF PARTNER MEDIA
Product Showcases
Shared Media