Efficiency Opportunities Through Motor Maintenance
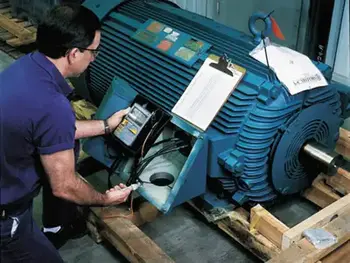
The electricity consumed by a motor in one year costs more than the motor itself, by as much as 10 times. Multiplying this cost by the life of the motor puts the necessity of maintaining optimum motor performance in true perspective. Motor maintenance is more than making sure the motor itself is operating correctly. It also involves ensuring that power supplied to the motor is within acceptable tolerances, that the motor’s output power is efficiently transmitted to the load and that the load itself is properly maintained so as not to make the motor work harder than necessary. Record keeping is an essential part of motor maintenance. Comparing results of recent tests to historical records, maintenance staff can much more readily spot degraded performance and potential breakdowns and take steps to adjust the system and avoid costly unscheduled downtime. Motor maintenance programs must be customized. Hot, dirty, humid conditions require more frequent checks of performance and attention to maintaining the physical condition of the motor. It may also be necessary to isolate motors from extreme conditions or to blow conditioned air over them for cooling purposes.
HOW MOTOR MAINTENANCE SAVES ENERGY
Motors eventually become less efficient through wear, breakdown of lubricants and falling out of alignment. Scheduled maintenance is the best way to keep the whole system operating within acceptable tolerances. Properly applied, maintenance will also provide valuable information on potential motor failure so that unscheduled downtime can be minimized.
MOTOR MAINTENANCE ENERGY-SAVING STRATEGIES
The greatest enemies of efficient motor operation are improper installation or adjustments, low-quality electrical power, adverse environmental conditions (e.g., dust, dirt, moisture, extreme temperature) and wear. The general guidelines in this section address these issues.
MOTOR MAINTENANCE LOGS
A motor maintenance program is of most value when it is consistently applied. The system should remind staff when it is time to perform specific maintenance functions on individual motors; provide a means of recording the functions performed; and act as an historical record to track the performance of individual motors. Each motor should have a maintenance form, recording the load served (e.g. supply fan #1 or boiler feedwater pump #3) and the motor’s make, model, serial number and ratings. Specifications for ancillary equipment (e.g., drive belts, pulleys) should be recorded for quick reference. Space should be provided for recording observations of unusual motor performance. Computerized maintenance programs are available that will notify plant personnel of upcoming motor maintenance. These programs also provide a convenient repository for information on all motors (plus other systems that require maintenance) and analysis tools for determining how effectively maintenance is being carried out.
PROPER LUBRICATION
Proper lubrication is essential to long operating life for motors and all mechanical equipment. It must be done periodically and consistently — it is too late when the motor audibly communicates its needs. Many times service personnel try to quiet a noisy motor by pumping lubricant into the bearing. This may work for a short while but the life of a noisy bearing is limited and over-lubrication (as described below) may result.
SHAFT ALIGNMENT
Larger motors are usually coupled to their loads and proper shaft alignment is important to adequate bearing life. In belt-driven applications, belts must be perpendicular to the shaft axes or they will wear and bearing life will be shortened. Alignments made under one set of circumstances can change due to temperature, loading, foundation movement and rotational speeds.
BEARING MAINTENANCE
All bearings require maintenance to perform properly and achieve their service lives. Bearings can be classified as sleeve or anti-friction types. In sleeve bearings, the shaft rides in a thin film of lubricant between the shaft and the bearing. Antifriction bearings have ball or roller bearings that spin between the shaft and the bearing housing. There is considerable overlapping in the use of both types in electric motors. Proper maintenance consists simply of keeping the bearing clean, lubricated and loaded not in excess of its rating.
POWER QUALITY
Power quality can have a large impact on motor performance. Motors are designed with the assumption that electric power will be provided within certain tolerances. It is easy to assume that because motors are operating, the power is within acceptable tolerances, but this is not always true. Power quality can be degraded as it is supplied from the utility or at the facility; in either case, it is necessary to identify the cause and correct it. Important power quality issues are discussed below.
FACTORS AFFECTING MOTOR MAINTENANCE COSTS
Motor maintenance costs will be influenced by ongoing costs such as: testing, inspecting, cleaning and drying; parts for repairs; consumables (e.g., lubricants, belts, etc.); and labor. Costs will be increased directly as the frequency of maintenance activities is increased. In addition, one-time costs may be incurred from time to time to correct problems associated with power supplied to the motors. The level of testing performed on motors determines the cost of such testing. These tests can be as simple as having maintenance personnel take voltage and current draw measurements, or as sophisticated as comprehensive motor circuit analysis tests. Actual costs for testing and repairs should be obtained from providers of these services. If the motor is in a particularly dirty or hot location, it will require as much as six times as much attention. It is essential that motors be selected based on the environment in which they will be operating. It may also be desirable to isolate the motor from the environment with barriers or filters and cooling air in order for the motor to operate within design limits.
From: Electric Motors and VFDs Handbook, Vol 3, The Electricity Forum
On-Site Training
Interested in cost effective, professional on-site electrical training?
We can present an Electrical Training Course to your electrical engineering and maintenance staff, on your premises, tailored to your specific equipment and requirements. Click on the link below to request a Free quotation.
EF PARTNER MEDIA
Product Showcases
Shared Media