Power Quality Troubleshooting Explained
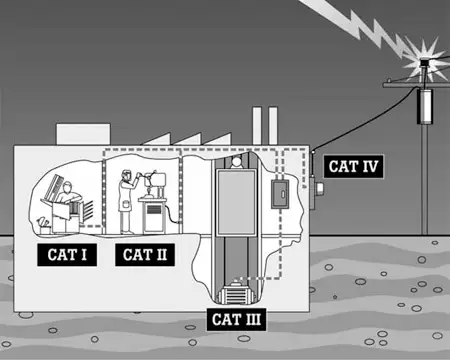
Power quality troubleshooting is essential for identifying and resolving issues that disrupt the efficiency and reliability of electrical systems. Poor power quality (PQ)—caused by voltage sags, surges, harmonic distortion, and other irregularities—can lead to equipment malfunctions, reduced operational lifespan, and costly downtime. For businesses and electrical professionals, understanding and addressing PQ issues is crucial to maintaining optimal system performance, preventing costly repairs, and enhancing safety. Effective power quality troubleshooting enables professionals to diagnose underlying problems, ensure stable power flow, and protect sensitive equipment, making it a vital practice in today’s energy-dependent environments.
Power Quality Analysis Training
Request a Free Power Quality Training Quotation
Effective troubleshooting ensures stable power supply, mitigates power quality events, and safeguards process control systems, making it a vital practice in today’s energy-intensive environments.
The symptoms of poor PQ include intermittent lock-ups and resets, corrupted data, premature equipment failures, and overheating of components for no apparent cause. These issues result in downtime, decreased productivity, and frustrated personnel. This article provides insights on PQ problems and initiating effective solutions. Before starting any measurements, it is critical to consider the following precautions:
All measurements should only be performed by qualified personnel trained to safely analyze PQ, using appropriate procedures and tools rated for work on electrical systems.
While suggested solutions are consistent with the National Electric Code (NEC) to the best of our knowledge, all NEC requirements must be followed without exception.
The information presented here aims to assist professionals but is not a substitute for the specialized knowledge and experience of expert PQ practitioners.
This document serves as a “starter kit” for PQ troubleshooting, not a definitive guide.
Start at the Scene of the Issue
To address PQ problems, begin troubleshooting as close to the “victim load” as possible. The victim load often includes sensitive equipment such as electronic devices or systems that malfunction due to poor PQ. Part of the diagnostic process involves isolating PQ issues from other potential causes such as hardware or software faults. Like any detective, you should “start at the scene of the crime” and take basic measurements.
Alternatively, you may begin at the service entrance using a three-phase monitor and work downstream to the victim load. This method is particularly useful if the PQ problems originate with the utility. However, surveys consistently reveal that most PQ problems stem from within the facility’s distribution systems. PQ generally deteriorates as you move downstream through the system due to factors such as load conditions, capacitor banks, and wiring or grounding issues. In fact, 75% of PQ problems are related to wiring and grounding errors.
For these reasons, many PQ experts recommend starting with a comprehensive assessment of the building’s electrical infrastructure. A logical troubleshooting flow often involves first diagnosing the infrastructure, followed by monitoring the system as needed. This bottom-up troubleshooting approach helps identify and resolve issues effectively.
First Steps
Create a One-Line Diagram: A current one-line diagram of the site is invaluable when troubleshooting PQ problems. This diagram identifies AC electrical sources, distribution systems, and the loads they serve. If you work on-site, the layout may already exist in your mind, but having it on paper benefits everyone involved.
For professionals visiting a new site, creating an up-to-date one-line diagram helps identify recent changes in the system, such as new power factor correction capacitors or additional loads. Systems are dynamic and evolve over time, often in unplanned ways. Some problems may originate locally, while others result from interactions between different parts of the electrical system.
Understanding these interactions is key to diagnosing power quality issues. Comprehensive documentation enhances your ability to analyze and address problems, though it’s often the most disorganized sites that require the most assistance. Consultants frequently earn their fees by updating existing documentation to reflect the actual system configuration. The goal at this stage is to gather as much accurate information as possible, even if complete documentation is unavailable.
Monitoring and Resolving Problems
When conducting a power quality survey, pay close attention to single phase and three phase systems. Monitor for events such as harmonic distortion, voltage imbalances, and transients. Use tools capable of analyzing total harmonic distortion and identifying problematic load conditions. In many cases, equipment failures can be traced to insufficient PQ management.
Consider the role of capacitor banks and power factor correction capacitors in stabilizing the system. Properly functioning capacitors improve efficiency and reduce harmonic distortion, but poorly maintained or improperly configured units can exacerbate PQ issues. Investigate how reenergizing systems after a power failure affects the overall stability of the electrical system.
Power Quality Troubleshooting requires a methodical approach and a clear understanding of the site’s electrical system. By analyzing power quality, identifying the root causes of power quality problems, and implementing corrective measures, you can enhance system reliability, protect sensitive electronic equipment, and maintain efficient operations. Monitoring load conditions, addressing wiring and grounding issues, and maintaining capacitor banks are critical steps in resolving PQ issues and ensuring optimal performance.
On-Site Training
Interested in cost effective, professional on-site electrical training?
We can present an Electrical Training Course to your electrical engineering and maintenance staff, on your premises, tailored to your specific equipment and requirements. Click on the link below to request a Free quotation.
EF PARTNER MEDIA
Product Showcases
Shared Media