A new way to capture waste heat
A few decades ago, many processes wasted energy and no one got very excited. With rising energy costs and a growing need to reduce carbon dioxide and other emissions, its different today.
So when an entirely new technology for heat recovery becomes available to industry, smart operators pay attention.
Such a process is the Organic Rankine Cycle ORC. Industrial and mechanical engineers are familiar with the Rankine Cycle. Its the thermodynamic process described by 19th century Scottish physicist William Rankine for extracting work from steam. It is the familiar process used in combinedcycle generators. The steambased Rankine cycle is great for extracting waste heat from high temperature sources, such as gas turbine exhausts. This energy can then be used to spin a steam turbine to generate additional electric power. However, for heat sources less than perhaps 500°F its not as practical.
Thats where the ORC comes in. By using as a working fluid an organic fluid that vaporizes at a temperature far lower than water, the Rankine cycle can be used in the same way to extract otherwise wasted energy from fluids with temperatures as low as 150°F. Heat is extracted from the fluid in a heat exchanger, vaporizing the organic working fluid. The organic fluid in its gas form can then spin a turbine and generate useful electric energy. The produced power can be used on site or sold. The turbine exhaust returns the fluid to the heat exchanger for another shot of energy. A whole new world of heat recovery options opens up.
The ORC is already widely used for energy recovery from gas pipeline compressors and in geothermal power plant applications, and is increasingly being applied in solar collector applications. In all of these situations, waste heat energy generates electric power to supplement electric requirements for the site, or is sent to the electric utility grid. ORC can also be used to generate electricity in industrial applications.
According to Gordon Foster from Calnetix, a manufacturer of ORC systems, “The early adopters in the U.S. tend to be in states that have investment credit or production credit programs for recovering waste heat to produce electricity. Companies in states without incentives but with high electricity rates are also candidates.” According to Foster, paybacks for industrial customers tend to be from three to five years.
If your industrial plant has the right characteristics, the ORC may be a great tool for increasing energy efficiency. Possible sources of waste heat for an application include oven or furnace exhausts, cement kilns, petrochemical processing exhausts, incinerators or other flue gas discharges, and process water or other fluids in the food processing, plastics, or metal treating industries.
Foster indicates that in assessing suitability of a process for ORC, it is important to gather information on temperature and flow rate of the heat source, and also information on ambient wet bulb and dry bulb temperatures. He notes, “Even if the heat source is adequate, high temperature and humidity locations do not tend to pencil out.”
Ormat Technologies, Inc. is a vertically integrated provider and operator of large ORC systems. The company provides support to utilities and industry, as well operating its own geothermal ORC plants. Paul Thomsen, Director of Public Policy and Business Development from Ormat, indicates that right now the firm is also seeing large energy potential in the cement industry, as well as in lower temperature gas turbine heat exhausts, and pipeline compressor stations. According to Roni Omessi, Ormats Senior Director of Recovered Energy, industrial energy users should look for waste heat streams between 200°F and 350°F for the greatest opportunities in energy recovery.
Omessi says, “Look for sources with temperatures above 200°F not being utilized by other heat recovery methods.” It is true that at the lower end of the range, the necessary size of the heat exchanger increases, conversion efficiency is lower and capital costs increase. However, if this is a heat source that would otherwise be wasted, conversion efficiency may not be critical.
According to Omessi, ORC providers such as his firm can work with industrial customers in assessing their waste heat stream, then design a system and choose an organic working fluid to maximize heat recovery. He notes that with the companys experience in these applications, they can make available simple and reliable designs. One of the newer features of commercial ORC systems is their potential for remote operation.
Omessi says, “This is especially attractive for remote sites or for large industrial facilities. The system controls can be located at a convenient central location.”
Another important provider of ORC equipment is Pratt & Whitney, a United Technologies company. According to Jeff Jurgensmier, Engineering Communications Manager for the firm, Pratt & Whitney Power Systems offers a 280 kW machine, and also a family of larger ORC equipment from Italian partner, Turboden. The Turboden product line ranges from 400 kW to 4MW, and above. The two companies combined now have 160 ORC power generating systems in 14 countries.
Jurgensmier indicates that the companys primary interest in North America to date has been natural geothermal resources. However, he adds, “There are many waste heat opportunities, including biomass burners, reciprocating engine and turbine exhausts, gas compression stations, etc.” He adds, “Other heat or power intensive industries such as glass, refineries, steel, thermal oxidizers and cement all have great potential. We continue to find new applications for ORC technology.”
He adds that until quite recently, smaller energy sources — less than one megawatt — generally could not take advantage of the merits of ORC technology. With smaller systems such as Pratt & Whitneys PureCycle 280 280 kW, that has changed. ORC is now practical for smaller heat sources.
According to Paul Thomsen from Ormat, heat recovery systems using ORC technology may qualify for federal tax credits of from 10 to 30. Also important is the fact that electric generation using ORC equipment for heat recovery may qualify for renewable portfolio credits in many states. Companies that are attempting to reduce carbon emissions can increase their onsite energy potential without increasing emissions.
Not every industry can take advantage of ORC technology. But if you have a continuous stream of hot water or other fluids – typically between 200°F and 500°F – on which you are not already doing heat recovery, this may be both a solution and an opportunity. If you are facing high electric rates or growing demand charges, its definitely worth looking into.
Related News
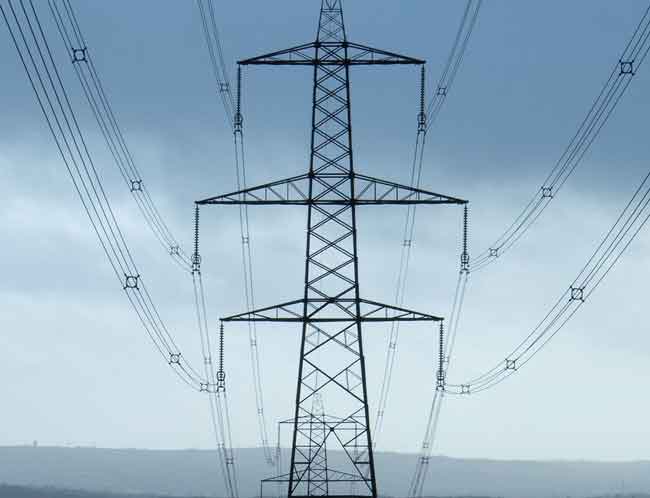
London Gateway Unveils World’s First All-Electric Berth
LONDON - London Gateway, one of the UK’s premier deep-water ports, has unveiled the world’s first all-electric berth, marking a significant milestone in sustainable port operations. This innovative development aims to enhance the port's capacity while reducing its environmental impact. The all-electric berth, which powers vessels using electricity instead of traditional fuel sources, is expected to greatly improve operational efficiency and cut emissions from ships docking at the port.
The launch of this electric berth is part of London Gateway’s broader strategy to become a leader in green logistics, aligning with the UK’s ambitious climate goals. By transitioning to electric…