Oil For Transformers - Efficient Operation
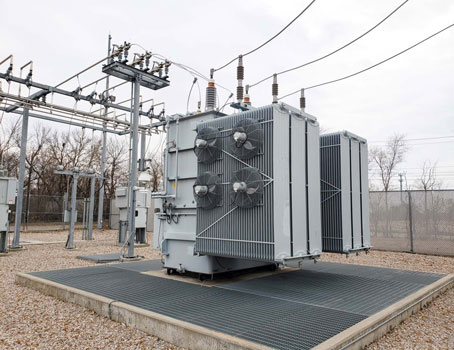
Oil for transformers acts as a vital dielectric fluid, providing insulation, cooling, and arc suppression. By reducing heat buildup and protecting internal components, high-quality transformer oil ensures safe, efficient, and long-lasting performance in power and distribution systems.
What is Oil for Transformers?
Oil for transformers is a specialized insulating and cooling medium used in electrical transformers. It ensures safe, efficient, and long-lasting operation.
✅ Provides electrical insulation between windings and core
✅ Dissipates heat to prevent overheating and equipment failure
✅ Suppresses arcing and prolongs unit service life
Electrical Transformer Maintenance Training
Substation Maintenance Training
Request a Free Training Quotation
Oil for transformers plays a critical role as a dielectric fluid, ensuring the safe and efficient operation of electrical transformers. The type of fluid used maintains the integrity of both paper insulation and solid insulation, ensuring efficient performance in fluid-filled electrical systems.As an insulating medium, it not only prevents electrical breakdown but also helps in cooling the equipment by dissipating the heat generated during operation. Equipment liquid, typically mineral-based or synthetic, is designed to offer excellent electrical insulation properties, enhance operational longevity, and protect against faults or failures. This fluid is essential for maintaining the equipment’s performance, safeguarding against short circuits, and improving overall system reliability. In this article, we’ll explore the importance of liquid in equipment, its types, and why it's crucial for both electrical safety and efficiency.
Transformer Oil Comparison Table
Oil Type | Key Features | Advantages | Limitations |
---|---|---|---|
Mineral Oil | Petroleum-based dielectric fluid | Cost-effective, excellent cooling performance | Flammable, environmentally harmful, prone to aging |
Silicone Oil | Synthetic, thermally stable | Fire-resistant, high flash point, long lifespan | Expensive, limited biodegradability |
Synthetic Ester | Man-made ester-based fluid | Biodegradable, high fire safety, stable at high temperatures | Higher cost, limited field experience |
Natural Ester (Vegetable Oil) | Derived from renewable plant oils | Sustainable, biodegradable, high fire point | Sensitive to moisture, higher viscosity |
Types of Transformer Oil
Equipment is typically filled with mineral liquid, which has been the most commonly used insulating liquid due to its stability, thermal performance, and cost-effectiveness. However, recent advancements have led to the development of alternative liquids, such as natural esters, which offer improved environmental benefits and higher fire points, reducing the risk of fire hazards. These alternative liquids also contain small amounts of fatty acids that enhance their oxidation stability and performance under high temperatures.
Electromagnetic Operation and Insulation
The electromagnetic operation of equipment involves the flow of current through windings, which induces magnetic fields and generates heat. Proper cooling and insulation are necessary to maintain the efficiency of this process. The liquid not only aids in cooling but also provides protection to the windings and contacts inside the equipment. Contact configurations within the equipment determine how electrical circuits connect and disconnect, and the insulating properties of the liquid prevent unintended short circuits or failures.
Different Types of Transformer Oils
Different types of equipment liquid are available, including mineral liquid-based and synthetic alternatives. Mineral liquids have been widely used for decades due to their proven reliability, but concerns over their environmental impact have led to the adoption of biodegradable options such as natural esters. These fluids offer a high fire point and enhanced oxidation resistance, making them an attractive choice for applications where fire safety and sustainability are priorities.
Applications of Transformer Oil
The applications of equipment liquid extend beyond just insulation and cooling. It also plays a crucial role in suppressing arcing within the equipment and ensuring the longevity of its components. Over time, however, liquid can degrade due to exposure to high temperatures, moisture, and contaminants. This degradation can compromise its insulating and cooling abilities, making regular oil testing essential. By conducting routine liquid testing, engineers can assess the condition of the liquid, identify contamination, and determine whether it needs to be replaced or treated.
Principles of Liquid Operation
The operation principles of the equipment liquid are closely tied to the efficiency of the equipment itself. When the equipment is energized, the liquid absorbs and transfers heat, maintaining a stable operating temperature. Any significant degradation in the liquid’s properties can lead to insulation failure and reduced performance. Ensuring that the liquid maintains its high dielectric strength is crucial for the equipment’s long-term reliability.
Fire Safety and Flash Point Considerations
Another key property of equipment liquid is its flash point, which determines the temperature at which the liquid can vaporize and ignite. A higher flash point indicates better fire resistance, reducing the risk of fires in electrical substations and industrial settings. Regular monitoring of the liquid’s flash point, along with other properties, is a necessary step in maintaining equipment safety.
Frequently Asked Questions
What is a Dielectric liquid, and why is it used in electrical transformers?
Dielectric liquid is a specially refined mineral liquid used in electrical equipment as an insulating and cooling medium. It helps to insulate the equipment’s internal components, preventing electrical breakdown. Additionally, it dissipates heat generated during operation to keep the equipment at an optimal temperature, ensuring efficiency and preventing damage from overheating.
What are the different types of oil used in transformers?
The two main types of oil used in equipment are mineral oil and synthetic oil.
- Mineral oil is derived from petroleum and is the most commonly used liquid in equipment due to its excellent insulating properties, cost-effectiveness, and availability. It is further divided into highly refined mineral liquid and less refined options.
- Synthetic oils are man-made liquids designed to perform better at extreme temperatures and provide enhanced thermal stability. They are typically used in situations requiring higher performance or in environments with strict environmental and safety regulations.
How does equipment liquid prevent electrical breakdown?
Equipment liquid prevents electrical breakdown by providing high dielectric strength, which allows the equipment to handle high voltage without risk of failure. The liquid acts as an insulating barrier between electrical components, such as conductors and windings, reducing the chance of short circuits. Its insulating properties ensure that electrical discharges or arcing do not occur, thereby maintaining the equipment's stability.
What is the role of transformer oil in cooling and heat dissipation?
The primary role of equipment liquid in cooling is to absorb the heat generated by the electrical components inside the equipment during operation. The oil circulates through the equipment, transferring heat away from the core and winding. It then releases the heat through the outer surfaces or the radiator system, maintaining an optimal operating temperature to avoid overheating, which could damage internal components and shorten the equipment’s lifespan.
How can transformer oil be tested for quality?
Transformer liquid can be tested for quality using several methods, including:
-
Dielectric strength testing to check for the liquid's insulating properties.
-
Acidity tests to detect the presence of contaminants that could cause corrosion or degradation.
-
Moisture content analysis to ensure the liquid remains free of water, which can reduce insulation effectiveness.
-
Color and appearance tests to identify contaminants, oxidation, or breakdown.
Transformer liquid should be replaced when it shows signs of contamination, degradation, or when its dielectric strength drops below the acceptable level. Regular monitoring and testing can help determine when liquid replacement or filtration is necessary to ensure the continued safe and efficient operation of the equipment.
Oil for transformers is an essential insulating and cooling medium used in electrical equipment to ensure optimal performance and longevity. Mineral liquid, the most commonly used type, helps dissipate the heat generated during operation, preventing overheating that could lead to equipment failure. It also provides electrical insulation, preventing short circuits and electrical faults by maintaining the integrity of the equipment's internal components. Additionally, liquid serves as a barrier against moisture and contaminants, further enhancing the reliability and safety of the equipment. Over time, liquid may degrade, requiring periodic monitoring and replacement to maintain its effectiveness.
On-Site Training
Interested in cost effective, professional on-site electrical training?
We can present an Electrical Training Course to your electrical engineering and maintenance staff, on your premises, tailored to your specific equipment and requirements. Click on the link below to request a Free quotation.
EF PARTNER MEDIA
Product Showcases
Shared Media