Transformer Oil Analysis Explained
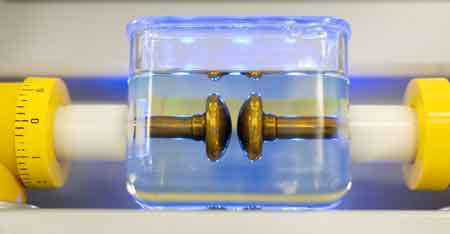
Transformer oil analysis is a critical aspect of preventative maintenance for electrical engineering and maintenance professionals. Ensuring the optimal condition of transformer oil is paramount for the reliable and efficient operation of high-voltage electrical equipment. Degraded oil can significantly impact transformer performance, leading to reduced efficiency, accelerated aging of insulation materials, and ultimately, costly equipment failures. By regularly monitoring the oil's properties through thorough analysis, engineers can proactively identify potential issues, implement timely corrective actions, and extend the lifespan of their transformers, ensuring a stable and uninterrupted power supply.
Electrical Transformer Maintenance Training
Substation Maintenance Training
Request a Free Training Quotation
It plays a vital role in maintaining the health and reliability of electrical equipment. Regular testing ensures that insulating liquids within transformers continue to perform their critical function—providing insulation and cooling while safeguarding the system from potential failures. With the growing complexity of high-voltage networks and the increasing demand for reliable energy distribution, understanding the nuances of transformer oil testing has never been more critical.
A cornerstone of transformer oil analysis is dissolved gas analysis (DGA). This diagnostic technique evaluates the presence of key gases dissolved in the fluid, which can reveal early signs of overheating or electrical faults within the system. Gases like hydrogen, methane, and ethylene, known as key gases, are often generated by the breakdown of insulating oil under stress. By interpreting these gas concentrations, electrical engineers can proactively address issues before they escalate into costly repairs or downtime.
Another critical aspect of oil testing is monitoring its moisture content. Water contamination is one of the leading causes of reduced dielectric strength in insulating liquids. Moisture not only compromises the fluid's insulating properties but also accelerates the degradation of solid insulation within the transformer. Routine testing of samples for water content enables early detection, ensuring that corrective actions, such as fluid purification or replacement, can be implemented promptly to protect high-voltage transformers.
Dielectric breakdown voltage testing
The dielectric breakdown voltage test provides another layer of insight into the condition of the insulating oil. By applying a progressively increasing voltage to the sample, this test determines the point at which electrical breakdown occurs. The results of such routine testing are invaluable for assessing the capacity to withstand the stresses imposed by high-voltage operations. This test, alongside other transformer testing methods, offers a comprehensive view of the equipment's readiness for demanding electrical environments.
Acid Number
Acid number, or neutralization number, testing is a key indicator of health. Over time, insulating liquids can degrade, forming acidic compounds that corrode internal components and reduce insulation performance. Elevated acid levels also contribute to the formation of sludge, which can obstruct heat dissipation and accelerate transformer aging. Monitoring the acid number through transformer testing and analysis allows operators to track the fluid's degradation and plan maintenance schedules effectively.'
Interfacial tension (IFT)
Interfacial tension (IFT) testing, although less frequently discussed, is equally critical in evaluating quality. IFT measures the ability of insulating fluid to separate from water. As fluid ages and becomes contaminated with byproducts of degradation, its interfacial tension decreases, indicating a loss in purity and efficiency. Ensuring high IFT values is essential for maintaining the insulating liquid's protective qualities and overall system performance.
In addition to these standard tests, advanced diagnostic techniques such as furan testing provide further insight into transformer health. By detecting furans, which are chemical markers of cellulose insulation breakdown, this test offers a direct measure of the aging and condition of solid insulation. Combined with power factor testing, which assesses the dielectric losses in insulating materials, these methods deliver a holistic approach to maintaining electrical equipment.
Transformer oil analysis also focuses on physical properties like flash point, which indicates the fluid's flammability and safety under operational conditions. A higher flash point denotes better thermal stability, ensuring the insulating liquid remains effective even in demanding environments. These parameters collectively highlight the importance of transformer oil testing and its role in safeguarding electrical systems.
Routine analysis not only identifies existing problems but also prevents potential failures, enabling a longer lifespan for critical assets. Electrical utilities and industries rely on these insights to maintain uninterrupted power supply and reduce operational costs. By focusing on key themes such as dissolved gas analysis, moisture content, and acid number, transformer oil analysis remains indispensable in modern power system management.
Frequently Asked Questions
What tests are done on transformer?
Transformer fluid undergoes a variety of tests to ensure its quality and performance. Common tests include dissolved gas analysis (DGA) to detect gases produced by internal faults, dielectric breakdown voltage testing to measure the fluid’s insulating properties, and moisture content testing to evaluate water contamination. Additional tests include acid number measurement to assess degradation, interfacial tension testing to determine purity, and furan testing to evaluate the condition of cellulose insulation. These tests collectively provide a comprehensive understanding of the health and the transformer’s overall condition.
How do you do oil analysis?
Oil analysis begins with proper sampling, which involves extracting a representative sample from the transformer under controlled conditions to avoid contamination. The sample is then subjected to laboratory tests, including physical, chemical, and electrical evaluations. For example, dissolved gas analysis identifies key gases indicative of faults, while dielectric breakdown voltage tests measure the a are compared to standard benchmarks to identify any potential issues.
How much does transformer oil sampling cost?
The cost of transformer oil sampling can vary based on the number of tests performed, the complexity of the analysis, and the service provider. Basic testing packages typically range from $200 to $500 per sample, covering essential evaluations like dissolved gas analysis, moisture content, and dielectric breakdown voltage testing. More advanced analyses, such as furan testing or complete diagnostics, can increase the cost, potentially reaching $1,000 or more. Regular testing, despite the expense, is a cost-effective strategy for preventing transformer failures and reducing maintenance costs in the long run.
How can the health of transformer oil be checked?
The health of transformer oil can be checked through routine testing and analysis. Regularly monitoring key parameters such as moisture content, dielectric strength, acid number, and interfacial tension helps assess the oil's condition. Advanced diagnostic techniques, like dissolved gas analysis and furan testing, can identify internal faults or insulation degradation at an early stage. These tests, combined with visual inspections for color and clarity, provide a complete picture of the health. Ensuring timely testing and addressing identified issues can extend the service life and improve transformer reliability.
On-Site Training
Interested in cost effective, professional on-site electrical training?
We can present an Electrical Training Course to your electrical engineering and maintenance staff, on your premises, tailored to your specific equipment and requirements. Click on the link below to request a Free quotation.
EF PARTNER MEDIA
Product Showcases
Shared Media