Fall Protection: The ABCs of Connecting Devices
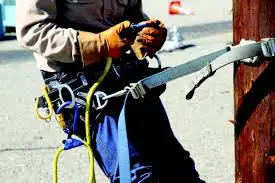
A personal fall protection arrest system (PFAS) is comprised of three vital components: an anchorage, body wear (full-body harnesses), and a connecting device (a shock-absorbing lanyard or self-retracting lifeline). The safety of at-height workers depends on these three components, and each one must be in place and used properly to provide maximum worker protection.
When discussing fall protection, anchorage connectors and full body harnesses receive a lot of attention. We don’t always stop to think about connecting devices like self-retracting lifelines or shock-absorbing lanyards, and yet these are the two components that bear the greatest forces during a fall.
Before we discuss the importance of the connecting device, let’s review the definition of each PFAS component, as defined by OSHA and ANSI.
According to OSHA, a personal fall arrest system is required if any risk exists that a worker may fall from an elevated position. Fall protection itself is required anytime a worker reaches a height of four or more feet for general industry and six or more feet for construction. To determine your working height, measure the distance from the walking/working surface to a lower level or the ground below. As we discussed above, OSHA mandates the use of a full-body harness with a shock-absorbing lanyard or retractable lifeline as part of the complete PFAS. A full-body harness, for instance, distributes the forces throughout the body, and a shock-absorbing lanyard decreases the total fall arresting forces. Let’s look at each of these components, briefly, before diving deeper into the importance and specifications of connecting devices such as shock-absorbing lanyards and self-retracting lifelines.
ANCHORAGE/ANCHORAGE CONNECTORS:
An anchorage is commonly referred to as a tie-off point, such as an I-beam, rebar, scaffolding, or rigid track system. An anchorage is—quite literally—a secure point of attachment for your lifeline/ lanyard that is independent from the worker’s means of support/suspension. An anchorage connector, on the other hand, is the component used to join the connecting device (shock absorbing lanyard or self-retracting lifeline) to the anchorage. Anchorages must be placed high enough for a worker to avoid contact with a lower level should a fall occur, and they should be able to support 5,000 pounds of force per worker or maintain a safety factor of at least two, under the supervision of a qualified person. Anchorage connectors must be positioned so that workers won’t endure a swing fall in the event of a fall from height.
FALL PROTECTION BODY WEAR:
Body wear is the personal fall protection equipment worn by a worker at height. A full-body harness is the only acceptable form of body wear for fall arrest applications. That’s because a full body harness distributes fall arrest forces across the shoulders, thighs, and pelvis. They also have a center back fall arrest attachment to connect to the fall arrest connecting device and may even include additional D-Rings for use in worker positioning, fall prevention, or suspension.
Full-body harnesses must meet the requirements of ANSI/ASSE Z359.1 for fall arrest applications. This means that any work positioning or travel restraint attachments (D-Rings) must withstand a dynamic strength test of a 3.3-foot free fall using a 220-pound test weight. Additionally, the dorsal (back) D-Ring must be suitable for rescue applications unless otherwise prohibited by the manufacturer. Other rescue attachments must meet the 3,600-pound static load test criteria, along with the dynamic test criteria of a two-foot free-fall distance (also) using a 220-pound test weight.
CONNECTING DEVICES:
Connecting fall protection devices are a crucial component of a complete PFAS. The connecting subsystem is the critical link that joins the full-body harness (body wear) to the anchorage/anchorage connector. Connecting devices can consist of energy-absorbing lanyards, self-retracting lifelines, rope grabs, or retrieval systems. How the connection is made depends on whether the worker is equipped for personal fall arrest or work positioning. For the sake of this discussion, we are only focusing on personal fall arrest components.
The connecting means for a PFAS is usually either an energy absorbing lanyard or self-retracting lifeline. A lanyard is literally defined as a flexible line securing a full-body harness to an anchorage point. Energy absorbing lanyards reduce the energy transmitted to the user’s body in the event of a fall. Shock absorbing lanyards also provide deceleration distance during a fall. This reduces the fall-arresting forces on the worker by approximately 60-80 percent below the threshold of injury, as specified by OSHA and ANSI. OSHA mandates that all lanyards include double-action, self-closing, self-locking snap hooks to reduce the possibility of roll-out. Shock absorber packs can also be built into non-shock-absorbing lanyards to provide shock-absorbing capabilities. The inner core of a shock-absorbing pack expands smoothly to reduce fall arrest forces during a fall.
Self-retracting lifelines (SRL’s) are another viable option for connecting devices, depending on your application and fall protection needs. Self-retracting lifelines reduce the free-fall distance and energy loads from a fall. SRL’s also enable greater horizontal and vertical mobility than standard six-foot shock absorbing lanyards. There are great benefits to using SRL’s, including shorter activation and arresting distances, which reduce the risk of worker’s impacting the ground or lower level below. While standard shock absorbing lanyards allow for up to six feet of free-fall distance before activating, self-retracting lifelines require less than two feet to arrest free falls.
According to OSHA 1926.502(d), horizontal lifelines must be designed with a minimum breaking strength of 5,000 pounds. Similarly, self-retracting lifelines and lanyards that do not limit the free fall distance to two feet or less must be capable of sustaining a minimum tensile load of 5,000 pounds when fully extended. However, self-retracting lifelines that automatically limit the free-fall distance to two feet or less must only be capable of sustaining a minimum tensile load of 3,000 pounds when fully extended.
Connecting fall protection devices offer many options, and they should be considered based on the application at hand and working environment. It’s always smart to use a lanyard or lifeline attached to an anchorage point that is positioned directly overhead to protect workers from swing fall. Although all three components of a PFAS are subjected to the total fall force, connecting devices are comprised of only one strength member (webbing, rope, steel cable, etc.). It’s essential to choose a connecting device that is high quality and to check it daily for excessive exposure to UV light, chemicals, physical damage, and/or improper storage. Inadequate inspection can easily lead to device failure.
Consider the following when selecting the right type of fall protection connecting device for your specific personal fall arrest needs:
- Application and Environmental Conditions—this includes the presence of moisture, dirt, grease, oil, acids, hazards and obstructions, and ambient temperature.
- Potential Fall Distance—your potential fall distance is usually greater than anticipated. It’s important to consider the length of your connecting device, along with the length of elongation during deceleration, worker height, and an added safety factor.
- System Component Compatibility—It’s crucial to design test your PFAS as a complete system because components from multiple manufacturers may not be compatible with one another. Incompatible or non-interchangeable components can easily cause roll-out.
- Product Quality and Regulations—Don’t skimp on your PFAS components. The better the quality, the safer the worker will be. Furthermore, although OSHA fall protection regulations are enforced by a federal agency, ANSI standards are suggestive and self-enforced. Even so, ANSI standards should not be taken for granted. Use ANSI standards alongside OSHA regulations as part of a stated performance indicator. ANSI standards are written to save lives and prevent worker injury and should not be taken lightly.
On-Site Training
Interested in cost effective, professional on-site electrical training?
We can present an Electrical Training Course to your electrical engineering and maintenance staff, on your premises, tailored to your specific equipment and requirements. Click on the link below to request a Free quotation.
EF PARTNER MEDIA
Videos
Product Showcases
Shared Media