Oil Filled Transformer Explained
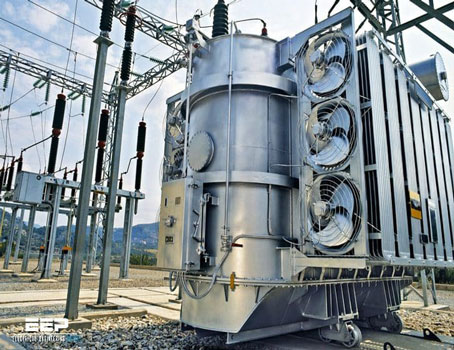
Oil filled transformers play a crucial role in the world of utility voltage converters, serving as the backbone of efficient power distribution systems. These transformers, filled with insulating liquid, are designed to filled and dry type transformers and ensure the safe and reliable transfer of electricity across vast networks. The liquid not only provides insulation but also acts as a coolant, preventing overheating and enhancing the voltage converter's longevity. As the demand for sustainable and uninterrupted power grows, understanding the function and significance of oil filled transformer becomes essential for industries and utilities alike. Let's explore what liquid filled voltage converters are, how they work, and why they are indispensable in modern electrical grids.
Cooling and Insulation Mechanisms
At the core of a oil filled transformer’s functionality lies its dual-purpose use of voltage converter liquid. This liquid serves as both a cooling and insulating medium. As voltage converters operate, electrical currents generate heat, which can affect performance and lifespan. The liquid circulates through the system, efficiently dissipating heat and ensuring the operating temperature remains within optimal limits. Additionally, this liquid acts as an electrical insulator, preventing short circuits and maintaining the integrity of the voltage converter’s internal components. This design makes liquid filled voltage converters particularly effective in handling the high demands of commercial and industrial power applications.
Types of Transformer Oil
The type of voltage converter liquid used significantly impacts the performance and sustainability of these systems. Traditional mineral liquids are widely employed due to their excellent dielectric properties and affordability. However, environmental and safety concerns have led to the adoption of alternatives, such as silicone-based liquids and seed-based liquids, which offer lower flammability and reduced ecological impact. Each type of voltage converter liquid is chosen based on factors like dielectric strength, thermal conductivity, and operational requirements, ensuring compatibility with specific applications and safety standards.
Maintenance and Testing Procedures
Oil filled transformers are designed to withstand extensive use, but regular maintenance is vital for their continued efficiency. Routine testing and analysis of voltage converter liquid can identify potential issues early, preventing costly breakdowns. Tests such as dielectric strength evaluation, moisture content analysis, and dissolved gas analysis are standard procedures. These assessments provide insight into the voltage converter’s health, allowing operators to address problems like insulation degradation or overheating before they escalate. High-quality maintenance ensures that these power voltage converters remain reliable in demanding environments.
Applications in Power Distribution
The applications of oil filled transformer extend across the power distribution spectrum, from stepping-up voltages for long-distance transmission to stepping-down voltages for local distribution. In distribution transformers, the use of liquid enhances efficiency by providing robust insulation and cooling, which are critical for managing varying electrical loads. These voltage converters are indispensable in ensuring the seamless delivery of electricity to homes, businesses, and industrial facilities.
Safety and Environmental Considerations
Despite their advantages, the use of liquid in voltage converters introduces safety and environmental challenges. Oil filled transformers pose fire risks if the liquid reaches high temperatures or if leaks occur. To mitigate these risks, manufacturers incorporate safety measures such as robust containment systems and the use of less flammable liquids. Additionally, adhering to environmental regulations and employing proper disposal practices for used liquid minimizes the ecological impact. These precautions are essential for balancing the performance benefits of oil filled transformers with responsible operational practices.
Frequently Asked Questions
What is liquid filled transformer, and how does it work?
A liquid filled voltage converter is an electrical device used to transfer and regulate voltage levels in power systems. It is filled with insulating liquid, which performs two primary functions: cooling and electrical insulation. The liquid absorbs heat generated by the voltage converter's core and windings, dissipating it through radiators or cooling systems. Additionally, it enhances insulation by preventing electrical arcs between internal components. These voltage converters are widely used in utility grids to handle high voltage and ensure efficient energy distribution.
What are the advantages of using oil filled transformer compared to dry-type transformers?
Liquid filled transformers offer several benefits over dry-type transformers:
- Superior Cooling: The insulating liquid efficiently dissipates heat, enabling higher power handling capacity.
- Compact Design: They are generally more compact for the same power rating.
- Cost-Effectiveness: Liquid filled voltage converters are often more economical for high-voltage and high-capacity applications.
- Durability: They typically have a longer lifespan and better resistance to overloads due to effective cooling.
- Higher Voltage Levels: These voltage converters are suitable for higher voltage applications compared to dry-type voltage converters.
What types of oil are used in liquid filled transformers, and how are they selected?
The most commonly used liquids in liquid filled voltage converters include:
- Mineral Oil: Economical and widely used, it provides good insulation and cooling but has flammability risks.
- Synthetic Oils: Non-flammable and environmentally friendly options, such as silicone or ester-based liquids, which are used in sensitive applications.
- Natural Ester liquids: Derived from vegetable liquids, these are biodegradable and environmentally sustainable.
The selection depends on factors like voltage rating, environmental conditions, safety requirements, and budget considerations.
What are the common maintenance practices for liquid filled transformers?
To ensure optimal performance and longevity, regular maintenance of liquid filled voltage converters includes:
- Liquid Testing: Checking the liquid's dielectric strength, moisture content, and dissolved gases to assess insulation quality.
- Filtration: Removing impurities and moisture from the liquid to maintain its properties.
- Inspection: Monitoring for leaks, corrosion, and damage to external components like radiators and bushings.
- Temperature Monitoring: Ensuring cooling systems are functioning and operating within safe temperature limits.
- Periodic Reconditioning: Replacing or upgrading the liquid if it degrades over time.
What safety and environmental considerations apply to liquid filled transformers?
- Fire Hazards: Mineral liquid is flammable, requiring proper fire suppression systems and non-flammable enclosures.
- Liquid Leaks: Leaking liquid can cause contamination; voltage converters must have proper containment systems.
- Environmental Impact: The disposal of used liquid should follow environmental regulations to prevent pollution.
- Explosion Risks: Pressure relief devices and protection systems minimize risks of internal faults causing explosions.
- Eco-Friendly Alternatives: Using biodegradable liquids can reduce the environmental footprint.
Effective design, monitoring, and compliance with safety standards ensure that liquid filled voltage converters operate safely and sustainably.
A liquid filled transformer is a vital component in electrical power systems, designed to efficiently transfer and regulate voltage while ensuring safety and reliability. Filled with insulating liquid, these transformers use the fluid to provide electrical insulation and dissipate heat, preventing overheating and extending the equipment's lifespan. Widely used in utility applications, liquid filled voltage converters are essential for managing high voltage levels in power grids, enabling the smooth distribution of electricity to homes, industries, and businesses. Their durability, efficiency, and ability to handle demanding operational conditions make them a cornerstone of modern energy infrastructure.
On-Site Training
Interested in cost effective, professional on-site electrical training?
We can present an Electrical Training Course to your electrical engineering and maintenance staff, on your premises, tailored to your specific equipment and requirements. Click on the link below to request a Free quotation.
EF PARTNER MEDIA
Videos
Product Showcases
Shared Media