Oil in Transformers - An Insulating Medium
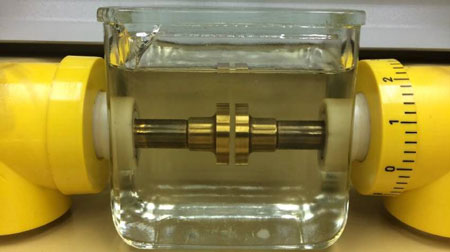
Oil in transformers plays a critical role as a cooling and insulating medium which directly impacts the efficiency, performance, and lifespan, which are essential components of the power grid. Understanding its properties, maintenance requirements, and failure indicators can help professionals prevent costly outages and enhance grid reliability. Let's explore the key functions of dielectric fluid, common issues such as contamination and aging, and best practices for testing and maintenance, equipping readers with the knowledge to optimize device performance and safety.
Electrical Transformer Maintenance Training
Substation Maintenance Training
Request a Free Training Quotation
The Dual Function of Transformer Oil
The primary function of transformer-based oils is to provide both insulation and cooling. As the device operates, heat is generated from the core and coils due to electrical losses. Device liquid, typically filled with mineral oil or similar insulating fluid, absorbs this heat and dissipates it efficiently, thus preventing overheating. Moreover, it serves as an insulating material, maintaining the dielectric strength required for safe operation. The high dielectric strength of the liquid prevents electrical arcing or short circuits between components within the device, ensuring that the unit functions reliably. This dual-purpose function of the oil contributes significantly to the device’s ability to operate for extended periods without failure, reducing the risks of overheating and electrical faults.
Electrical insulating materials play a crucial role in maintaining the efficiency and safety of transformers by managing heat from the core and coils. Among the most commonly used materials, paper insulation provides effective thermal and electrical resistance, ensuring stable performance under operational stresses. Solid insulation, such as epoxy or resin-based materials, complements paper insulation by adding structural integrity and resistance to mechanical and thermal degradation. Together, these insulating systems work to optimize heat dissipation and prevent electrical faults, safeguarding equipment longevity and reliability.
Types of Transformer Oils
However, not all device oils are created equal. There are two main types of fluids used in devices: uninhibited oil and inhibited oil. Uninhibited liquid lacks additives that can slow down its natural degradation, making it more prone to breakdown over time. On the other hand, the inhibited liquid is enhanced with oxidation inhibitors that increase its resistance to degradation. This makes the inhibited liquid ideal for modern devices, where long-term stability and performance are crucial. As devices continue to serve in industrial and power distribution systems, the type of fluid used in each unit plays a direct role in its efficiency, lifespan, and overall environmental impact.
The Importance of Regular Testing and Quality Assessment
When it comes to device liquid, regular testing is essential to ensure that it maintains its properties over time. One of the most critical tests conducted is the dielectric breakdown voltage test, which measures thermal conductivity and the liquid's ability to withstand electrical stress without breaking down. This test ensures that the liquid can continue to insulate effectively under high-voltage conditions. Another important analysis is the Dissolved Gas Analysis (DGA), which detects gases dissolved in the liquid. The presence of certain gases can indicate internal faults, such as overheating or arcing, which could lead to a device failure. By performing regular tests, maintenance teams can identify potential issues early and take corrective action before they escalate into significant problems.
Environmental Considerations and the Shift Toward Sustainable Oils
Environmental considerations also come into play when selecting liquid for the device. Traditional mineral oils, while effective, pose certain environmental risks, such as fire risk and potential toxicity in the event of spills. As a result, alternative, environmentally friendly options, such as natural esters, are gaining popularity. These bio-based liquids and dry type transformers are derived from renewable sources and offer better biodegradability, making them a more sustainable option compared to conventional mineral oils. Additionally, their higher flash point reduces the fire risk associated with device operation, further contributing to the safety of electrical installations. However, while natural esters present a promising alternative, their adoption is still growing, and they are not yet as widespread as mineral oils.
Maintenance and Purification of Transformer Oil
As with any fluid used in electrical equipment, device liquid requires periodic maintenance and purification. Over time, device liquid can deteriorate due to oxidation, external contamination, or electrical stress breakdown. To ensure that the liquid retains its properties, purification techniques such as filtration or vacuum treatment are employed. These methods remove contaminants and restore the liquid’s insulating properties, helping to extend the life of the device. By maintaining the quality of the insulating liquid, power companies can avoid costly repairs and ensure that their devices continue to function efficiently for years.
Frequently Asked Questions
Which oil is used in the transformer?
The liquid used in devices is typically a type of mineral oil, which is specifically refined and treated to meet the insulating and cooling requirements of devices. However, natural esters, which are derived from renewable plant sources, are increasingly used as an environmentally friendly alternative. These liquids are selected for their high dielectric strength (the ability to resist electrical breakdown) and their ability to dissipate heat efficiently from the device's internal components.
What is the oil inside a transformer?
Oil filled transformers are dielectric fluid, meaning it does not conduct electricity and serves primarily to insulate the electrical components from each other. This liquid helps prevent electrical arcing and short circuits. In addition to its insulating properties, the insulating oil also acts as a cooling agent, absorbing and dissipating heat generated by the electrical currents passing through the device's core and coils. The liquid helps maintain the device at a safe operating temperature, preventing overheating and damage to the internal components.
How to maintain transformer oil?
To maintain liquid, regular testing is essential to monitor its dielectric strength, moisture content, and dissolved gases, which can indicate internal issues. Filtration and vacuum treatment help purify the liquid by removing contaminants like sludge, moisture, and gases. Monitoring liquid levels is crucial to ensure proper insulation and cooling while addressing leaks or evaporation. Over time, liquid may need to be replaced or upgraded, especially if it has degraded or become contaminated. By following a routine maintenance schedule, including inspections and necessary treatments, device liquid can be kept in optimal condition, ensuring the device operates safely and efficiently.
What happens if there is no oil in a transformer?
If a device runs without liquid or if the liquid level becomes too low, several critical problems can occur. The device would lack the necessary insulation and cooling properties provided by the liquid. Without adequate insulation, electrical arcing could occur, leading to short circuits or even fires. Additionally, the device would overheat because there would be no liquid to absorb and dissipate the heat generated by the electrical currents. Overheating can damage the device’s internal components, reduce its efficiency, and ultimately lead to the complete failure of the device. Therefore, maintaining an adequate liquid level is essential for a device's safe and efficient operation.
Oil in devices plays a critical role in both insulation and cooling, ensuring the efficient operation and longevity of the device. It acts as an insulating fluid, preventing electrical faults by maintaining a high dielectric strength, and absorbs heat generated during operation, preventing overheating. Equipment liquid can be mineral liquid or natural esters, with the latter being an environmentally friendly alternative. Regular maintenance, including testing for dielectric strength, moisture, and dissolved gases, along with purification methods like filtration and vacuum treatment, is necessary to keep the liquid effective. Proper oil management helps extend device lifespan, reduce risks of failure, and ensure safe, reliable operation in electrical systems.
On-Site Training
Interested in cost effective, professional on-site electrical training?
We can present an Electrical Training Course to your electrical engineering and maintenance staff, on your premises, tailored to your specific equipment and requirements. Click on the link below to request a Free quotation.
EF PARTNER MEDIA
Product Showcases
Shared Media