Transformer Coil Explained
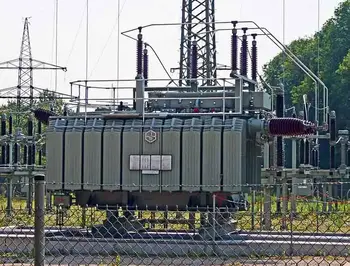
A transformer coil is a fundamental component in electrical devices that facilitate the transfer of electrical energy through electromagnetic induction. Understanding the construction and function of this coil is essential for optimizing the performance of voltage transformers and power transformers in various applications. A transformer coil is simply a series of loops or turns of insulated wire wound around a magnetic core. The core, typically made of laminated iron or steel, provides a path for the magnetic flux generated by the coil. There are two distinct coils: the primary coil and the secondary coil.
Electrical Transformer Maintenance Training
Substation Maintenance Training
Request a Free Training Quotation
What is a Transformer Coil?
It consists of windings of wire wrapped around a magnetic core. These coils are integral to operation, enabling the transfer of electrical energy between circuits by increasing or decreasing voltage levels through electromagnetic induction. When an input voltage is applied, the coils generate magnetic fields, inducing a corresponding output voltage in another coil.
What is the Difference Between a Primary and Secondary Transformer Coil?
The primary coil is the input coil, connected to the power source. When an alternating current (AC) flows through it, it creates a fluctuating magnetic field around the core. This changing magnetic field induces a voltage in the secondary coil connected to the output load. The secondary coil's voltage can be higher or lower than the primary coil's voltage, depending on the desired outcome: increasing (step-up) or decreasing (step-down) the voltage level.
The primary coil is the winding connected to the input voltage source. It receives electrical energy and creates a magnetic field in the magnetic core. The secondary coil, on the other hand, is connected to the output voltage side. It receives the induced voltage from the magnetic flux generated by the primary coil. The number of turns in each coil and their arrangement determine the voltage transformation ratio between the primary and secondary coils.
How Does the Number of Turns in Each Transformer Coil Affect the Voltage Transformation?
The number of turns in the primary and secondary coils directly affects the voltage transformation ratio. According to the principle of electromagnetic induction, the voltage induced in the secondary coil is proportional to the ratio of the number of turns in the secondary coil to the number of turns in the primary coil. For instance, if the secondary coil has twice as many turns as the primary coil, the output voltage will be twice the input voltage. Conversely, the output voltage will be lower if the secondary coil has fewer turns. This ratio is crucial to achieve the desired voltage levels.
What are the Different Types of Winding Arrangements in a Transformer Coil?
It can be arranged in various ways to optimize performance and efficiency. Common configurations include:
- Concentric Windings: Cylindrical coils are wound one over the other, with the low voltage winding typically placed closer to the core.
- Interleaved Windings: Sections of the primary and secondary windings are interleaved to reduce leakage flux and improve coupling.
- Bi-filar Windings: Two wires are wound simultaneously like a single wire, reducing proximity effect losses at high frequencies.
They can be arranged in various winding configurations to suit different applications:
- Layer Winding: Coils are wound in multiple layers, providing compactness and reducing leakage flux. This arrangement is common in high voltage devices.
- Helical Winding: Coils are wound in a helical fashion, allowing for better cooling and higher current capacity. This is often used in large power devices.
- Disc Winding: Coils are wound in disc-shaped sections, improving mechanical strength and voltage distribution. This type is subjected to high mechanical stresses.
- Sandwich Winding: Primary and secondary coils are interleaved, enhancing magnetic coupling and reducing leakage inductance. This configuration is typical in small and medium-sized devices.
What Types of Wire are Used in a Transformer Coil?
Copper is the most common material used due to its excellent electrical conductivity and thermal stability. However, aluminum can be used in larger power transformers to reduce cost. To prevent short circuits, the wires are insulated with materials like enamel, paper, or specialized insulating varnish. The type and thickness of insulation depend on the voltage level and operating temperature.
How is a Transformer Coil Insulated to Prevent Short Circuits?
Insulation is crucial to prevent electrical short circuits and ensure safe operation. Several types of insulation materials are used:
Enamel Coating: The wire is coated with an enamel layer, providing basic insulation and protection against moisture and chemical damage.
Paper Insulation: Paper is used between winding layers, offering excellent dielectric properties and thermal stability.
Polyester Film: Thin polyester films are wrapped around the coils, providing high dielectric strength and resistance to mechanical stress.
Impregnated Insulation: Coils are impregnated with insulating varnish or resin, enhancing thermal conductivity and mechanical integrity.
Ideal vs. Real
In an ideal transformer, all the magnetic flux generated by the primary coil would link with the secondary coil, and there would be no energy losses. However, real transformers experience losses due to factors like resistance in the windings, core losses (hysteresis and eddy currents), and leakage flux. These losses are minimized through careful design and the use of high-quality materials.
They are the heart of these remarkable electrical devices, enabling the efficient and safe transformation of voltage levels. Understanding their construction, function, and various design considerations is crucial for appreciating the intricate engineering that goes into creating these essential components of modern power systems.
They are vital components in electrical devices, enabling efficient energy transfer through electromagnetic induction. By understanding the differences between primary and secondary coils, the impact of winding turns on voltage transformation, and the various winding configurations, one can optimize design for specific applications. The use of high-quality wire and effective insulation techniques ensures the reliability and safety in handling high voltage and power demands.
On-Site Training
Interested in cost effective, professional on-site electrical training?
We can present an Electrical Training Course to your electrical engineering and maintenance staff, on your premises, tailored to your specific equipment and requirements. Click on the link below to request a Free quotation.
EF PARTNER MEDIA
Videos
Product Showcases
Shared Media