Transformer Components Explained
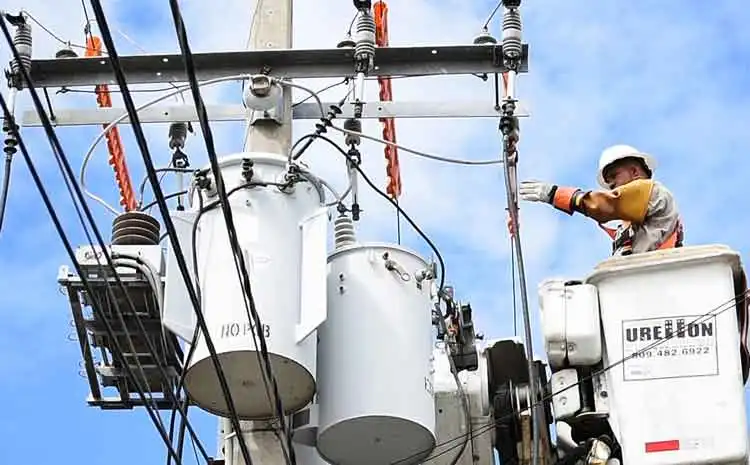
What are the Main Transformer Components?
The primary transformer components include the core, windings, insulating oil, tap changer, cooling system, and safety devices. Each component plays a specific role in the transformer's operation and overall efficiency.
At its core, a transformer comprises two fundamental components:
- Primary Winding: This coil of wire, connected to the input voltage source, generates a magnetic field when an electric current flows through it.
- Secondary Winding: The secondary winding is linked to the output load. It receives the magnetic flux generated by the primary winding and induces a voltage in itself, thus transferring electrical energy to the output circuit.
These windings, often made of copper or aluminum, are carefully wound around a magnetic core, typically constructed from laminated silicon steel to minimize energy losses.
What are the Essential Components of a Transformer?
Core: The core is the basic part of a transformer, providing a path for magnetic flux. It is typically made of laminated silicon steel to reduce energy losses.
- Primary and Secondary Windings: These windings consist of copper or aluminum coils. The primary winding receives the input voltage, and the secondary winding delivers the output voltage. These windings are crucial for the process of electromagnetic induction.
- Insulating Oil: Also known as mineral oil, this oil surrounds the windings and core, providing insulation and cooling by absorbing heat generated during operation.
- Tap Changer: A load tap changer adjusts the transformer's voltage ratio to regulate the output voltage under varying load conditions.
- Cooling System: This system includes cooling tubes and fans that dissipate heat from the insulating oil, maintaining an optimal operating temperature.
- Conservator Tank: This tank accommodates the expansion and contraction of insulating oil, maintaining the oil level and preventing air and moisture from entering the transformer.
What is the Role of the Tap Changer in a Transformer?
The tap changer is a critical component that allows for adjusting the transformer's voltage ratio. By changing the number of turns in the primary or secondary winding, the tap changer regulates the output voltage to match the load requirements. This adjustment is crucial for maintaining voltage stability and ensuring efficient operation of electrical power systems. Load tap changers (LTC) are crucial components that enable a transformer to adjust its output voltage. By varying the number of turns in the windings, the LTC can compensate for fluctuations in the input voltage or load demand, ensuring that the output voltage remains stable.
How Does the Cooling System of a Transformer Work?
Transformers generate heat during operation due to various losses. To prevent overheating and ensure optimal performance, they are equipped with cooling systems. Smaller transformers may rely on natural air cooling, while larger units often employ forced air or liquid cooling mechanisms. In liquid-filled transformers, insulating oil serves as both a coolant and an insulator. The cooling system in a transformer ensures that the insulating oil and other components do not overheat. The system typically includes cooling tubes through which the oil circulates, dissipating heat to the surrounding air. Fans and radiators may also be used to enhance cooling efficiency. Air passes through the silica gel in the breather to remove moisture, protecting the transformer from moisture-related damage. This system maintains a stable operating temperature, ensuring the longevity and reliability of the transformer.
What Safety Devices are Used in Transformers?
Transformers are equipped with various safety devices to prevent damage and ensure safe operation. These devices include:
- Pressure Relief Device (PRD): This device releases excessive pressure buildup inside the transformer tank, preventing potential explosions.
- Buchholz Relay: This relay detects gas accumulation or sudden pressure changes inside the transformer, which could indicate internal faults. It triggers an alarm or trips the transformer to prevent further damage.
- Oil Temperature Gauge and Winding Temperature Gauge: These gauges monitor the temperature of the insulating oil and windings, respectively, alerting operators to potential overheating issues.
What is the Function of a Conservator Tank in a Transformer?
The conservator tank plays a vital role in maintaining the insulating oil level in a transformer. It accommodates the expansion and contraction of the oil due to temperature changes, ensuring a constant oil level. The tank also prevents moisture and air from entering the transformer by using a breather filled with silica gel. As air passes through the silica gel, moisture is absorbed by the silica crystals, protecting the transformer from moisture-related issues.
Liquid-filled transformers often have a conservator tank, an auxiliary tank connected to the main tank. It acts as a reservoir for the insulating oil, accommodating changes in oil volume due to temperature variations. This helps maintain the optimal oil level in the main tank, preventing air ingress and ensuring proper insulation and cooling. A breather, an airtight metallic cylindrical drum containing silica gel, is connected to the conservator tank. As air passes through the silica gel, moisture is absorbed by the silica crystals, protecting the transformer from moisture-related issues.
Transformers are complex electrical devices composed of several essential components that work together to transfer electrical energy efficiently and safely. The core, windings, insulating oil, tap changer, cooling system, and safety devices all play critical roles in the transformer's operation. Understanding these components and their functions helps ensure the reliable performance of transformers in electrical power systems.
On-Site Training
Interested in cost effective, professional on-site electrical training?
We can present an Electrical Training Course to your electrical engineering and maintenance staff, on your premises, tailored to your specific equipment and requirements. Click on the link below to request a Free quotation.
EF PARTNER MEDIA
Videos
Product Showcases
Shared Media