Transformer Oil Filling
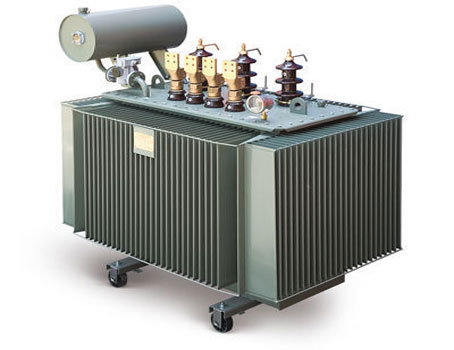
Transformer oil filling ensures proper insulation and cooling in power transformers. It involves degassing, dehydration, and vacuum filling of dielectric fluid to maintain system reliability, prevent overheating, and support high-voltage performance.
What is Transformer Oil Filling?
Transformer oil filling is the process of introducing insulating oil into a transformer to provide cooling, insulation, and moisture protection.
✅ Ensures dielectric strength and thermal conductivity
✅ Performed under vacuum to avoid moisture and air pockets
✅ Critical for commissioning and transformer maintenance
Transformer oil filling is a critical process in the operation and maintenance of transformers within transmission and distribution (T&D) electrical networks. This specialized insulating oil serves as both a coolant and a dielectric medium, essential for dissipating heat and preventing electrical breakdowns. Proper oil filling ensures optimal transformer performance, enhances insulation properties, and extends the equipment's lifespan. In T&D networks, where reliability and efficiency are paramount, transformer oil filling plays a crucial role in maintaining system stability, preventing failures, and ensuring uninterrupted power delivery across the grid. For a deeper understanding of the fluid’s role in performance, see our guide on transformer oil and its critical functions.
Electrical Transformer Maintenance Training
Substation Maintenance Training
Request a Free Training Quotation
Essential for Optimal Transformer Performance
Transformer oil filling is a crucial component of the maintenance and operation of electrical devices, ensuring their smooth operation and extended longevity. The process of filling a device with liquid serves several critical purposes, including insulation, heat dissipation, and voltage regulation. It is vital to maintain the dielectric strength of the device to prevent breakdowns and ensure the reliable operation of electrical equipment. The liquid acts as a solid insulation medium, allowing for the proper functioning of both the device and the connected electrical circuits. This article examines the importance of device liquid filling, delving into the essential processes, safety measures, and environmental considerations associated with this crucial aspect of device maintenance. Proper oil filling is essential to the integrity and operation of any electrical power transformer used in substations or T&D systems.
Oil Preparation and Treatment for Proper Filling
Before the oil is introduced into the device, it undergoes thorough preparation and treatment to remove impurities such as moisture and gas. This step is crucial to maintain the dielectric strength of the liquid, which is essential for preventing electrical faults. The liquid used in devices must possess high insulation properties, and any contaminants can significantly reduce its effectiveness. Filtration and dehydration processes ensure that the liquid meets the necessary quality standards before it is filled into the device. Additionally, the liquid may undergo degassing to eliminate air pockets, which can also compromise the device's insulation and performance. Properly treated liquid ensures that the device operates efficiently and safely, protecting the delicate components from voltage surges and electrical breakdowns. Before filling, it's important to understand the construction of transformers, as design impacts oil volume and insulation paths.
Transformer Oil Filling Overview
Category | Details |
---|---|
Purpose | Provides insulation, cooling, and moisture protection for transformer components |
Common Oils Used | Mineral oil (standard), synthetic oil (high performance), and biodegradable oils (eco-sensitive applications) |
Preparation Methods | Filtration, dehydration, and degassing to remove moisture, gas, and particulate contaminants |
Filling Techniques | - Conventional filling for low-voltage systems- Vacuum filling for high-voltage systems to eliminate air pockets and moisture intrusion |
Key Safety Measures | Spill prevention, moisture exclusion, personnel PPE, equipment inspection, contamination control |
Monitoring & Testing | Dielectric strength tests, dissolved gas analysis (DGA), liquid sampling, and moisture content checks |
Environmental Practices | Use of biodegradable fluids, recycling or treating used oil, regulatory-compliant disposal |
Application Scope | Power transformers, substation transformers, pad-mounted units, medium-voltage and high-voltage systems |
Filling Methods for Safe and Effective Operation
The oil filling process typically follows one of two methods: conventional liquid filling or vacuum liquid filling. Conventional liquid filling is used in devices with lower voltage ratings, where the risk of contamination or air entry is minimal. However, for high-voltage devices, the vacuum liquid filling method is preferred. This process creates a vacuum within the device to prevent air or moisture from entering the system during the liquid-filling process. The vacuum ensures that the liquid fully penetrates the insulation and fills all parts of the device, preventing the formation of air bubbles or voids that can impair the effectiveness of the solid insulation. The careful selection of the liquid filling method ensures that the device functions properly without the risk of electrical failure due to improper liquid saturation or contamination. The oil-filling process plays a key role in substation transformer installation and maintenance, ensuring thermal and dielectric stability.
Safety Measures in Transformer Oil Filling
Given the critical nature of the oil-filling process, safety is of utmost importance. The filling process must be carried out with precision to avoid spillage or contamination, as these could lead to hazardous conditions. Workers handling device liquid are required to follow strict safety protocols to ensure that no impurities or moisture affect the quality of the liquid. Special care is taken to prevent the introduction of foreign materials into the system, which could lead to reduced dielectric strength and ultimately result in device failure. Additionally, all equipment involved in the filling process must be thoroughly inspected and maintained to prevent leaks or malfunctions that could compromise the integrity of the liquid. Ensuring a contamination-free and well-maintained liquid-filling process is essential for safeguarding both the equipment and personnel involved. Ongoing oil quality monitoring is often part of broader transformer health check strategies used to prevent failures and extend equipment life.
Monitoring Oil Quality for Long-Term Efficiency
Once the liquid is filled, continuous monitoring is essential to ensure that it retains its dielectric strength and insulating properties throughout the device’s operational life. Regular inspections and quality control measures, including dielectric tests and liquid sampling, help detect any issues with the liquid's performance, such as the presence of moisture or particulate matter. This ongoing monitoring ensures that the device operates at optimal efficiency, preventing issues that could arise from liquid degradation. Furthermore, maintaining the liquid’s integrity helps protect the solid insulation of the device, ensuring its longevity and reducing the likelihood of costly repairs or replacements.
Environmental Considerations and Transformer Oil Management
The use and disposal of transformer liquid must be handled with care due to environmental concerns. Some device liquids can be harmful to the environment if spilled or improperly disposed of. As a result, there is a growing trend toward the use of biodegradable liquids, which are designed to break down more easily in the event of a spill, reducing their environmental impact. Moreover, proper disposal methods, such as recycling used liquid or treating it for reuse, have become standard practices in the industry. Ensuring that the device liquid is handled and disposed of responsibly is not only a legal requirement but also an essential step in minimizing the ecological footprint of electrical operations. For pad-mounted installations, 3-phase pad mounted transformers require careful oil filling under vacuum to eliminate moisture and trapped air.
Frequently Asked Questions
How is transformer oil filling performed?
Filling oil in a current transformer (CT) is typically done during installation or maintenance. First, the device tank should be thoroughly cleaned and inspected for any contamination or damage. Then, the device is carefully filled with liquid using a pumping system or a filling machine, ensuring that the liquid level completely covers the windings and core. It is crucial to avoid introducing air or moisture into the device during the process, as these can negatively affect its performance. Once filled, the liquid level is checked, and any air bubbles or trapped gas are removed to ensure the system is sealed correctly.
Why are transformers oil-filled?
Transformer oil filling primarily involves two functions: insulation and cooling. The liquid acts as an insulator, preventing electrical arcing and breakdowns between the high-voltage windings and the device tank. Additionally, the liquid absorbs the heat generated by the electrical currents flowing through the device, helping to dissipate it and maintain an optimal operating temperature. This liquid-based system enhances the device's efficiency, safety, and lifespan.
What kind of oil do you put in a transformer?
The most common liquid used in devices is mineral oil, derived from refined petroleum. This liquid has good dielectric properties and thermal conductivity. In some cases, synthetic or vegetable-based liquids are used as alternatives, especially in environmentally sensitive applications or for higher-performance devices. These liquids are chosen for their ability to insulate, cool, and resist degradation over time.
How much oil is filled in a transformer?
The amount of liquid required for transformer oil filling a device depends on its size, design, and voltage rating. Typically, the liquid volume can range from a few litres in small devices to several thousand litres in large power devices. The specific volume is determined by the device’s rated capacity, the dimensions of the core and windings, and the cooling requirements. Each device is designed with a precise liquid filling capacity to ensure optimal performance and safety.
Transformer oil filling is a crucial process in the manufacturing and maintenance of electrical devices. The liquid, typically mineral liquid or synthetic alternatives, serves as an insulating and cooling medium within the device, helping to prevent electrical faults and dissipate heat generated during operation. During the filling process, the device tank is carefully filled with liquid to ensure complete coverage of the device's windings and core, without introducing air or moisture, which could compromise the device's performance and longevity. Proper device oil filling is essential for maintaining the efficiency and reliability of power distribution systems, as well as preventing overheating and electrical breakdowns.
Related Articles
On-Site Training
Interested in cost effective, professional on-site electrical training?
We can present an Electrical Training Course to your electrical engineering and maintenance staff, on your premises, tailored to your specific equipment and requirements. Click on the link below to request a Free quotation.
EF PARTNER MEDIA
Videos
Product Showcases
Shared Media