Frequency Converter
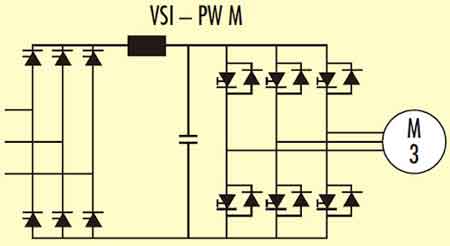
A frequency converter is an essential device for the modern industrial electrician to understand. This device, also known as a variable frequency drive (VFD) or AC drive, controls the speed of an AC motor by adjusting the frequency and voltage of the power supply. Here is a review of the key concepts, such as motor control, inverter technology, and the importance of Hz (Hertz) in understanding its operation. From reading this article, an industrial electrician will gain a deeper understanding of how a frequency converter works, its applications in industrial automation, and the significant energy savings it offers. Also, this article explores specific applications of frequency converters, including their use in pumps, fans, and HVAC systems, equipping the electrician with the knowledge to effectively utilize this technology in various industrial settings.
Modern industrial processes rely heavily on precise motor control, and frequency conversion plays a crucial role in achieving this. A solid-state frequency converter, a key component in many industrial systems, provides a reliable and efficient means of altering the frequency of the power source. This allows for precise control of motor speed, leading to optimized performance and significant energy savings across a wide range of applications.
Variable Frequency Drive (VFD)
Before the advent of modern VFDs, controlling the speed of AC motors was a complex task. Early methods involved using AC generators with variable rotational speeds or multi-pole motors with switches to alter the number of active stator poles. These methods were often inefficient and limited in their control capabilities. The development of solid-state electronics paved the way for the modern VFD, which provides precise and efficient motor control.
A Variable Frequency Drive (VFD), often simply called an AC drive, is a type of electronic controller that drives an electric motor by varying the frequency and voltage of its power supply. The VFD adjusts the motor speed to match the required load, providing precise control and optimizing performance. This technology has become essential in various industrial and commercial applications, offering significant benefits in energy efficiency, process control, and equipment lifespan.
Motor Control
The primary application of a VFD is motor control. By adjusting the frequency of the AC power supplied to the motor, a VFD can precisely control its speed. This is crucial in applications where variable speed is required, such as conveyor belts, pumps, and fans. Precise motor control allows for optimized process operation, reduced mechanical stress on equipment, and improved overall efficiency.
Inverter
At the heart of a frequency converter lies an inverter. This crucial component converts the incoming AC power to DC power and then inverts it back to AC power at a different frequency. This process allows the converter to adjust the output frequency and voltage, providing the variable speed control necessary for various applications. Modern inverters utilize solid-state technology, primarily Insulated Gate Bipolar Transistors (IGBTs), for efficient and reliable power conversion. IGBTs are high-speed switching transistors that can rapidly turn on and off, enabling precise control of the output waveform.
The inverter section utilizes a technique called Pulse Width Modulation (PWM) to generate the desired AC waveform. PWM involves creating a series of pulses with varying widths to emulate the shape of a sine wave. By adjusting the width of these pulses, the inverter can control both the voltage and frequency of the output power. This precise control allows for smooth motor operation and minimizes harmonic distortion.
Hz (Hertz)
Hertz (Hz) is the unit of measurement for frequency, representing the number of cycles per second of an AC waveform. Understanding Hertz is fundamental to grasping how frequency converters function. For instance, a motor designed to operate at 60 Hz will rotate at a specific speed. It can alter this frequency—for example, to 50 Hz or even 400 Hz—to change the motor's speed.
It's important to note that the effective voltage of an AC power supply can vary with frequency. For example, a 460V 60 Hz system has a lower effective voltage than a 380V 50 Hz system, even though their peak voltages are similar. Converters must account for this difference to ensure proper motor operation and prevent damage.
Three-Phase
Three-phase power is a common type of AC power supply that utilizes three conductors carrying alternating currents with a phase difference of 120 degrees. Many industrial applications are designed for three-phase power due to its efficiency and ability to deliver more power compared to single-phase systems. Three-phase converters are essential for controlling large motors and heavy-duty equipment.
While many industrial applications utilize three-phase power, converters are also available for single-phase systems. Single-phase converters are typically used for smaller motors and residential applications. However, three-phase motors are generally preferred for variable speed operation due to their wider power range and ability to start rotating without external assistance.
Speed Control
The ability to precisely control the speed of a motor is a key function of a frequency converter. By adjusting the output frequency, the converter can regulate the motor's speed to match the specific needs of the application. This precise speed control not only optimizes performance but also reduces energy consumption and extends the lifespan of the motor and related equipment.
Industrial Automation
Frequency converters play a vital role in industrial automation. They are used extensively in manufacturing processes, material handling systems, and various automated equipment. The ability to precisely control motor speed and integrate with programmable logic controllers (PLCs) makes them essential for achieving efficient and flexible automation solutions.
Energy Saving
One of the most significant benefits of using a VFD is energy saving. In many applications, motors operate at full speed even when a lower speed would suffice. By adjusting the motor speed to match the actual load, a VFD can significantly reduce energy consumption. This is particularly beneficial for applications with variable load requirements, such as pumps and fans, where energy savings can be substantial.
Applications
Frequency converters find applications in a wide range of industries and equipment. Some common applications include pumps, fans, conveyors, compressors, HVAC systems, and machine tools. In pumps and fans, VFDs optimize flow rates and reduce energy consumption. In conveyors, they provide precise speed control for material handling. In HVAC systems, they regulate air flow and temperature for optimal comfort and efficiency.
Questions and Answers
What is a frequency converter, and what is it used for?
Also known as a variable frequency drive (VFD) or AC drive, it is an electronic device that controls the speed of an AC motor by adjusting the frequency and voltage of the power supplied to the motor. It is used in a wide range of applications, including industrial automation, HVAC systems, and pumps, to optimize performance, save energy, and improve process control.
How does a frequency converter work?
It typically consists of a rectifier, an inverter, and a control circuit. The rectifier converts the incoming AC power to DC power. The inverter then converts the DC power back to AC power at a different frequency, which is used to control the speed of the motor. The control circuit manages the operation of the converter, allowing for precise speed regulation and various other functions.
What are the benefits of using a frequency converter?
Using one offers several benefits, including:
- Energy savings: By adjusting the motor speed to match the load, VFDs can significantly reduce energy consumption.
- Improved process control: Precise speed control allows for optimization of processes and improved product quality.
- Reduced mechanical stress: Smooth acceleration and deceleration reduce wear and tear on the motor and related equipment.
- Extended equipment lifespan: By reducing stress and optimizing operation, VFDs can extend the life of motors and other components.
- Reduced noise: VFDs can help reduce the noise produced by motors, especially at lower speeds.
What are the main types and how do they differ?
The main types include:
- Voltage-source inverters (VSIs): These are the most common type and use a constant voltage DC bus.
- Current-source inverters (CSIs): These use a constant current DC bus and are typically used for larger motors and specialized applications.
- Cycloconverters: These directly convert AC power from one frequency to another without an intermediate DC stage. They are typically used for very high power applications.
How do you select the right one for an application?
Selecting the right frequency converter involves considering several factors, including:
- Motor type and size: The VFD must be compatible with the motor's voltage, current, and power requirements.
- Application requirements: The VFD should be able to provide the necessary speed range, control accuracy, and dynamic response.
- Environmental conditions: The VFD should be rated for the operating environment, including temperature, humidity, and altitude.
- Features and functionality: Consider additional features like communication protocols, built-in protection, and programming options.
- It is recommended to consult with a qualified engineer or supplier to ensure the selection of the most suitable one for your specific application.
Frequency converters, also known as variable frequency drives (VFDs) or AC drives, are essential devices for modern industrial electricians. They provide precise motor control by adjusting the frequency and voltage of the power supply, leading to optimized performance and significant energy savings. This article explored the key concepts behind frequency converters, their role in industrial automation, and various applications including pumps, fans, and HVAC systems. By understanding the principles and applications of frequency conversion, electricians can effectively utilize this technology to enhance efficiency and productivity in industrial settings.
On-Site Training
Interested in cost effective, professional on-site electrical training?
We can present an Electrical Training Course to your electrical engineering and maintenance staff, on your premises, tailored to your specific equipment and requirements. Click on the link below to request a Free quotation.
EF PARTNER MEDIA
Product Showcases
Shared Media