Electrical Insulation Resistance Test Explained
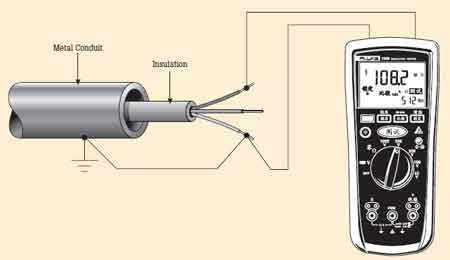
An electrical insulation resistance test measures the effectiveness of electrical insulation in resisting current flow. It helps detect degradation, moisture, or contamination in wiring, motors, and cables to prevent faults, ensure safety, and maintain equipment performance in industrial and commercial systems.
What is an Electrical Insulation Resistance Test?
An electrical insulation resistance test is ing the safety and ity of power systems.
✅ Measures the resistance of insulation to detect deterioration or moisture
✅ Ensures the safety and reliability of power systems and equipment
✅ Helps prevent faults in motors, cables, transformers, and wiring
Visit Our Electrical Troubleshooting Training Course
This test helps identify weaknesses in the insulation that can lead to equipment failure or dangerous faults. With around 80% of maintenance and testing involving evaluating the integrity of insulation, this analysis plays a critical role in maintaining system reliability. In this article, we will explore the importance of insulation resistance testing, how it is performed, and the factors that can affect the results. For a deeper understanding of the tools involved in this process, see our electrical test equipment guide, which covers essential instruments for accurate insulation resistance testing.
How to Interpret Results
Interpreting insulation resistance test results requires understanding what the measured resistance values reveal about the condition of the insulation. Typically measured in megohms (MΩ), these values indicate how well the insulation resists electrical current under applied test voltages. A higher resistance reading suggests good insulation health, while lower values may signal deterioration, contamination, or moisture ingress.
When using a megohmmeter, compare the results against the equipment manufacturer's specifications or industry standards like IEEE 43, which recommends a minimum resistance value of 1 megohm per kilovolt (1 MΩ/kV) plus 1 MΩ for rotating machines. For example, a 4,160V motor should generally show at least 5.16 MΩ. Resistance values well below this threshold may indicate dielectric breakdown or aging insulation.
It’s also important to observe resistance trends over time as part of a predictive maintenance program. A gradual decline in IR values could mean that the insulation is absorbing moisture or contaminants, while sudden drops may point to mechanical damage or insulation failure. Temperature corrections are essential when comparing results, as resistance tends to decrease with rising temperatures.
Consistently low readings across all test voltages could indicate uniform degradation, while varying results at different voltages may suggest surface leakage currents or partial discharges. In such cases, further diagnostic testing like polarization index (PI) or dielectric absorption ratio (DAR) may be required to assess insulation condition more accurately.
Proper interpretation of insulation resistance results helps ensure safe operation, reduce the risk of unplanned outages, and extend the life of electrical equipment.
Common Causes of Low Insulation Resistance Readings
When insulation resistance readings fall below acceptable thresholds, it's critical to identify the underlying cause before resuming equipment operation. While a low megohm reading might suggest insulation failure, several other factors can also contribute.
One of the most frequent issues is moisture contamination. Water trapped inside insulation due to environmental exposure, poor sealing, or condensation can drastically reduce resistance values. Similarly, surface leakage currents caused by dust, oil, or conductive particles on the surface of insulators can give the false impression of degraded insulation.
Insulation aging is another major factor. Over time, thermal stress, electrical loading, and vibration can lead to insulation degradation, such as cracked jackets, hardened insulation, or reduced dielectric strength. In older equipment, these effects can cause gradual declines in resistance, which should be tracked and compared against historical maintenance records.
Ambient humidity and temperature during the test can also affect readings. High humidity tends to reduce resistance, especially on surfaces, while elevated temperatures can lower bulk insulation resistance. For accurate comparisons, apply temperature correction factors to normalize the results.
In some cases, improperly performed tests—such as using incorrect test voltages, poor grounding, or failing to isolate the system—can produce inaccurate results. Always follow manufacturer's instructions and test using calibrated megohmmeters to ensure reliability.
Understanding the cause of low readings allows for more accurate diagnosis, proper repairs, and targeted preventive maintenance—helping to avoid equipment damage, safety risks, and costly downtime.
Typical Minimum Insulation Resistance Values
Equipment Type | Test Voltage | Minimum IR Value | Notes |
---|---|---|---|
Low-Voltage Motors | 500–1000 V DC | 1 MΩ or higher | Based on general guideline: 1 MΩ per kV + 1 MΩ |
Medium-Voltage Motors | 1000–5000 V DC | 5 MΩ to 100 MΩ | Use IEEE 43 standard for rotating machines |
Power Cables (LV) | 500–1000 V DC | >100 MΩ | Values depend on cable type and length |
Power Cables (MV/HV) | 1000–5000 V DC | >500 MΩ | Higher resistance indicates dry, clean insulation |
Dry-Type Transformers | 1000–5000 V DC | >1000 MΩ | Test phase-to-ground and phase-to-phase |
Oil-Filled Transformers | 500–2500 V DC | >2000 MΩ | Check for oil contamination or moisture ingress |
Control Wiring Circuits | 250–500 V DC | >10 MΩ | Lower voltages but still require good insulation |
Switchgear Bus Insulation | 1000–5000 V DC | >1000 MΩ | Varies with voltage class and age of equipment |
Frequently Asked Questions
Why is it important?
An insulation resistance (IR) test measures the ability of insulation to resist current flow under high test voltages. It is important because it identifies potential faults in the insulation, such as moisture ingress, contamination, or degradation, which can lead to short circuits, equipment damage, or safety hazards. Regular preventative maintenance, including IR testing, helps ensure that systems remain safe and operational, reducing downtime and costly repairs.
How is an electrical insulation resistance test performed?
An IR test is typically conducted using insulation resistance testers, which apply high test voltages to the equipment's insulation. The process involves disconnecting the equipment from the power supply and applying the voltage across the insulation to measure its resistance to current flow. This analysis provides valuable resistance measurements that indicate the health of the insulation. The analysis is usually conducted at several voltage levels to assess performance under different conditions, and the results are compared to industry standards to determine if the insulation is performing correctly. If you're testing electric motors, visit our page on electric motor testing to explore diagnostic techniques that help detect insulation breakdown.
What are acceptable electrical insulation resistance test values?
Acceptable resistance measurements can vary based on the type of power system being tested. In general, higher resistance values indicate better insulation health, while lower values suggest potential problems. For example, large industrial motors may require minimum values of 1 megohm per kilovolt, while other systems might have different thresholds. Additionally, factors such as the type of equipment, system voltage, and environmental conditions can influence the acceptable value. It's important to follow industry guidelines when interpreting results. The accuracy of an insulation resistance test depends on using the right device—learn more in our insulation resistance tester article.
What factors can affect the results of an electrical insulation resistance test?
Several factors can impact the accuracy and reliability of insulation resistance testing. Temperature, humidity, and contamination can all lower resistance values, giving the appearance of insulation degradation when the issue may be environmental. Additionally, the age of the equipment and the condition of the dielectric can influence the results. Equipment that has been exposed to harsh conditions or has not been properly maintained may show lower resistance values due to dielectric absorption, where the insulation retains moisture or contaminants. It's important to account for these factors when evaluating analysis data. To implement a consistent maintenance schedule that includes insulation testing, read our preventive maintenance training overview.
How often should an electrical insulation resistance test be conducted?
The frequency of IR testing depends on the specific system and the operating environment. In general, critical systems should undergo IR testing as part of regular preventative maintenance, at least annually, though some equipment may require more frequent testing. For high-voltage equipment or equipment operating in harsh conditions, IR tests may need to be conducted more regularly to ensure safety and reliability. Ongoing monitoring of results helps in tracking any degradation in insulation performance over time, allowing for timely interventions.
An electrical insulation resistance test is a crucial aspect of maintaining the health and safety of power systems. Regular testing with appropriate resistance testers provides valuable insights into the integrity, helping to prevent costly failures and ensuring the safety of personnel. By understanding the factors that influence resistance measurements and following a consistent schedule, facilities can effectively manage the risk of failure and maintain reliable operations.
Related Articles
On-Site Training
Interested in cost effective, professional on-site electrical training?
We can present an Electrical Training Course to your electrical engineering and maintenance staff, on your premises, tailored to your specific equipment and requirements. Click on the link below to request a Free quotation.
EF PARTNER MEDIA
Videos
Product Showcases
Shared Media