Thin-film cells fatten solar market
The latest civic breakthrough was the recent passage of the California Solar Initiative, the largest solar-energy bill in U.S. history. The California Public Utilities Commission's bill establishes an 11-year solar rebate program worth $3.2 billion for new and retrofit installations of solar photovoltaic systems.
On the national level, the House of Representatives recently introduced legislation that would extend solar tax credits, now due to end in 2008, through 2017. Under the plan, residential and commercial installations receive a tax credit of $1,500 per half-kilowatt in power use reduction, among other incentives.
Observers said U.S. interest in solar energy might be catching up with the interest seen in the rest of the world.
"American taxpayers want to invest in technologies that create jobs, reduce emissions, lower our energy bills and keep our energy dollars here in the United States," the Washington-based Solar Energy Industries Association said in a statement praising the bill. That group and other alternative-energy advocates are swarming the halls of Congress to compete for federal largesse, as lawmakers seek to reduce U.S. dependence on foreign oil.
Nonetheless, the 2007 solar-cell market is expected to be virtually a mirror image of last year's: Demand is astronomical, but worldwide growth remains hampered by persistent shortages of the critical polysilicon materials used to make the cells.
One change this year is that thin-film solar cells have arrived and are poised to steal market share from conventional solar-cell products. One thin-film startup, First Solar Inc. (Phoenix), is ramping up at a frenetic pace and claims to have the industry's lowest-cost panels, priced at $2.40/W-up to 45 percent below its rivals.
The Wild West of the booming clean-technology sector boasts no fewer than 40 companies scrambling to develop thin-film cells. Even Sharp Corp., the world's largest solar-cell maker, is entering the fray. Venture capitalists are pouring millions into thin-film solar startups, and a diversity of companies, from Google to Honda, has invested in the sector.
The appeal of thin-film cells is that they require little or no polysilicon, a critical material now in short supply because of spiraling solar-energy demand. Conventional solar cells, which account for 90 percent or more of today's shipments, are manufactured using the polysilicon materials, which constitute 40 to 50 percent of the cost of a conventional photo-voltaic cell. In contrast, thin-film cells use a thin layer of materials formed on a substrate.
For some time, polysilicon shortages have disrupted the supply chain and stunted overall growth rates in the solar-cell market. Piper Jaffray & Co. (Minneapolis) predicts that the sector will see a 22 percent jump in worldwide sales in 2007.
Polysilicon shortages may last until 2008 or longer-a trend that opens the door for thin-film technologies, said Jesse Pichel, an analyst with Piper Jaffray. "We don't expect to see a polysilicon glut for the foreseeable future. However, it's a better situation than in past years, in that we have several new polysilicon plants moving into production," he said.
What this means is that the solar-cell industry is out of balance and under pressure. "The solar-power evolution is in its early stages, and there is no single-point technology," Pichel said. "Polysilicon feedstock prices are rising, and module ASPs are falling 6 percent annually, squeezing margins and limiting capacity."
The solar-energy industry as a whole faces a multitude of challenges. First, the solar-cell market could be overhyped and due for a shakeout.
Many of the companies in the sector are smaller, privately held startups, which face stiff competition from the established, conventional solarcell giants. The latter group includes Evergreen, Kyocera, Mitsubishi, Motech, Sanyo, Sharp, Shell, SunPower and Suntech.
Cost is another issue. Despite breakthroughs, residential solar-energy costs range from 20 to 40 cents/kilowatt-hour on sunny days. That's two to three times more expensive than the current electricity grid, according to market research firm Solarbuzz LLC (San Francisco). (One kilowatt equals the amount of electricity needed to burn a 100-W light bulb for 10 hours, according to the firm.)
The sun is free, but converting its energy into electric power isn't. That requires a new and costly infrastructure from the home to the public utilities.
A household must install a solar-module system on the roof. Power from that system flows to an inverter, which converts and transforms it into usable voltage and alternating current. Some homes could generate sufficient solar power for all their power needs, but many would still need to be connected to the public utility grid because they wouldn't derive sufficient power from the solar installation.
For a typical home, a 3-kW grid-tied solar system costs approximately $17,500 to install after California's rebate (but before any tax incentives), according to Solarbuzz. It takes three to seven years to break even, the firm said.
In general, solar energy is not expected to reach parity or become "grid competitive" without subsidies until 2010, Pichel of Piper Jaffray said.
In many nations, governments must provide subsidies in order to make solar viable for consumers and businesses. For years, Germany and Japan have offered attractive subsidies; not surprisingly, they also lead all other nations in solar adoption. Incentives are also in place in Spain and elsewhere, but the United States lags in such programs.
Some observers believe the tide is turning in solar, thanks to subsidies and technology breakthroughs, including the much-touted thin films. But there are a number of costs and technology trade- offs associated with these new materials.
The polysilicon used in conventional cells is expensive, but the conventional cell structures have proved production-worthy, and they achieve greater power efficiencies than their thin-film counterparts. Thin-film cells have a power efficiency rating of 8 to 14 percent, compared with 14 to 20 percent for conventional products.
Thin-film cells have been in development for decades, but they use exotic materials that are difficult to manufacture with decent volume yields. The most common thin-film materials are amorphous silicon or polycrystalline. They include cadmium telluride and copper indium gallium diselenide, among others.
Only a handful of companies have actually brought the technology into mass production, including First Solar, Mitsubishi and United Solar Ovonic LLC (Auburn Hills, Mich.). Nanosolar Inc., a startup originally funded by Google Inc. in June 2006, announced a $100 million financing package to build the world's largest solar-cell manufacturing facility, in San Jose, Calif. Currently in pilot production in its Palo Alto, Calif., facility, the solar-cell startup is developing a roll-to-roll solar-cell technology.
In December, Honda Motor Co. Ltd. established a subsidiary, Honda Soltec Co. Ltd., that will produce next-generation thin-film solar cells based on a compound of copper, indium, gallium and selenium.
Thin-film products will not displace conventional solar cells at least "in the next decade, but we do expect that they will grow and find markets," said Julie Blunden, vice president of external affairs at SunPower Corp. (San Jose).
"The overall solar-cell market will grow 10 to 20 percent in 2007 and 2008," predicted Subhendu Guha, president and chief operating officer of United Solar Ovonic, a subsidiary of Energy Conversion Devices Inc. "We are growing 50 to 100 percent every year."
United Solar Ovonic claims to be the world's largest manufacturer of triple-junction, amorphous silicon photovoltaic solar panels. "Previously, the question was, 'Can we develop it?' Now, not only can we do it, but we're in production," Guha said.
United plans to nearly triple its output by 2008 and says its panels are cost-competitive. With help from its subsidies in California, the company's solar modules are "getting close to 20 cents per kW-hr," approaching the peak rates of the electricity grid, Guha said.
Another thin-film supplier, First Solar, also is raising eyebrows. "First Solar's modules are the lowest-cost in commercial production today, at about $1.50/W to manufacture-about 45 percent below (the) industry average," according to a recent report from Piper Jaffray. "While emerging lower-cost technologies may exist in the lab, First Solar has a two-year lead in costs and scale."
The company's modules are based on cadmium tellurium technology and require no polysilicon. First Solar reportedly has signed a number of large OEM contracts in Germany, but the company is not expected to turn a profit until 2008.
Not all of the excitement revolves around the startups. In fact, the newcomers are keeping a close eye on the established industry giants, especially Sharp. That company has been expanding its conventional solar-cell capacity, but it is also making a major push into the thin-film arena. Late last year, Sharp rolled out two thin-film solar panels, which are said to achieve a conversion efficiency of 8.5 percent and to deliver 90 W.
The products are based on a tandem cell design, which combines separate amorphous and monocrystalline layers. A key feature is the ability to form the silicon raw materials into a layer only about 2 microns thick on a glass substrate. That thickness - roughly 1/100th that of conventional polysilicon solar cells - reduces overall cost for consumers, Sharp says.
This month, Sharp claimed to have developed a stacked, triple-junction thin-film solar cell for mass production. The triple-junction structure combines two amorphous silicon layers and one microcrystalline silicon layer. The new architecture claims to boost cell conversion efficiency from 11 percent to 13 percent and module conversion efficiency from 8.6 percent to 10 percent. Production of the triple-junction technology is slated to begin at Sharp's Katsuragi plant (Nara Prefecture, Japan) in May.
Despite its developments in thin films, Sharp has not turned its back on conventional solar cells. Last year, the company increased its annual production capacity by 100 MW to meet demand in Japan and abroad. As a result, solar-cell production capacity at the Katsuragi Plant will reach 600 MW per year, the world's highest, according to the firm.
Sharp said it would double its production capacity for solar modules during the coming year at Sharp Manufacturing Co. (Wrexham, North Wales). Capacity will increase from 110 MW to 220 MW annually, which will supply the booming European market.
The U.S. market also is seeing strong growth in both homes and businesses, said Marc Cortez, director of marketing for the Sharp's Solar Energy Solutions Group. "Generally, in the United States, we expect the market to grow," he said. "You will still see growth rates of 20 percent per year."
Related News
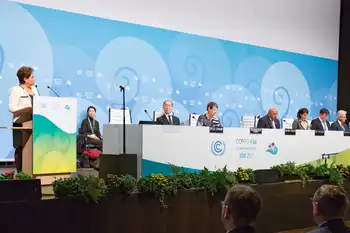
What to know about the big climate change meeting in Katowice, Poland
WARSAW - Delegates from nearly 200 countries have assembled this month in Katowice, Poland — the heart of coal country — to try to move the ball forward on battling climate change.
It’s now the 24th annual meeting, or “COP” — conference of the parties — under the landmark U.N. Framework Convention on Climate Change, which the United States signed under then-President George H.W. Bush in 1992. More significantly, it’s the third such meeting since nations adopted the Paris climate agreement in 2015, widely seen at the time as a landmark moment in which, at last, developed and developing countries would…