Entrepreneur wants to reinvent the utility pole
CALGARY, ALBERTA - Paul Giannelia has made a career of toppling traditions. He was, after all, the agent who ended PEI's isolation from mainland Canada by erecting the $1-billion Confederation Bridge in the 1990s.
Now the veteran project manager has another target in his sights – the ubiquitous wood poles that carry the bulk of North America's electrical power grid. The age of wood is ending, he proclaims, thus escalating the debate polarizing the utility industry: wood versus composite materials.
In one corner is Canada's utility pole leader, Stella-Jones Inc. SJ-T of Montreal, a profitable, established company that supplies 350,000 wooden structures each year to the continent's power distributors.
In the other is Mr. Giannelia's money-losing upstart, Resin Systems Inc. RS-T, with sales of barely $10-million a year. It has developed a modular pole based on composite materials – polymer resins and glass fibre – that it says is cheaper, lighter and more environmentally palatable than wood.
Late last year, Resin Systems made what Mr. Giannelia, its 61-year-old chief executive officer, touts as a breakthrough: Hydro One's selection of his poles for renewing a power line in northwestern Ontario.
With this deal, “we're going to shoot the lights out,” says Mr. Giannelia, whose Calgary-based company makes its poles in an Ontario factory. “One milestone we needed was to land our first major strategic customer – one of the top 15 purchasers of utility poles in North America.”
Hydro One falls in that category, he says, and other utilities will take their cue from the Ontario transmission giant. At stake is a continental market of $8-billion a year. Now, 90 per cent of that market is staked out by wood poles, but if Mr. Giannelia has his way, it will be much less.
Brian McManus, president of Stella-Jones, is unimpressed. “It certainly doesn't keep me up at night,” he says. “When you talk to the utilities, you get quite a different answer. Wood utility poles are a proven item that's been in the utilities' stable for many years.”
Over the decades, he argues, they have beaten off a host of challengers, including concrete and thin-wall steel poles. There is nothing in Resin Systems' claims that hasn't been heard before, he says, and the low cost of the wood always wins the day.
Mr. Giannelia concedes that, on their own, wood poles may be cheaper, particularly at shorter lengths, but the composite kind is much easier to install and costs less in lifetime ownership, he argues. The life of a maintenance-free composite pole, he says, could extend more than 100 years, compared with a 40-year average for wood – although Mr. McManus puts the wood poles' life at 50 to 60 years.
Wood poles come from cutting down forests; composite materials are downstream byproducts of hydrocarbons. But composites have one big plus for utilities: Unlike wood poles, they don't need to be pressure-treated with chemical preservatives, such as creosote, to avoid deterioration.
That issue looms large as utilities cope with the ravages of weather, bugs and fungus, while trying to prevent toxic chemicals from seeping into soil and lakes. The pileated woodpecker is another big hazard for wood, but the pesky bird is no threat to glass fibre and resin.
Mr. McManus says wood poles are getting more environmentally friendly, as they become recyclable and preservatives prove less toxic and more resilient to breaking down in landfill.
“I'm not going to say the preservatives don't have some toxicity level to prevent fungi and insects from attacking them,” he says. “But as long as the poles are properly handled, it's not an issue.”
Those arguments don't sway Mr. Giannelia, who was born in Austria, moved to Canada at age 8, and grew up in a construction family in a suburb of Toronto. He went to university for an economics degree, but couldn't get infrastructure out of his blood. He took engineering by correspondence, although he never acquired an engineering degree – except, more recently, the honorary kind.
In the late 1970s, Mr. Giannelia co-founded an engineering firm that worked on landmark projects such as the Cambie Street Bridge in Vancouver, and light rail transit systems in Calgary, Edmonton and Vancouver.
He then bid on the controversial fixed link to be built between PEI and New Brunswick, and his consortium won the contract. Bringing the public-private project to reality took a decade – seven years of pushing the process and three years of building the bridge. It opened on schedule on May 31, 1997.
Back at his base in Alberta, Mr. Giannelia learned of an Edmonton company, Resin Systems, that had solved technical challenges around impact resistance of composite materials. He became CEO, took a 5-per-cent stake, and developed a modular design based on short tapered lengths of 15 or 30 feet that can be fitted into each other. It means less costly transit and storage, allowing poles to be erected on site in combinations from 30 to 165 feet.
That put him up against Stella-Jones, a titan in pressure-treated poles and rail ties, but a mystery outside its sector. “We get mistaken for anything from a beer company to a lingerie company,” Mr. McManus says. The name, in fact, reflects two major founding shareholders – an Italian firm named Stella and a Scottish company named Jones.
Mr. McManus says there is room for different kinds of materials in the industry, and concedes the lighter modular poles can be useful for putting power lines into hard-to-get-at areas.
Indeed, Hydro One spokeswoman Danielle Gauvin says the utility chose Resin Systems' product to replace poles in rough terrain, where lighter composite modules have an advantage. Ms. Gauvin says the utility is open to using all kinds of poles, depending on conditions.
The Hydro One deal is not, by itself, a game-changer – it is an open contract valued at up to $20-million in three years.
But Mr. Giannelia hails it as a first step to expanding his factory in Tilbury, in southwestern Ontario, which employs 115 people. It's been a rare manufacturing startup in an area suffering from industrial decline.
That factory could grow even larger if his composite formula is applied to other uses, such as bridge construction and materials handling. “Our only limitation is our engineering imagination,” he insists.
Related News
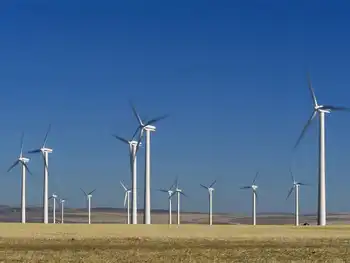
Alberta is a powerhouse for both green energy and fossil fuels
CALGARY - By Chris Varcoe, Calgary Herald
A few things are abundantly clear about the state of renewable energy in Alberta today.
First, the demise of Alberta’s Renewable Electricity Program (REP) under the UCP government isn’t going to see new projects come to a screeching halt.
In fact, new developments are already going ahead.
And industry experts believe private-sector companies that increasingly want to purchase wind or solar power are going to become a driving force behind even more projects in Alberta.
BluEarth Renewables CEO Grant Arnold, who spoke Wednesday at the Canadian Wind Energy Association conference, pointed out the sector is poised to keep…