The quest for the better battery
The goal of Mr. Peters, 51, and his co-workers at International Battery, a high-tech start-up, is industrial revolution. Racing against other companies around the globe, they are on the front lines of an effort to build smaller, lighter, more powerful batteries that could help transform the American energy economy by replacing gasoline in cars and making wind turbines and solar cells easier to integrate into the power grid.
This summer the Obama administration plans to announce how it will distribute some $2 billion in stimulus grants to companies that make such advanced batteries for hybrid or all-electric vehicles and related components. International Battery is vying for a modest chunk of it.
The hope is that the grants will spur far higher levels of experimentation and production, pushing down the costs that have prevented these batteries from entering the mass market.
The batteries would not only replace the fuel tanks in millions of cars and trucks, but would also make wind turbines and solar cells more practical, by absorbing excess energy when their production jumps and giving it back when the wind suddenly dies or the sun goes behind a cloud.
But first, companies like International Battery will have to tweak the chemistry of their devices and improve the manufacturing process, bolstering the batteries’ capabilities. And prices will have to come down — a problem that is far more daunting when it comes to batteries for vehicles and the grid, because the packs are hundreds or thousands of times the size of those for handheld electronics.
Nearly all battery research now focuses on lithium ion batteries, which made their consumer debut in 1991 and have since replaced nickel-cadmium and nickel-metal-hydride technologies in many portable electronics.
Lithium is the third-lightest element on the periodic table, which allows for far greater energy density. A lithium ion battery that will move a car one mile weighs less than half as much as a nickel metal hydride and one-sixth as much as lead acid.
Advanced battery manufacturing is mostly based in Japan, China, Taiwan and South Korea, where laptop computers and similar devices are built.
International Battery bought machines from China that manufacture the components and has been tweaking them to make them run faster, use fewer materials and produce a better product. Each button on the control panels is labeled in Chinese characters, with English penciled in by hand underneath. Near Mr. Peters’ machine, a cardboard box awaiting unpacking bears hand lettering that says, “Glass Please Carefully.”
Other companies are also trying out new chemistries and materials, at the positive and negative terminals of the battery. As technicians try to improve battery assembly, the first requirement is a strikingly clean work environment. Mr. Peters, in goggles and spotless rubber gloves, declined to shake hands recently, just as a surgeon might on the way into the operator room.
The gloves protect him from the chemicals in the battery, which include nickel, cobalt and manganese, and shield the batteryÂ’s delicate tissues from the natural oils on his fingers.
“We don’t want any debris,” said Mr. Peters, who formerly worked at a nearby factory that made bulletproof glass. (International Battery’s pristine new showplace was previously an appliance repair shop.)
The engineers face a difficult challenge. The batteries have to store a lot of energy in a small, light package, scoring high in a quality known as energy density. They also have to absorb energy and give it back quickly, a factor called power density.
Think of a battery as a bottle for energy, and the power density as the size of the bottleÂ’s neck. Good power density means a shape like a peanut butter jar, easy to fill or empty; low power density is more like a wine jug with a narrow neck.
The batteries have to charge quickly and withstand thousands of cycles of charge and discharge. They have to dissipate heat without catching fire, a product problem that a giant like Apple Computer could survive but a start-up electric car company probably could not. The batteries must function in Maine winters and Texas summers.
Engineers have met almost all of these goals, but not simultaneously in one product. And they are still way off on price: the components remain far too costly. But they are trying, devoting more and more resources to meeting that goal.
A few yards away from Mr. Peters, workers were getting ready to tear out the cafeteria so new cubicles could be built for more engineers as International BatteryÂ’s production expands.
“The battery is an enabler” of electric vehicles and other technologies, said Ted J. Miller, a technical specialist at the Ford Motor Company, referring to the models being produced in Allentown and others relying on different chemistry.
Mr. Miller represents Ford at the Advanced Battery Consortium, an organization formed with federal encouragement in 1991 to coordinate research on technology. Ford, Chrysler and General Motors have contributed, often with research scientists and facilities, and the Energy Department has written checks.
Automakers need improvements in batteries “everywhere we can get it,” Mr. Miller said.
In 1991 the Advanced Battery Consortium was founded and set a near-term target for developing a battery that would cost $150 per kilowatt-hour of storage. (A kilowatt-hour sells for about a dime and will move a car three or four miles.)
Eighteen years later, prices are in the range of $750 to $1,000. By comparison, a lead-acid battery in a conventional car costs less than $100 for that much capacity, although it is much too heavy to build an electric car around and not durable enough.
Now the Energy Department has a new goal: $500 by 2012.
“We think we can make that,” said Patrick Davis, the program manager at the Energy Department’s vehicle technologies program.
One reason for the optimism is the infusion of money that Washington is preparing to get the job done. The $2 billion in new grants planned this summer includes $1.2 billion for companies manufacturing battery cells and complete battery packs, $350 million for electric drive component manufacturing and $25 million for battery recycling. The cell and battery-pack companies could get up to $150 million each. Companies have already applied for more than $6 billion in grants.
The Obama administration is also hoping to drum up market demand. In March, President Obama, visiting a testing center for electric vehicles run by Southern California Edison in Pomona, announced tax credits of up to $7,500 for consumers who buy plug-in hybrid vehicles. Such models get some of their energy from the power grid and some from gasoline.
“This investment will not only reduce our dependence on foreign oil, it will put Americans back to work,” Mr. Obama said. “It positions American manufacturers on the cutting edge of innovation and solving our energy challenges.”
Some industry experts say that simply getting electric cars to market will touch off a cycle of new research, investment and product improvement.
“If there is a demand for all-electric vehicles, as opposed to small hybrids, you’re going to have a monumental scale-up of the battery industry,” said Kevin Czinger, chief executive of Coda Automotive, which plans to offer a $45,000 four-door all-electric sedan in California next year.
But when it comes to a genuine mass market for an affordable plug-in hybrid or all-battery car, “we don’t quite know how to get there,” said Mr. Miller, of Ford.
Consumer Reports magazine detailed the price problem in its February issue, reviewing an after-market conversion of a Prius to a plug-in. For $10,875 the magazine had a five-kilowatt-hour battery installed by a Toyota dealership in Massachusetts. It got a 67 miles a gallon, a 35 percent improvement over the stock version.
“Our Prius’s conversion to plug-in power cost more than you could ever expect to recoup in gas savings,” the magazine said. Still, “as a sign of things to come, we found it encouraging.”
Carl A. Picconatto, a battery expert at Mitre, a technology consulting firm, and other scientists suggest that materials reduced to the nano scale are a promising avenue. Nano-materials have huge surface areas in small, light packages; batteries work through chemical reactions that unfold on surface structures.
In batteries, charged particles travel through electrolytes. Crawling through an electrolyte consumes energy that does not get delivered to the consumer. But pushing through a nano-material could be like “pushing your hand through sand, versus pushing your hand through a big pile of rocks,” Dr. Picconatto said.
Still, in some applications, nano-materials gum up the works, or break down after a few dozen charges and discharges, experts say. Solving that problem could allow a cheaper, lighter battery pack.
The plug-in hybrid Chevy Volt, due out in November 2010, will carry 16 kilowatt-hours and go up to 40 miles on a full charge; if estimates from Mr. Miller hold when it goes into mass production, the battery pack alone would run from $9,600 to $16,000. And that does not count related parts like the system that maintains the temperature of the cells within an acceptable range and manages the charging and discharging.
“We believe electrification is the future if the industry,” said Bob Kruse, the company’s executive director for global vehicle engineering, hybrids, electric vehicles and batteries.
“The mastery of battery technology is key,” he said. “We still have a lot of work to do.”
Related News
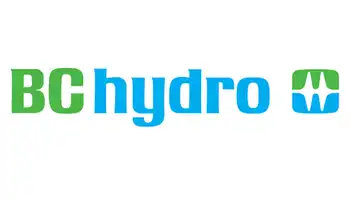
B.C. residents and businesses get break on electricity bills for three months
VICTORIA - B.C. residents who have lost their jobs or had their wages cut will get a three-month break on BC Hydro bills, while small businesses are also eligible to apply for similar relief.
Premier John Horgan said Wednesday the credit for residential customers will be three times a household’s average monthly bill over the past year and does not have to be repaid as part of the government’s support package during the COVID-19 pandemic.
He said small businesses that are closed will not have to pay their power bills for three months and large industrial customers, including those operating mines and…