Turning forest slash into cash
WEST LORNE, ONTARIO - Forest fire season had passed, so the plumes of smoke rising from the dense forest below caught David Ramsay's eye.
It was fall 2004, and Ramsay, Ontario's minister of natural resources, was flying in a small plane over an area of northern Ontario. Curious about the smoke, he asked his pilot to fly in for a closer look.
What he saw was indeed fire, though nothing like the wildfires currently ravaging southern California.
"It was a normal operation in which the forest industry, in cooperation with the ministry, burns the tops of trees," recalls Larry Skinkle, biomass co-ordinator for the forests section of the ministry. "It was roadside slash being disposed of."
Slash is the unwanted branches, stumps, tops and leaves of trees that are removed during logging. The standard industry practice is to burn slash at the side of logging roads. It's estimated that about 15 per cent of wood resulting from logging activities is biomass from forest slash, though in Ontario the issue is still being studied.
Ramsay asked his staff to hunt around for technologies that could put slash to better use. A government team visited Sweden, Finland and Germany and came to realize there was potential to convert biomass into usable energy, and at the same time create new revenue for the struggling forest sector.
Last summer, the ministry decided to invest $771,000 to construct a prototype biorefinery that's capable of converting slash into a carbon-neutral "bio oil."
Bio oil is a "green" fuel that contains no sulphur dioxide and half the nitrogen oxide of conventional oil. But just like conventional fuel oil, bio oil can be used in industrial boilers, diesel generators and in turbines that generate electricity.
"There's a lot of residual biomass out there to sustain us," says Peter Fransham, founder and president of Ottawa-based Advanced Biorefinery Inc., which was hired to build the government prototype based on a "dry distillation" process called pyrolysis.
Pyrolysis, as an approach, is well understood and used. It works by rapidly heating biomass to an extreme temperature — up to 1,000 degrees F — in an oxygen-starved chamber. Under such intense heat, the molecular structure of the biomass shatters, resulting in three usable materials: oil, charcoal and gas.
Essentially, what happens over millions of years with fossil fuels happens in a matter of seconds with pyrolysis.
In a biorefinery, the gases and charcoal can be recycled as fuel for powering the system and for pre-drying the biomass. The oil — representing about 60 per cent of the mix — is separated out and can be shipped off as fuel oil or used as a source of chemicals for making everything from plastics to foods to fertilizer.
The challenge when using forest slash as a raw material, however, is that it's a low-density material typically located in remote areas. Bringing it to a central processing facility isn't economical, as the transportation costs wipe out any profit.
"It doesn't take long before the cost of trucking exceeds the value of the biomass," says Fransham, who decided to take a different approach to the problem. "We take the machine to the biomass."
Advanced Biorefinery has designed a transportable plant with six 20-foot-long modules that are easy to transport and can be assembled on-site within a week. By converting slash into a liquid seven times denser, transportation becomes economical.
"When logging is done in an area and loggers take their equipment to a new site, we go with it," says Fransham, an engineer and scientist who has been developing the technology for 18 years.
"You can view the biomass as an oil well on the surface, but to keep the transportation costs down you have to densify it as you go."
A Dorchester, Ont.-based venture called Agri-Therm Ltd., recently spun out of the University of Western Ontario, is taking a similar approach.
However, its mobile pyrolysis plant is targeted at farmers who want to turn agricultural residue into bio oil.
Queen's University professor David Layzell, research director with the biomass research think-tank BIOCAP Canada, says emerging competition in the field is just what the industry needs to drive innovation and greater interest in bio oil.
"We have to start thinking of bio oil as a major biofuel," says Layzell, pointing out that bio oil's potential as an industrial fuel tends to be overshadowed by sexier renewable transportation fuels such as ethanol and biodiesel.
He says that as the United States moves more aggressively to wean itself from foreign crude oil, there will be a significant role for bio oil and Canadian know-how that has matured after three decades of university research. "Within this whole area of pyrolysis Canada is probably a world leader."
Fransham figures his bio oil became competitive in 1999 when crude oil was an inflation-adjusted $20 (U.S.) per barrel, making it more affordable to produce than its bitumen cousin from the Alberta oil sands.
"That's pretty much our break-even price in today's dollars," he says. "We will have to discount the bio oil because it is not easy to store and burn, but our market studies indicate that people will buy biofuels at a 30 per cent discount to the market."
Shouldn't be a problem. A barrel of crude oil is trading at around $60 these days, but approached $80 back in July.
The high prices led to announcements of record profits last week from some of world's top oil producers, and economists say prices will likely rise back up over the next year.
Fransham envisions a day when thousands of his machines are deployed across the province, churning out enough of the green fuel every day to heat or supply electricity to the equivalent of 2 million homes. The technology would also be suited for heavily forested areas of the United States, China, India and other parts of Canada, where remote communities could harvest slash for local fuel production and local use.
But you don't have to go into the bush to make a business out of bio oil, says Andrew Kingston, president and chief operating officer of Vancouver-based DynaMotive Energy Systems Corp.
DynaMotive prefers to build larger, permanent fast-pyrolysis facilities that are strategically located beside a feedstock (raw material) source. For example, the firm's pilot plant in West Lorne, Ont., is located on the site of Erie Flooring & Wood Products, which each day can produce during normal operations about 100 tonnes of sawdust and wood chips.
The West Lorne facility and Erie Flooring have a symbiotic relationship. Erie supplies the residual biomass that is converted into bio oil, charcoal and gas using DynaMotive's process. The bio oil is then used to fuel a Magellan Aerospace gas turbine, which produces heat and 2.5 megawatts of electricity, some of it used for Erie's wood flooring plant. Any remaining electricity is sold into the provincial grid under contract.
DynaMotive's goal is to travel the world looking for similar, mutually beneficial partnerships — for instance, with a company in Australia that handles municipal green waste or a sugar producer in Brazil with a constant output of sugarcane bagasse (pulpy residue left after extracting sugar). Cleaning up forests in British Columbia that have been devastated by the pine beetle represents another opportunity down the road, if the economics are right.
"We're almost scavengers," says Kingston, pointing out DynaMotive has tested more than 120 raw materials — from coconut shells to tealeaves.
"We look at the leftovers and see what we can process. In some instances it works, and in others it doesn't. It all depends on volume, the logistics of moving the material, processing it, and what you eventually do with the fuel."
A 200-tonne per day pyrolysis plant is currently under construction in Guelph that will convert wood-based construction demolition material into bio oil and use it to generate electricity.
A number of other plants are planned for Ontario, which through the province's new standard-offer program will pay 11 cents per kilowatt-hour for electricity produced from biomass.
As with Advanced Biorefinery, DynaMotive had early financial support through Sustainable Development Technology Canada, as well as the now discontinued Technology Partnerships Canada. That financing was crucial to demonstrating that the technology works and that the bio oil itself could compete with conventional oil.
The road to acceptance has been slow, but momentum is finally building. "The industrial fuels market is quite staggering, but it's also a market that doesn't accept change very readily. There's a lot of skepticism that needs to be broken down," Kingston explains. "It's moving solidly in the right direction now, and interest begets more interest."
It helps that aluminum maker Alcoa Canada, after testing DynaMotive's bio oil in a furnace at a smelting plant in Baie-Comeau, Que., was satisfied enough to enter contract negotiations for more supply. "We're getting a lot of acceptance by very significant industrial users," says Kingston.
Layzell thinks big when he thinks bio oil.
If enough demand builds for the green crude, and enough large biorefineries emerge to produce it, then it's conceivable that a pipeline infrastructure could one day emerge to support it — similar to what we have today for natural gas and conventional oil.
"When we're looking at bioenergy becoming a significant portion of Canada's energy needs, we need to start thinking scale," he says.
But it's still early days, says Fransham.
"We're kind of where the oil industry was back in the early 1900s.... It's only really in the last five years that the stars have aligned, with high energy prices and concern about the environment."
Related News
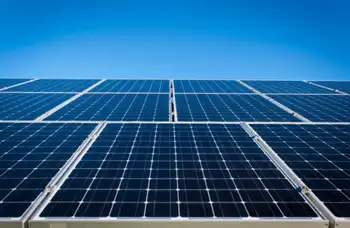
Energy Department Announces 20 New Competitors for the American-Made Solar Prize
WASHINGTON - The U.S. Department of Energy (DOE) announced the 20 competitors who have been invited to advance to the next phase of the American-Made Solar Prize Round 3, a competition designed to incentivize the nation’s entrepreneurs to strengthen American leadership in solar energy innovation and domestic manufacturing.
The American-Made Solar Prize is designed to help more American entrepreneurs thrive in the competitive global energy market. Each round of the prize brings new technologies to pre-commercial readiness in less than a year, ensuring new ideas enter the marketplace. As part of the competition, teams will have access to a network of…