Substation Grounding - Ensuring Electrical Safety
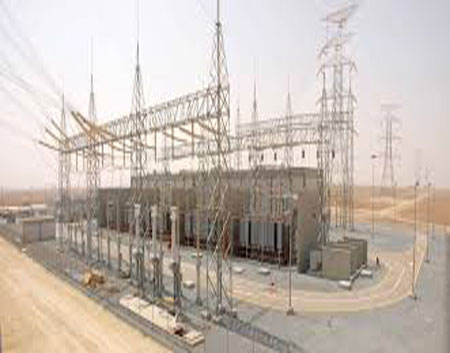
Substation grounding is a critical aspect of electrical engineering that ensures the safety and reliability of power systems. At its core, substation grounding refers to interconnected conductors designed to safely dissipate fault currents and maintain equipment at a common potential. This process is essential to protecting personnel and equipment from electrical hazards, ensuring uninterrupted power supply, and minimizing the risk of damage during electrical faults or lightning strikes. Proper systems in electrical substations enhance operational stability, prevent voltage surges, and ensure compliance with regulatory standards. Understanding the principles and importance of electrical systems is key to designing efficient, safe, and compliant power systems.
Advanced Protective Relays and IEDs
One of the most significant advancements in substation protection is the use of microprocessor-based protective relays and Intelligent Electronic Devices (IEDs). These advanced control systems detect and isolate faults rapidly, preventing damage to critical infrastructure. Unlike traditional electromechanical relays, modern protective relays provide real-time data collection, communication capabilities, and adaptive settings that enhance their performance. By integrating these devices, substations can protect and control power flow more efficiently, reducing downtime and enhancing reliability.
Substation Automation and Virtualization
Substation automation has further transformed how protection systems operate. Automation and virtualization enable centralized control, minimizing the need for extensive hardware and on-site interventions. Virtual protection schemes allow engineers to monitor electrical substations remotely, quickly identifying issues and deploying corrective measures without physically accessing the site. This automation improves the adaptability of power system management, ensuring that substations respond dynamically to changes in load demand and grid conditions.
Essential Protection Equipment
Comprehensive protection equipment is vital for maintaining the integrity of a substation. Circuit breakers play a critical role in interrupting fault currents and preventing cascading failures within the electrical grid. Proper coordination of circuit breakers with other protective devices ensures that faults are isolated at the right locations, minimizing disruptions. Additionally, surge arresters, insulators, transformers, and grounding systems contribute to shielding substations from overvoltages, short circuits, and unexpected electrical anomalies.
Preventing Animal Intrusions
Another challenge in substation protection is mitigating the risks posed by wildlife. Animal intrusion is a frequent cause of electrical faults, leading to power disruptions and costly repairs. Birds, rodents, and climbing animals can inadvertently bridge high voltages, causing short circuits or equipment damage. To counter this, substations implement physical barriers, insulated covers, and laser deterrent systems to keep animals away from sensitive components. These preventive measures significantly reduce outage risks while ensuring the long-term safety of electrical substations.
Protection Against Overvoltages and Lightning Strikes
Substations must also be protected against transient overvoltages caused by lightning strikes and switching operations. Without adequate defences, these sudden voltage spikes can severely damage equipment, leading to costly failures. High-performance surge arresters and robust grounding techniques are essential for dissipating excess energy safely. By directing fault currents into the ground, these protective measures help maintain system stability and prevent disruptions to transmission and distribution networks.
The Future of Substation Protection
Effective substation protection involves a combination of advanced technologies and strategic design. The ability to detect and isolate faults quickly, deploy automation for enhanced monitoring, and implement robust protective equipment ensures the reliability of the power system. Substations must continuously adapt to new challenges, integrating state-of-the-art solutions that enhance their resilience against faults, environmental threats, and operational inefficiencies. As the demand for electrical power grows, so does the need for comprehensive and intelligent protection strategies that safeguard the backbone of modern energy infrastructure.
Frequently Asked Questions
Why is substation grounding important for electrical safety?
A substation system is essential for electrical safety because it provides a safe pathway for fault currents to travel to the earth, thereby preventing dangerous electrical shocks to personnel and damage to equipment. Without a proper system, fault currents can cause dangerous voltages to build up in the equipment and surrounding areas, increasing the risk of electric shock. Systems also help in controlling step and touch voltage hazards, ensuring that electrical equipment remains safe for workers. In the event of an electrical fault, the system helps to quickly and safely direct the current to the ground, reducing the risk of injury and ensuring the safe operation of the electrical system.
What are the key components of a substation grounding system?
The key components of an electrical system include the grounding grid, grounding rods, connections, and conductors. The grid is usually made of metal conductors buried in the soil around the substation. It forms a network that provides a low-resistance path for fault currents to travel. Rods, also known as earth rods, are metal rods driven into the ground to improve the dissipation of fault currents into the earth. These rods are typically placed at strategic locations throughout the substation to ensure that the system is effective in different environmental conditions. Connections link all components of the system, ensuring that they work together to create a continuous conductive path. Conductors carry the fault currents from the equipment to the grid or rods. Together, these components ensure that electrical faults are safely dissipated, and the system operates reliably and safely.
How is ground resistance measured, and why does it matter in substation grounding?
Ground resistance is measured using instruments like a ground resistance tester, which applies a small current to the system and measures the voltage drop across the system. The result is a value of resistance (measured in ohms) that indicates how easily fault currents can flow through the earth. Low ground resistance is essential for a system to effectively dissipate fault currents and prevent dangerous voltage buildup. High ground resistance can lead to insufficient dissipation of electrical energy, increasing the risk of electric shock and equipment damage. It can also cause increased heating in the system, leading to the potential for fires or system failure. Therefore, achieving an optimal level of ground resistance is crucial for the safety and reliability of the substation.
What are the best practices for designing an effective substation grounding system?
Designing an effective electrical system requires careful consideration of several factors, including the layout of the substation, soil resistivity, the type of equipment used, and potential fault currents. The grid should be designed to cover the entire substation area, ensuring that all equipment is well-connected to the system. The rods should be placed at locations that optimize the flow of fault currents into the ground, taking into account factors like soil type and moisture content. The system should be designed to minimize ground resistance by using materials that provide good conductivity and by considering the depth and arrangement of the rods. Regular testing and ongoing maintenance should be part of the design process to ensure the system remains effective over time. Additionally, safety considerations, such as the mitigation of step and touch voltages, should guide the placement of components to protect personnel working in or near the substation.
How do regulations and standards impact substation grounding design and maintenance?
Regulations and standards play a critical role in electrical system design and maintenance by ensuring that systems meet safety and performance criteria. Standards such as IEEE P80 provide detailed guidelines for the installation, design, and maintenance of systems, ensuring that systems are both safe and reliable. Compliance with these standards helps minimize the risk of electrical hazards, such as electric shock or equipment failure and improves the overall reliability of the substation. These standards also ensure that electrical systems are designed to handle fault currents effectively, taking into account local soil resistivity, environmental conditions, and system requirements. Regular updates to regulations help keep systems in line with technological advances and industry best practices. By following these standards, substations can ensure that their systems perform effectively and comply with safety laws, reducing risks and enhancing operational efficiency.
Substation grounding is a critical element of electrical system safety and performance, ensuring that electrical substations are properly protected against electrical faults. It involves creating a safe pathway for fault currents to travel into the earth, preventing hazardous voltages that could lead to electric shocks or equipment damage. Key components of a system include grids, rods, and conductors, which work together to minimize ground resistance and safely dissipate fault currents. Proper design and maintenance are essential to maintaining a reliable system, with factors like soil resistivity, equipment type, and safety considerations playing a key role. Adherence to industry standards, such as IEEE P80, ensures compliance with safety regulations and optimal system performance, ultimately safeguarding both personnel and the substation equipment.
On-Site Training
Interested in cost effective, professional on-site electrical training?
We can present an Electrical Training Course to your electrical engineering and maintenance staff, on your premises, tailored to your specific equipment and requirements. Click on the link below to request a Free quotation.
EF PARTNER MEDIA
Videos
Product Showcases
Shared Media