Hand Safety - Protective Gloves
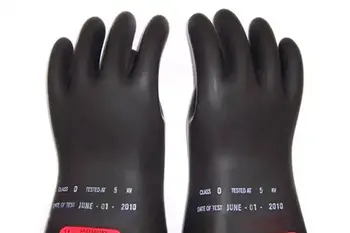
Rubber insulating gloves are among the most important articles of personal protection for electrical workers. To be effective, the gloves must incorporate high dielectric and physical strength, along with flexibility and durability. For superior performance they should meet and/or exceed the requirements of current American Society for Testing and Materials (ASTM) D120 specifications. Gloves should also be electrically tested following ASTM D120/IEC903 specifications.
A glove system usually consists of:
Rubber Insulating Gloves: Classified by the level of voltageand protection they provide.
Liner Gloves: Are used to reduce the discomfort of wearing rubber insulating gloves in all seasons, for year round use.
Liners: provide warmth in cold weather, while they absorb perspiration in the warm months. These can have a straight cuff or knit wrist.
Leather Protector Gloves: Should always be worn over rubber insulating gloves to provide the mechanical protection needed against cuts, abrasions and punctures. Look for those that are steam pressed on curved hand forms to ensure proper fit over rubber gloves.
ELECTRICAL-PROTECTIVE GLOVE CLASSIFICATION
Employees who work in close proximity to live electrical current may require a variety of electrically insulating protective equipment. The Occupational Safety and Health Administration (OSHA) outlines this in their Electrical Protective Equipment Standard (29 CFR 1910.137) which provides the design requirements and in-service care and use requirements for electricalinsulating gloves and sleeves as well as insulating blankets, matting,
covers and line hoses. Electrical-protective gloves are categorized by the level of voltage protection they provide and whether or not they’re resistant to ozone. Voltage protection is broken down into the following classes:
For gloves, ozone resistance is covered by the “Type” designation. A Type I glove is not ozone-resistant, while a Type II is ozone-resistant. Once the gloves have been issued, OSHA requires that “protective equipment shall be maintained in a safe, reliable condition”. This requires that gloves be inspected for any damage before each day’s use. Gloves must also be inspected immediately following any incident that may have caused damage. OSHA requires that insulating gloves be given an air test along with the inspection.
OSHA requires air testing, but doesn’t explain how to perform the test. The test method is described in ASTM F 496, Specification for In-Service Care of Insulating Gloves and Sleeves. Basically, the glove is filled with air, either manually or by an inflator, and then checked for leakage. The leakage is detected by either listening for escaping air or holding the glove against the tester’s cheek to feel air releasing.
As stated in ASTM specifications for In-Service Care and Use of Rubber Gloves and Sleeves, gloves and sleeves should be expanded no more than 1.5 times their normal size for type I, and 1.25 times normal for type II during the air test. The procedure should then be repeated with the glove turned inside out. In addition to this daily testing, OSHA requires “Electrical protective equipment shall be subjected to periodic electrical tests.” OSHA does not elaborate on a time frame for these tests, but ASTM F 496 does provide direction. It states that gloves being used in the field must be electrically retested every six months.
Gloves that have not been placed into service after an electrical test shall not be placed into service unless they have been electrically tested within the previous 12 months. See reference below for Testing Agency information. OSHA recognizes that gloves meeting ASTM D 120-87, Specification for Rubber Insulating Gloves, and ASTM F 496, Specification for In-Service Care of Insulating Gloves and Sleeves, meet their requirements.
INSPECTION
In order to maintain the highest level of insulating protectionand ensure long life, it is essential that gloves (and sleeves) are properly cared for and stored.
Before each use, gloves and sleeves should be inspected for holes, rips or tears, ozone cutting, UV checking and signs of chemical deterioration. Refer to ASTM F 1236, Standard Guide for Visual Inspection of Electrical Protective Rubber Products for Additional Information.
Gloves and Sleeves should also be examined to determine if they show any damage as a result of chemical contamination, particularly from petroleum products. The first sign of exposure is swelling in the area of contamination. Should any rubber equipment be exposed to chemical contaminants or be suspect of any other physical damage, it should be turned in for inspection, cleaning and electrical testing.
Since sleeves cannot be inflated, they are inspected along the edge as they are rolled. Rolling will stretch the sleeve along the edge, making cuts, tears and ozone cutting more visible. After the outside of the sleeve is inspected, the procedure should also be repeated with the sleeve turned inside out.
COMMONLY ASKED QUESTIONS
Q. Can I just use the rubber glove only, and not have to buy the leather part?
A. Leather protective gloves should always be worn over rubber insulating gloves to provide the needed mechanical protection against cuts, abrasions, and punctures.
Q. Would re-testing be needed if I don’t use the gloves very often and visually see no damage?
A. Yes, re-testing is still needed to verify the integrity of the material and to ensure electrical safety is maintained for the user.
Q. If I find a hole, can I just “patch it” - like a tire inner tube?
A. No - because this would not comply with ASTM or OSHA Standards for Electrical Protective Gloves, and it would not pass Accredited Laboratory Testing.
From: Electrical Safety & Arc Flash Handbook Handbook, Volume 3, The Electricity Forum
On-Site Training
Interested in cost effective, professional on-site electrical training?
We can present an Electrical Training Course to your electrical engineering and maintenance staff, on your premises, tailored to your specific equipment and requirements. Click on the link below to request a Free quotation.
EF PARTNER MEDIA
Videos
Product Showcases
Shared Media