Guidelines for the Installation of Cable In Cable Trays
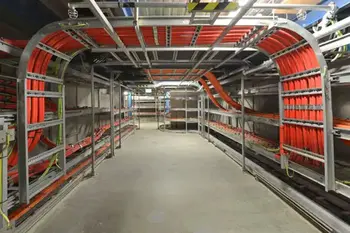
The use of ladder-type trays as raceways for insulated cables is becoming more prevalent. These raceways are being more heavily loaded with increasing number and size of cables being installed. With this growth in the use of tray, it is increasingly important that the tray and cable be installed within industry recognized practices. Discussed are the installation in tray of single and multi-conductor insulated cables with design limitations, example calculations, equipment, and equipment usage and its limitations.
For over thirty years, the use of a ladder-type tray as a rigid structural system for support of cables has grown dramatically. Accompanying this increase is the need for larger and longer cables to be installed. Designers and installers are continually faced with difficult challenges in the layout and installation of cable in tray. It is incumbent that pre-planning of an orderly sequence of events takes place to ensure that a successful installation occurs within recognized limits. Cable installed in tray is subject to many of the same considerations as cable being installed in conduit systems. Correctly calculated data and adherence to the design limits of the cables being installed with respect to tensions, sidewall pressures, and minimum bending radii increases the probability for a successful installation. Damage occurs more frequently as a result of improper handling during installation, or inadequate protection after installation. Cable tray layout must take into consideration the design limits of the cable.
Installation Design Considerations and Formulas
Tensions
The maximum allowable pulling tension that can be applied safely to a cable varies with the size and material of the conductor, the number of cables, and the method of attachment between the pulling line and cable.
A. For pulling eyes and bolts the maximum tension is expressed as:
Tmax = .008 * N * A Eq. (1)
(For copper conductors and full hard drawn aluminum.)
Tmax = .006 * N * A (For soft aluminum) Eq. (2)
Where
Tmax = Maximum allowable pulling tension in lbs/(kg)
N = Number of conductors
A = Conductor area in circular Mils (mm2)
.006 or .008 = Allowable stress per circular Mil (mm2) area for referenced metals.
For pulling eyes and bolts, the tension generated in a straight section of cable tray is expressed as:
T = L x w x f Eq. (3)
Where
L = The length of the cable tray section in feet (m)
w = The total weight of the cable being pulled in pounds (kg).
f = The coefficient of friction.
A. Range of .15 to .25 is recommended for the coefficient of friction. This coefficient is a function of the condition and alignment of sheaves.
B. For basket grips, the limit is 1000 lbs (453.6 kg/m) per grip or the value calculated in equation (1) whichever is smaller. This limit applies to a single conductor cable, a multi-conductor cable with a common overall jacket, two or three twisted cables, or paralleled cables using one grip. It is desirable to pull the cable by the conductors if this choice can be made rather than other type grips.
C. For conductor wedge-type compression grips, the grip manufacturer should be consulted for design limits of these devices. The same limits apply to these devices as pulling eyes and bolts.
Found In: Wire and Cable and Wiring Methods Handbook - Vol. 3
On-Site Training
Interested in cost effective, professional on-site electrical training?
We can present an Electrical Training Course to your electrical engineering and maintenance staff, on your premises, tailored to your specific equipment and requirements. Click on the link below to request a Free quotation.
EF PARTNER MEDIA
Product Showcases
Shared Media