How Often Must Employers Audit Their Electrical Safety Programs?
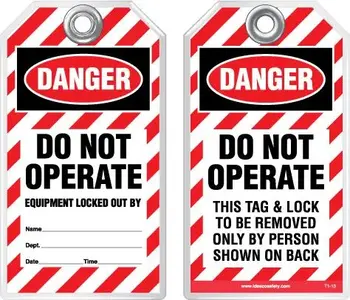
How often must employers audit their electrical safety programs? OSHA and NFPA 70E require audits at least every three years to ensure compliance, update safety procedures, and protect workers from electrical hazards.
How Often Must Employers Audit Their Electrical Safety Programs?
✅ Specifies the OSHA and NFPA 70E requirement for audits at least every three years.
✅ Ensures workplace compliance, hazard prevention, and updated safety procedures.
✅ Protects employees from electrical shock, arc flash, and other hazards.
Ensuring a safe working environment is paramount, especially when dealing with potential electrical hazards. Regular audits of electrical safety programs are crucial in maintaining compliance with standards and protecting workers. Employers conducting audits should understand the fundamentals of arc flash hazards to ensure their safety programs address the most critical risks.
Auditing electrical safety programs regularly is crucial for maintaining a safe workplace. While the NFPA 70E standard mandates audits at least once every three years, conducting them more frequently can help identify and mitigate potential risks more effectively. Electrical safety audits encompass various aspects, including documentation review, equipment inspection, work practice observations, and training assessments. By following the guidelines provided by NFPA 70E and conducting regular audits, employers can ensure a safe working environment for their employees and foster a strong culture of safety. Compliance checks should reference OSHA’s 29 CFR 1910.147 lockout/tagout requirements to confirm energy control procedures are being followed.
This comprehensive approach to safety audits not only ensures compliance with regulations but also enhances the overall safety culture within the organization, ultimately protecting both workers and assets from electrical hazards. A well-documented arc flash assessment process is essential for verifying that electrical safety programs meet both OSHA and NFPA 70E requirements.
What are Electrical Safety Audits?
An electrical safety audit is a systematic process of evaluating an organization's electrical safety program against established standards and best practices. These audits assess various aspects of the program, including:
-
Work Practices: The audit examines how electrical work is conducted within the organization. This includes safe work procedures**, adherence to lockout/tagout procedures**, and the use of appropriate personal protective equipment (PPE)**.
-
Electrical Equipment: The audit evaluates the condition of electrical equipment, looking for signs of damage, overloading, or improper installation**.
-
Training: The audit assesses the adequacy and effectiveness of electrical safety training** provided to employees. This includes training on hazard recognition, safe work practices, and the proper use of PPE**.
-
Electrical Safety Culture: The audit assesses the overall electrical safety culture** within the organization. This includes management commitment to electrical safety, employee awareness, and reporting of potential hazards**.
Why are Electrical Safety Audits Important?
Electrical safety programs offer several advantages for employers:
-
Identifying and Mitigating Risks: Audits uncover potential weaknesses or gaps in the electrical safety program before an incident occurs. This allows for corrective actions to be taken, reducing the risk of electrical accidents and injuries.
-
Ensuring Compliance with Regulations: Electrical safety audits help ensure compliance with relevant regulations and standards**, such as those established by the National Fire Protection Association (NFPA) 70E.
-
Demonstrating Due Diligence: Regular audits demonstrate an employer's commitment to electrical safety and can be valuable evidence in case of accidents or regulatory investigations.
-
Continuous Improvement: Audits provide a platform for continuous improvement of the electrical safety program. Identified deficiencies can be addressed, and best practices can be implemented to enhance electrical safety across the organization.
How Often Should You Do a Safety Audit?
According to the NFPA 70E standards, employers must audit their electrical safety programs at least once every three years. However, more frequent audits are recommended, especially in industries with high-risk electrical work. Regular audits help identify gaps in safety protocols and ensure that the practices align with the latest standards and regulations.
In addition to the triennial comprehensive audits, periodic field work audits should be conducted to ensure safe working conditions. These field audits focus on actual work practices and the use of electrical equipment, identifying potential electrical hazards in real-time and ensuring that safety measures are effectively implemented.
Information Provided by NFPA 70E Standard
The NFPA 70E standard for electrical safety in the workplace provides comprehensive guidelines for creating and maintaining safe working environments when dealing with electrical hazards. Key information provided by NFPA 70E includes:
-
Safety Program Requirements: Guidelines for developing an effective safety program that includes policies, procedures, and training for all employees involved in electrical work.
-
Risk Assessment Procedures: Detailed procedures for conducting risk assessments to identify and mitigate potential electrical hazards. A well-documented arc flash assessment process is essential for verifying that electrical safety programs meet both OSHA and NFPA 70E requirements.
-
Arc Flash Risk Management: Requirements for managing arc flash hazards, including the calculation of incident energy, establishing arc flash boundaries, and selecting appropriate personal protective equipment (PPE).
-
Safe Work Practices: Recommendations for safe work practices, including lockout/tagout procedures, use of appropriate tools, and safe handling of electrical equipment.
-
Training and Education: Requirements for ongoing training and education to ensure that all employees are aware of the hazards and understand the necessary precautions to take during electrical work.
By adhering to the NFPA 70E standards, employers can create a robust electrical safety culture that prioritizes the well-being of their employees and minimizes the risk of electrical incidents.
Importance of Regular Audits
Regular audits are vital in maintaining an effective safety program. They help ensure that the program remains up-to-date with the latest regulations and best practices. Additionally, audits provide an opportunity to review the effectiveness of safety training and the adherence to safe work practices. This continuous improvement process is crucial in fostering a culture of safety within the organization.
During an audit, specific focus should be given to the following:
-
Arc Flash Analysis: Ensure that all necessary measures are in place to protect workers from arc flash hazards. This includes proper labeling, PPE, and adherence to safe working distances. A well-documented arc flash analysis process is essential for verifying that electrical safety programs meet both OSHA and NFPA 70E requirements.
-
Training Programs: Evaluate the effectiveness of safety training programs and ensure that all employees are adequately trained in recognizing and mitigating electrical hazards. Incorporating NFPA 70E training into audit criteria ensures that worker education aligns with current safety standards.
-
Incident Reporting: Review incident and near-miss reports to identify trends and implement corrective actions.
Regular electrical safety audits are a critical component of a comprehensive approach to electrical safety** in the workplace. By identifying and addressing potential hazards, electrical safety audits help to create a safe working environment** for all employees involved in electrical work.
Related Articles
On-Site Training
Interested in cost effective, professional on-site electrical training?
We can present an Electrical Training Course to your electrical engineering and maintenance staff, on your premises, tailored to your specific equipment and requirements. Click on the link below to request a Free quotation.
EF PARTNER MEDIA
Product Showcases
Shared Media