Lockout Tagout Procedure Explained
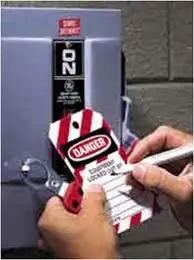
Lockout Tagout procedure ensures worker safety by isolating hazardous energy sources during maintenance. This OSHA- and NFPA 70E-compliant safety process prevents accidental startup, protects employees, and reduces electrical risks.
What is a Lockout Tagout Procedure?
A lockout tagout procedure is the cornerstone of hazardous energy control in the workplace.
✅ A step-by-step method to isolate electrical, mechanical, and hydraulic energy sources
✅ Uses locks, tags, and verification steps to ensure equipment stays de-energized
✅ Ensures OSHA and NFPA 70E compliance for workplace electrical safety
Request a Free Training Quotation
This formalized, written instruction is essential for ensuring that machinery or equipment is properly isolated during maintenance or servicing activities. A clear and effective procedure not only protects workers but also ensures compliance with federal safety regulations. Workers often benefit from a clear breakdown of Lockout Tagout Steps, ensuring each phase of the process is done correctly.
To comply with the Occupational Safety and Health Administration (OSHA) standard 29 CFR 1910.147, employers must implement lockout tagout (LOTO) procedures that ensure the complete energy isolation of any machine or equipment before maintenance or servicing begins. These procedures involve identifying all types of hazardous energy—such as electrical, hydraulic, pneumatic, or thermal—and applying an appropriate energy isolating device to block the potential for unexpected energy releases. Effective LOTO procedures also require addressing stored or residual energy, which may persist in the system even after shutdown. Proper energy isolation not only protects workers from serious injury but also supports a comprehensive safety culture aligned with OSHA's goals for workplace protection.
Establishing the Procedure
Every lockout tagout procedure must begin with a clear, structured plan. These procedures are more than just instructions—they represent a tailored safety protocol that reflects the specific needs of each machine, system, or facility. They must be comprehensive enough to guide workers and inspectors alike while remaining practical for field use.
Key components include:
-
Identification of Equipment – Define the specific machine or system subject to servicing.
-
Energy Source Documentation – Outline all energy types that must be isolated, including electrical, hydraulic, pneumatic, and more.
-
Authorized Personnel – Identify who is allowed to apply and remove LOTO devices.
-
Communication Requirements – Detail how affected employees will be informed about the lockout process.
-
Verification Methodology – Explain how workers confirm the effectiveness of the isolation.
-
Restoration Procedures – Describe steps for safely re-energizing the equipment after work is completed.
10 Steps of the Lockout Tagout Procedure
The lockout tagout procedure follows a structured 10-step process to ensure complete hazardous energy control:
-
Preparation – Identify the machine or equipment requiring servicing and review its energy sources.
-
Notification – Inform all affected employees that lockout tagout will be performed.
-
Shutdown – Power down the equipment using normal operating controls.
-
Isolation – Physically disconnect or block all energy sources, such as electrical, hydraulic, or pneumatic.
-
Lockout Devices – Apply locks to each energy-isolating device to prevent reactivation.
-
Tagout Devices – Attach warning tags to communicate that equipment is locked out.
-
Stored Energy Release – Safely release or restrain any residual or stored energy.
-
Verification – Test and confirm that all energy sources have been successfully isolated.
-
Servicing and Maintenance – Perform the necessary work while equipment remains secured.
-
Lock and Tag Removal – After work is complete, only the employee who applied the lock removes it, followed by safe re-energization.
Administrative Responsibilities
Developing a strong procedure is just the beginning. Employers are also responsible for maintaining and enforcing these energy control procedures. That includes providing necessary resources, assigning responsibility, and ensuring workers are trained in compliance. When several employees are involved, Group Lockout Tagout provides a method to protect everyone working on shared equipment.
Core administrative duties include:
-
Training Programs – Ongoing training ensures all employees know their roles and responsibilities.
-
Annual Inspections – Regular audits help confirm procedures are being followed and remain effective.
-
Recordkeeping – Maintaining training logs and program updates is essential for compliance and liability protection.
OSHA Compliance
OSHA’s Lockout Tagout regulation (29 CFR 1910.147) mandates that energy control procedures must be in writing, machine-specific, and reviewed periodically. The workforce must easily understand each procedure and be accessible when needed. Failure to meet these requirements can lead to serious enforcement actions.
The standard outlines expectations such as:
-
Documented steps for isolating and securing energy sources.
-
Procedures for verifying a zero-energy state.
-
Detailed guidance for removing lockout devices and returning equipment to service.
A lockout tagout procedure is the backbone of a safe work environment when servicing energized equipment. When clearly written, properly implemented, and periodically reviewed, it dramatically reduces the risk of injury and death. It serves as both a safety roadmap and a regulatory shield—vital to any comprehensive safety program.
Compliance depends on knowing the OSHA Lockout Tagout Standard, which defines the rules for hazardous energy control. Workers can gain essential skills through OSHA Lockout Tagout Training, designed to meet federal safety expectations.
Canadian Standards for Lockout Tagout
In Canada, lockout tagout procedures are guided by the CSA Z460 standard, which establishes requirements for the control of hazardous energy. This standard aligns closely with OSHA 29 CFR 1910.147 but includes additional guidance to reflect Canadian workplace conditions and provincial safety regulations.
Key points under CSA Z460 include:
-
Employers must develop written energy control procedures tailored to each piece of equipment.
-
Training must be provided to all authorized and affected employees, with refresher courses as needed.
-
Procedures must cover multiple forms of energy, including electrical, mechanical, hydraulic, pneumatic, and thermal.
-
Annual reviews and inspections are required to ensure compliance and ongoing effectiveness.
By following CSA Z460, Canadian employers protect workers, meet legal obligations, and align with best practices for hazardous energy control across industries.
Frequently Asked Questions
What standards govern Lockout Tagout compliance?
In the United States, OSHA standard 29 CFR 1910.147 regulates the control of hazardous energy. In Canada, compliance is guided by CSA Z460, with additional requirements set by provincial safety authorities. Both standards outline employer responsibilities, training requirements, and procedural guidelines for LOTO.
Who is responsible for applying lockout devices?
Only authorized employees—those trained and designated for servicing or maintenance—can apply lockout devices. Each device must be individually assigned, and the person who applied it is the only one allowed to remove it, ensuring accountability and safety throughout the procedure.
Related Articles
-
To clear up common issues, explore Lockout Tagout Questions, where frequently asked topics are explained in detail.
To ensure compliance and worker protection, The Electricity Forum offers specialized Construction Electrical Safety Training, including NFPA 70E Training and CSA Z462 Arc Flash Training courses. Request a free training quotation today to equip your team with the knowledge and skills they need to stay safe on the job.
On-Site Training
Interested in cost effective, professional on-site electrical training?
We can present an Electrical Training Course to your electrical engineering and maintenance staff, on your premises, tailored to your specific equipment and requirements. Click on the link below to request a Free quotation.
EF PARTNER MEDIA
Product Showcases
Shared Media