Lockout Tagout Steps
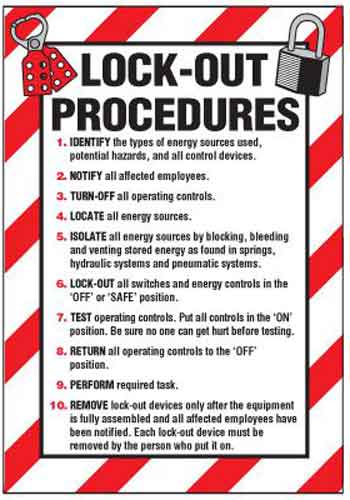
Lockout Tagout steps are the practical, repeatable tasks that workers perform each time a machine or system is serviced. These steps are not simply suggestions—they’re required by OSHA to protect employees from unexpected startup or the release of stored energy. Knowing and following each step, in order, can mean the difference between a safe job and a tragic accident. Refer to our OSHA Lockout Tagout Requirements page for a full breakdown of compliance standards.
Request a Free Training Quotation
As outlined by the Occupational Safety and Health Administration, following proper procedures when applying an energy isolating device is critical to controlling hazardous energy. The OSHA standard 1910.147 requires that all energy sources be identified and brought to a safe position before any servicing or maintenance begins. This step is crucial in preventing unexpected startup or release of potentially hazardous energy that could cause serious injury. Ensuring that each energy isolating device is applied correctly and verified helps maintain compliance and protects workers performing tasks on energized systems.
A well-defined Lockout Tagout procedure promotes consistent execution, enhances accountability, and significantly reduces the risk of injuries from hazardous energy sources such as electrical, mechanical, pneumatic, hydraulic, chemical, and thermal systems.
Why Lockout Tagout Steps Are Important
Hazardous energy can lead to serious injuries or fatalities if released while machinery is being serviced. Lockout Tagout (LOTO) steps provide a systematic process for isolating these energy sources to eliminate the risk of accidental startup. By following these steps, authorized employees can safely de-energize, maintain, and re-energize equipment across a wide range of industries. To learn how these procedures are documented and standardized, visit our Lockout Tagout Procedure guide.
In addition to improving safety, these procedures promote operational efficiency and help ensure OSHA LOTO compliance.
Best Practices for Lockout Tagout
-
Use clear signage and durable tags
-
Keep detailed LOTO procedure documentation for each piece of equipment
-
Conduct regular audits of your energy control procedures
-
Ensure all authorized employees receive up-to-date Lockout Tagout training
10 Standard Lockout Tagout Steps
1. Prepare for Shutdown
Before anything is turned off, workers must assess the equipment to understand what types of energy are involved. This includes electrical power, pressurized air, steam, gravity, and other hazards. Reviewing equipment manuals or diagrams helps identify potential dangers before beginning the lockout.
2. Notify Affected Employees
Workers who regularly operate or rely on the equipment need to be informed of the shutdown. This communication helps prevent misunderstandings and keeps everyone aware of what is happening. Notification should happen before the equipment is taken offline.
3. Shut Down Equipment
The equipment must be turned off using its normal control mechanisms, such as switches, buttons, or levers. This step ensures a controlled transition from operation to shutdown before isolating any energy.
4. Isolate All Energy Sources
Each energy source must be disconnected or otherwise blocked. Workers may close valves, shut off breakers, disconnect lines, or use other isolation methods. It's essential that every potential energy source be accounted for and isolated.
5. Apply Lockout/Tagout Devices
With the energy sources isolated, lockout devices are applied to secure them. Tags are also added to indicate who performed the lockout and when. Only authorized personnel can apply these devices, which physically prevent reactivation.
6. Release Stored Energy
Even after the equipment is shut down, dangerous energy may still remain. This can include pressure in lines, tension in springs, or stored electrical charge. Workers must release, block, or dissipate these energy sources before work begins.
7. Verify Isolation
Before starting work, it's critical to ensure that all energy has been fully isolated. Workers do this by attempting to operate the equipment and checking that no movement occurs. This confirmation step is often missed but is essential for safety.
8. Perform Maintenance or Servicing
With everything locked and verified, authorized personnel can now safely perform equipment maintenance, servicing, or inspections. All tools and parts should be handled carefully to avoid introducing new hazards. After servicing, ensure the machine is intact and all personnel are clear of the area. Ensure tools are removed and guards are reinstalled.
9. Remove Lockout/Tagout Devices and Re-Energize
Once the work is complete and the area is cleared, locks and tags can be removed—but only by the person who applied them. This ensures accountability and prevents unauthorized removal that could place others in danger.
10. Restore Power and Notify Workers
Energy can be safely restored with the locks removed and equipment cleared. Workers who were previously informed of the shutdown should now be notified that the equipment is back in service and ready for use.
Following these 10 Lockout Tagout steps is the most effective way to control hazardous energy during servicing. Each step builds upon the last to create a controlled, repeatable process that prevents injury and saves lives. Cutting corners in this process is never worth the risk.
Read More About Lockout Tagout
On-Site Training
Interested in cost effective, professional on-site electrical training?
We can present an Electrical Training Course to your electrical engineering and maintenance staff, on your premises, tailored to your specific equipment and requirements. Click on the link below to request a Free quotation.
EF PARTNER MEDIA
Product Showcases
Shared Media