What Constitutes an Electrically Safe Condition Explained
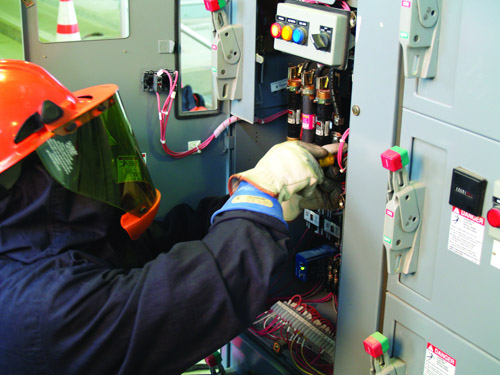
What constitutes an electrically safe condition? It's a key NFPA 70E safety question that ensures all electrical hazards are eliminated before work begins. This process protects workers from arc flash, shock, and equipment failure risks through proper de-energization protocols.
Request a Free Training Quotation
What Constitutes an Electrically Safe Condition?
An electrically safe condition is achieved when all sources of electrical energy are identified, de-energized, locked out, and verified as zero energy. It’s essential for NFPA 70E compliance and workplace safety.
✅ Power sources are isolated and locked out
✅ Absence of voltage is tested and verified
✅ Equipment is grounded where necessary
Working with electrical equipment presents significant hazards, including the risk of shock and arc flash. To minimize these dangers, it is essential to establish an electrically safe work condition (ESWC) before beginning any work. Let me outline the key steps required to create a safe environment, along with the importance of lockout/tagout (LOTO) procedures and the use of personal protective equipment (PPE). It also covers the common hazards that can arise if proper protocols are not followed. Performing an accurate arc flash assessment is a critical step toward establishing an electrically safe work environment.
Visually verifying that equipment is disconnected from energized parts is a crucial step in preventing an electrical hazard when working on electrical conductors and circuits. Even after de-energizing, stored electrical energy may still be present, posing a risk of accidental shock or arc flash. Proper procedures, including testing for voltage and ensuring all energized electrical conductors are isolated, help mitigate these dangers. Workers must follow lockout/tagout protocols and always confirm that circuits are fully de-energized before handling any components to maintain a safe working environment. Ensuring a system is properly locked out aligns with OSHA 1910.147 lockout/tagout standards, which support safe de-energization procedures.
What Are the Key Steps?
To ensure a safe work condition, several critical steps must be taken to de-energize the system and eliminate the risk of accidental contact with live components. According to the NFPA 70E standard for safety, the process includes:
-
Identify all sources of power: This involves locating the specific circuits, conductors, and equipment that will be worked on.
-
Disconnect and isolate the power supply: The system must be placed in a de-energized state by disconnecting it from all power sources. For systems operating at 50 volts or higher, this is especially critical.
-
Apply lockout/tagout (LOTO) devices: Ensure that the system cannot be accidentally re-energized by applying locks and tags to the disconnection points.
-
Verify the absence of voltage: Use a properly rated voltage tester to ensure that the system is not carrying any live voltage.
-
Ground the system if necessary: This may be required to prevent accidental re-energization from stored energy or nearby power sources.
By following these steps, workers can confirm that the system has been isolated and de-energized, minimizing the risk of shock or arc flash. A reliable arc flash study identifies potential hazards and helps enforce safety protocols before work begins.
How Do You Verify That an Electrically Safe Condition Has Been Achieved?
Once the power has been disconnected and lockout/tagout procedures applied, it is crucial to verify the absence of voltage. This is done using a voltage tester or meter to confirm that all conductors and circuit parts are in a de-energized state.
The verification process includes:
-
Testing the voltage tester on a known live circuit to confirm that it is functioning properly.
-
Applying the tester to the equipment, conductors, and circuit parts to ensure they are no longer carrying voltage.
-
Re-testing the voltage tester after verifying the system to ensure it is still functioning correctly.
This step is vital because visual checks alone are not enough to guarantee that the system is safe to work on.
What Personal Protective Equipment (PPE) Is Necessary When Establishing an Electrically Safe Condition?
Even when a system is believed to be in a de-energized state, there is still a risk of residual energy or equipment failure. Therefore, workers must wear appropriate personal protective equipment (PPE), including:
-
Insulated gloves and tools to prevent accidental contact with live components.
-
Flame-resistant clothing protects against burns from unexpected arc flash incidents.
-
Face shields, safety glasses, and hard hats are used to guard against flying debris or falling objects.
-
Insulated boots and protective footwear for work environments with high-voltage systems.
Wearing PPE ensures that workers remain protected from hazards throughout the process of de-energizing equipment and verifying its status. Proper arc flash PPE is only used once all efforts have been made to de-energize and verify zero energy. Before declaring a system safe, it’s necessary to calculate the arc flash boundary to determine safe approach distances.
Why Is Lockout/Tagout (LOTO) Critical in Creating an Electrically Safe Condition?
The lockout/tagout (LOTO) process is an essential safeguard that prevents equipment from being accidentally re-energized while work is being performed. This procedure involves physically locking the controls to power sources and applying tags to alert other workers that maintenance is in progress.
Without LOTO, there is a significant risk that someone could unknowingly restore power to the system, putting maintenance personnel in direct contact with energized equipment. In addition to preventing shock, LOTO also protects workers from other dangers such as mechanical movement in equipment that relies on energy.
In cases where the system cannot be fully de-energized due to equipment design, such as with critical systems like life-support machinery, additional safety measures must be implemented to protect workers.
What Are the Common Hazards If an Electrically Safe Condition Is Not Properly Established?
If a proper safe work condition is not established, several hazards can arise, including:
-
Shock: Contact with live conductors and circuit parts can lead to severe injury or even death.
-
Arc flash: A sudden release of energy caused by a system fault can create an explosion of heat, light, and pressure, severely burning or injuring workers.
-
Overcurrent protective device failure: If overcurrent protective devices, such as fuses or circuit breakers, are not properly maintained or installed, they may fail to trip during a fault, increasing the risk of fire or shock.
By failing to follow the necessary steps, the risk of injury or equipment damage increases significantly, making it crucial to establish a safe work condition before any tasks are carried out.
Creating a safe work condition is vital for preventing hazards in the workplace. Following the guidelines of NFPA 70E, workers and employers can ensure that equipment is de-energized, lockout/tagout procedures are in place, and the appropriate PPE is used. Verifying the absence of voltage and being aware of the common hazards associated with energized work further reduces the risk of shock and arc flash. By adhering to these safety protocols, companies can maintain a safe working environment and protect their employees from hazards.
Related Articles:
On-Site Training
Interested in cost effective, professional on-site electrical training?
We can present an Electrical Training Course to your electrical engineering and maintenance staff, on your premises, tailored to your specific equipment and requirements. Click on the link below to request a Free quotation.
EF PARTNER MEDIA
Product Showcases
Shared Media