Oregon embraces giant solar factory
Expanding a factory? Picking out carpeting?
Did anyone tell him that thereÂ’s a recession?
Buoyed by the potential promise of a green economy, Mr. Klebensberger, who heads the American branch of SolarWorld AG, a company based in Bonn, Germany, is ramping up production of solar cells in a retrofitted factory that had its grand opening last October — in the teeth of the financial crisis.
“Was I worried about our position? No!” says Mr. Klebensberger, dismissing any hint that he was nervous at the opening. And he remains just as bullish today. SolarWorld’s plant here, which makes enough cells to fit 1,700 solar panels a day, is the biggest of its kind in the United States.
For the residents of Hillsboro, and for the Oregon economy, SolarWorld’s presence is a welcome boon. Its employees enjoy being in start-up mode, while others like the cachet of working for a renewable-energy company — which goes down well in outdoorsy Oregon.
“Green is the way to go,” says Michelle Zillig, who worked at Intel for 18 years before joining SolarWorld as a technician. “People can only have so many computers.”
At first glance, the timing of SolarWorldÂ’s decision to invest $500 million in the new site during a recession, in a state with an unemployment rate second only to MichiganÂ’s, couldnÂ’t have been worse. Prices for the companyÂ’s solar panels have slid about 15 percent since the factory opened, a result of growing competition and slowing demand, especially in Europe. Two manufacturers, GE EnergyÂ’s solar branch and BP Solar, have cut production in East Coast plants.
But new federal incentives to encourage renewable energy in the United States will give the industry a boost, analysts say.
The recent stimulus package included grants for businesses and utilities that install solar energy systems, and the bank bailout package last year removed the dollar cap on a 30 percent tax credit for home installations. Makers of renewable energy equipment also received help in the stimulus package, signed by President Obama.
“I think the writing on the wall is the U.S. is going to be the big market,” says Jesse Pichel, a solar analyst at Piper Jaffray.
The message for solar companies, Mr. Pichel says, is “get your butt over to the U.S. if you want to participate and get some of that stimulus package money.”
The United States lost its status as the worldÂ’s leading solar manufacturer in the 1990s as interest surged elsewhere. Now it makes little more than 5 percent of solar panels worldwide.
Even with federal support and positive buzz, only a fraction of 1 percent of the electricity in the United States comes from solar panels, leaving ample room for the market to grow.
Germany, SolarWorldÂ’s home, is at the same latitude as southern Alaska, often has cloudy skies and is a much smaller country than the United States. Yet the number of installed solar panels in Germany is more than three times the amount in America. Spain and Japan are also ahead.
“Germany is not a natural for solar, but they’ve had vision, and policy followed the vision, and industry growth followed the policy,” says Raju Yenamandra, the vice president for sales at SolarWorld in California.
For manufacturers, the low penetration rate of solar in the United States spells opportunity. Companies lucky enough to still have financing are building or expanding operations in a range of states, including Oregon, Ohio and New Mexico.
As the German flag fluttering outside the SolarWorld factory in Oregon attests, foreign companies are largely driving the new American manufacturing push.
Mr. Klebensberger and his rivals are especially eager for solar to take off in the desert Southwest, where the sun beats down through often-cloudless skies. California has made a strong solar push, with the amount of solar power installed roughly doubling in 2008 from the previous year.
Recently, new installations of the type of rooftop-ready panels that SolarWorld makes have been growing strongly, with 70 percent more installed in the United States in 2008 than in 2007. In Europe, new installations roughly tripled last year, according to Emerging Energy Research, an independent research firm. But the European number is expected to fall sharply this year, in the wake of a decision by the Spanish government to cut its solar subsidy.
For its part, SolarWorld made its bet on manufacturing in the United States long before the stimulus package arrived. In 2006, it bought the solar division of the Shell Group, which operated factories in California and Washington. Mr. Klebensberger revamped the California factory, throttled back the existing facility in Washington and began scouting other sites in those states, as well as Alabama, Georgia and New Mexico.
“I don’t know how many brochures we got from states that offered us incentives and upfront money,” Mr. Klebensberger says.
The company ultimately settled on a semiconductor factory here that was built in the 1990s and swiftly abandoned after a downturn in the chip industry. Semiconductors are made from the same crystal material as solar panels, and having water and exhaust systems in place helped SolarWorld ramp up faster.
State incentives also helped: Oregon, which has been heavily recruiting wind and solar companies, provided SolarWorld with $40 million in business tax credits.
SolarWorld also gained access to a big pool of potential employees because it is situated in the heart of the Oregon “Silicon Forest,” surrounded by semiconductor plants and a short drive from a much larger Intel factory. SolarWorld’s employment has swelled to more than 500, some of them temporary, which gets the company about halfway to its goal of 1,000 permanent workers by 2011; the company holds new-employee orientations each Monday.
Inside the plant, the factory floor combines the mild chaos and urgency of a start-up with the scale of a public company. In one room, orderly rows of cylindrical furnaces stand like so many trees; they are used to grow crystals weighing several hundred pounds. The crystals are made from polysilicon, a derivative of sand, and form the core ingredient of the solar panels.
In other rooms, the cooked and cooled crystal ingots — looking like spent artillery shells — are sliced by machines into what are called wafers. Then they are made chemically suitable for generating electricity and are overlaid with electric wires, and a slim, dark cell emerges. (The cells, which resemble drink coasters, are sent to SolarWorld’s California plant to be strung together into the finished product that goes onto roofs.)
Many of the processes are still being automated, and the plant is also testing and expanding new systems in mid-production.
“I’ve got this radio here in case things go south,” says Willie Owens, an equipment engineer in goggles and jeans. He was testing new furnaces and water cooling equipment. If there were a big problem, he explains, he would have to hit a button within one minute to activate emergency systems.
The job, he says with relish, provides “an adrenaline rush sometimes.”
Like a number of other SolarWorld employees at all levels, Mr. Owens is a transplant from the semiconductor industry, whose big West Coast factories have suffered badly in the latest downturn. Hynix, for example, closed a plant in Eugene, Ore., last year, resulting in the loss of about 1,100 jobs.
Mr. Owens heard on National Public Radio that SolarWorld was coming to Oregon and decided to jump after seven years at a wafer manufacturer in Portland. “I saw this as an opportunity to get into something that was growing,” he recalls. “Glad I did.”
Even as SolarWorld charges ahead, adding new equipment and breaking ground for its factory expansion, there are daily reminders of the challenges ahead. The companyÂ’s share price has declined more than 30 percent in two years, to 21.05 euros (US$27.80), largely because of slowing demand and a growing number of manufacturers.
Asia has also become a manufacturing hub for solar power, and many panels from China have entered the market, although the recession has forced some companies to cut back. Suntech Power, a leading Chinese manufacturer, is now using just 55 percent of its factoriesÂ’ capacity, though it, too, is looking for factory space in the United States for the long term.
Like the rest of the industry, SolarWorld is also trying to adjust to the decline in panel prices, which are likely to keep falling into the summer, given the oversupply and the continuing credit crisis.
Mr. Klebensberger tries to put a positive spin on this, noting that the first quarter — whose results are due in a few weeks — is always relatively weak because Europeans avoid installing panels during the winter.
For all of last year, the companyÂ’s sales grew at a heady 31 percent. But the pace of growth in the fourth quarter slowed considerably.
Industrywide installations in the first quarter in California, the largest market in the United States, remain robust. Installers there are wary, however. They say demand dried up in the last six months because companies lack financing and homeowners are more worried about their mortgages than sinking $25,000 or more into making electricity on their roof.
Analysts say the first-quarter figures in California may have had a boost from projects that were already in the pipeline and that future numbers may be less robust. A year ago, installers say, they were calling manufacturers to ask for panels; now the situation is reversed, with manufacturers making sales calls.
In the meantime, the competition among manufacturers is likely to intensify. Even as some of the weaker solar companies resort to layoffs, a number of big names — including Schott, First Solar, SunPower and Sharp — are building, expanding or looking to build manufacturing plants in the United States. Sanyo, the Japanese electronics company, is building a solar wafer factory in Salem, Oregon’s capital, that is to begin production this fall.
Mr. Klebensberger relishes the competition and the potential boost it can give the American economy. Solar energy can provide jobs and energy security, he says, “so it’s a way out of the crisis.”
Related News
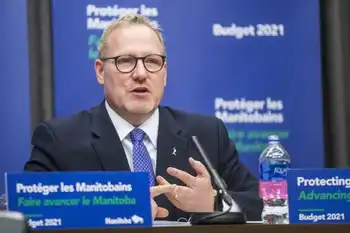
Manitoba looking to raise electricity rates 2.5 per cent each year for 3 years
WINNIPEG - The Manitoba government is planning to raise electricity rates by 2.5 per cent a year over the next three years.
Finance Minister Scott Fielding says the increases, to be presented in a bill before the legislature, are the lowest in a decade and will help keep rates among the lowest in Canada.
Crown-owned Manitoba Hydro had asked for a 3.5 per cent increase this year to help pay off billions of dollars in debt.
“The way we figured this out, we looked at the rate increases that were approved by PUB (Public Utilities Board) over the last ten years, (and) we…