Solar innovators forced to retool
FREMONT, CALIFORNIA - A few years ago, Silicon Valley start-ups like Solyndra, Nanosolar and MiaSolé dreamed of transforming the economics of solar power by reinventing the technology used to make solar panels and deeply cutting the cost of production.
Founded by veterans of the Valley’s chip and hard-drive industries, these companies attracted billions of dollars in venture capital investment on the hope that their advanced “thin film” technology would make them the Intels and Apples of the global solar industry.
But as the companies finally begin mass production — Solyndra just flipped the switch on a $733 million factory here last month — they are finding that the economics of the industry have already been transformed, by the Chinese. Chinese manufacturers, heavily subsidized by their own government and relying on vast economies of scale, have helped send the price of conventional solar panels plunging and grabbed market share far more quickly than anyone anticipated.
As a result, the California companies, once so confident that they could outmaneuver the competition, are scrambling to retool their strategies and find niches in which they can thrive.
“The solar market has changed so much it’s almost enough to make you want to cry,” said Joseph Laia, chief executive of MiaSolé. “We have spent a lot more time and energy focusing on costs a year or two before we thought we had to.”
The challenges come despite extensive public and private support for the Silicon Valley companies. Solyndra, one of the biggest firms, has raised more than $1 billion from investors. The federal government provided a $535 million loan guarantee for the companyÂ’s new robot-run, 300,000-square-foot solar panel factory, known as Fab 2.
“The true engine of economic growth will always be companies like Solyndra,” President Obama said in May during an appearance at the then-unfinished factory. But during the year that Solyndra’s plant was under construction, competition from the Chinese helped drive the price of solar modules down 40 percent. Solyndra rushed to start cranking out panels on Sept. 13, two months ahead of schedule, and it has increased marketing efforts to make the case to customers that Solyndra’s more expensive panels are cost-effective when installation charges are factored in.
“It definitely puts more pressure on us to bring our costs down as quickly as possible by ramping up volume,” said Ben Bierman, Solyndra’s executive vice president for operations and engineering.
Silicon Valley companies like Solyndra, Nanosolar and MiaSolé continue to receive hundreds of millions of dollars in customer orders and some plan to expand local manufacturing. But the rapid rise of low-cost Chinese manufacturers has made investors — who once envisioned the region’s future as Solar Valley — skittish about backing new capital-intensive start-ups.
“I don’t see another Solyndra being done,” said Anup Jacob, whose private equity firm, Virgin Green Fund, has invested significantly in Solyndra.
In the third quarter of 2010, venture capital investment in solar companies plummeted to $144 million from $451 million in the year-ago quarter, according to the Cleantech Group, a San Francisco research firm.
The paucity of capital and the sheer size of Chinese solar panel makers have proved particularly problematic for companies like Solyndra and MiaSolé, which make photovoltaic cells using a material called copper indium gallium selenide, or CIGS.
Unlike conventional solar cells, made from silicon wafers, CIGS cells can be deposited on glass or flexible materials, much as ink is printed on rolls of newspaper. Though the technology is less efficient at converting sunlight into electricity, the promise of “thin film” solar cells was that they could be made cheaply. But producing CIGS cells on a mass scale has turned out to be a formidable technological challenge, requiring the invention of specialized manufacturing equipment.
While Silicon Valley companies were working on the problem, silicon prices fell and Chinese companies like JA Solar, Suntech and Yingli Green Energy rapidly expanded production of conventional solar panels, supported by tens of billions of dollars in inexpensive credit from the Chinese government as well as other subsidies like cheap land.
Arno Harris, chief executive of Recurrent Energy, a San Francisco solar developer acquired by Sharp last month, said he chose to sign a supply deal with Yingli because the Chinese company offered low prices, quality products and financing.
“We realized that would enable us to bid competitive power prices from projects that could also be efficiently financed,” Mr. Harris said in an e-mail.
Chinese solar panel makers now supply about 40 percent of the California market, the largest in the United States, and the bulk of the European market, according to Bloomberg New Energy Finance, a research and consulting firm.
“We grow every year with double revenue and almost double capacity,” said Fang Peng, the chief executive of JA Solar, in a telephone interview from the company’s Shanghai headquarters. “At end of the year, we will have 1.8 gigawatts of capacity and will have grown from 4,000 employees at the beginning of this year to more than 11,000.”
By comparison, Solyndra expects to have a total production capacity of 300 megawatts by the end of 2011.
The competition from the Chinese prompted some Silicon Valley companies, like AQT Solar, to pursue new strategies to survive.
AQT has modified off-the-shelf machines used to make computer hard drives to create CIGS cells using a proprietary process. The Sunnyvale company, which has raised $15 million from investors, further cut its capital costs by manufacturing only solar cells, which it sells to other companies to package into solar panels.
Rather than build a factory from the ground up, the company recycled a 1970s-era rental building. “We moved in here in eight weeks, put our first 20-megawatt line up and did it for under a million dollars. That’s on Chinese time,” said Michael Bartholomeusz, AQT’s chief executive.
A mile away, another start-up, Innovalight, has abandoned solar module manufacturing altogether. The company had developed what it calls a silicon ink, which increases a solar cellÂ’s efficiency when it is printed on a standard silicon wafer.
After installing a 10-megawatt production line, in late 2008, Innovalight executives decided that, rather than compete with the Chinese, they would license the patented ink technology to them and avoid having to raise hundreds of millions of dollars to build factories of their own.
“How do you fight against enormous subsidies, low-interest loans, cheap labor and scale and a government strategy to make you No. 1 in solar?” said Conrad Burke, Innovalight’s chief. “Innovation will be the heart of the U.S. strategy, and although it might not create the same scale, we’re exporting well-protected technology to China and creating well-paying jobs here.”
As part of its corporate sustainability policy, Wal-Mart Stores last month acted to bolster American CIGS companies by signing a deal with a Silicon Valley solar installer, SolarCity, to put 15 megawatts of photovoltaic panels on its big-box stores and requiring that a significant percentage of them come from thin-film companies like MiaSolé.
Even so, SolarCity’s chief executive, Lyndon Rive, acknowledged that his company would also be installing a large number of conventional solar panels for the retail giant — nearly all of them made in China.
Related News
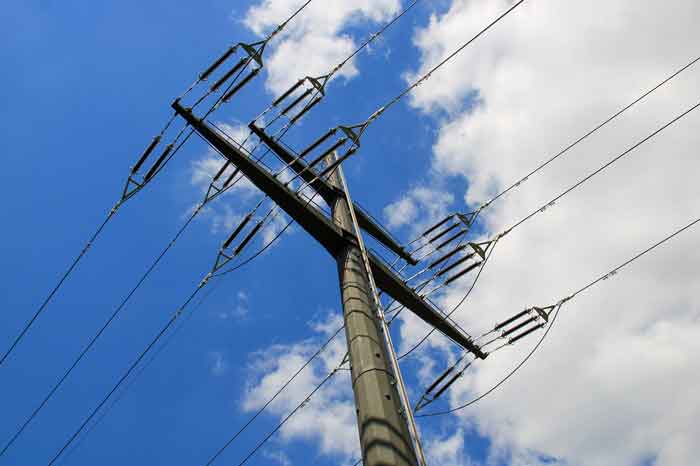
A New Era for Churchill Falls: Newfoundland and Labrador Secures Billions in Landmark Deal with Quebec
QUEBEC - St. John's, Newfoundland and Labrador - In a historic development, Newfoundland and Labrador (NL) and Quebec have reached a tentative agreement over the controversial Churchill Falls hydroelectric project, potentially unlocking hundreds of billions of dollars for the Atlantic province. The deal, announced jointly by Premier Andrew Furey and Quebec Premier François Legault, aims to rectify the decades-long imbalance in the original 1969 contract, which saw NL receive significantly less revenue than Quebec for the province's vast hydropower resources.
The core of the new agreement involves a substantial increase in the price that Hydro-Québec pays for electricity generated at…