DC Power Transformer
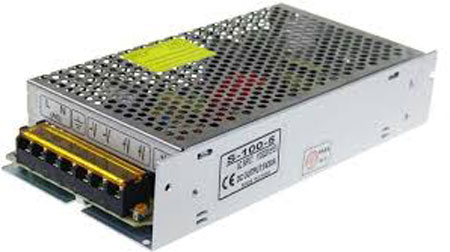
A DC power transformer is an essential device for industrial electricians to master, as it plays a vital role in distributing stable electricity and controlling the output voltage in complex electrical systems. Understanding how converters operate is crucial for ensuring a safe and reliable power supply to sensitive industrial equipment. Let's review that electricians will learn about the importance of devices in various applications, including the prevention of issues such as circuit tripping and damage caused by excessive starting currents. By gaining insight into the challenges and solutions associated with these devices, professionals can enhance the efficiency and stability of the electrical systems they work with daily.
Electrical Transformer Maintenance Training
Substation Maintenance Training
Request a Free Training Quotation
The Role of DC-DC Converters
A pivotal development in the management of electricity is the advent of converters, which are indispensable for adjusting voltage levels. Unlike traditional devices, these devices are specifically designed to step up or down voltage within circuits. Applications for converters span from powering compact electronic devices to enhancing the efficiency of renewable energy systems such as solar panels. By enabling precise control over output voltage, these converters ensure optimal performance across a wide range of applications, making them a cornerstone of modern electricity systems.
Limitations of Traditional Transformers
However, the effectiveness of electricity solutions is tightly bound to an understanding of the limitations of traditional devices. Conventional devices rely on the principle of electromagnetic induction, which requires a changing magnetic field—a condition inherently absent in direct current. This limitation highlights why traditional devices cannot directly process and underscores the necessity for alternative devices like converters and rectifiers. The inability of conventional transformers to handle DC emphasizes the ongoing need for innovation in electricity technology.
Design and Functionality of DC-DC Converter Transformers
The functionality of converter devices lies at the heart of this innovation. These specialized devices are engineered to operate in systems by utilizing advanced techniques such as self-saturation or square-wave-driven circuits. They facilitate efficient energy transfer within systems by altering voltage levels without the need for AC input. This capability is crucial for applications ranging from automotive electricity systems to high-efficiency industrial equipment. By bridging the gap between traditional AC transformers and modern needs, converter devices are redefining electricity management.
The Role of Rectifiers in DC Systems
Another critical element in electricity systems is the role of rectifiers. These devices convert AC to DC, enabling the integration of AC electricity sources with electricity systems. From powering everyday electronic devices to serving as a backbone for renewable energy setups, rectifiers play a crucial role in ensuring the compatibility and efficiency of electricity systems. By transforming AC input into a stable output voltage, rectifiers make it possible to harness and distribute electricity effectively, a fundamental requirement in today’s electrical supply networks.
Innovations in Photonic Transformers
As the demand for more efficient and compact electricity solutions grows, innovations in electricity technology have taken an exciting turn with the development of photonic devices. Unlike traditional magnetic-core devices, photonic devices leverage light-based technologies to perform voltage conversion. This groundbreaking approach offers several advantages, including enhanced efficiency and the potential for miniaturization. Though still in its early stages, photonic devices represent a promising frontier in the quest for advanced voltage conversion techniques.
Frequently Asked Questions
What is a DC Power Transformer, and how does it differ from an AC transformer?
A DC Power Transformer is a device used to convert a voltage level to another voltage level, either stepping it up or stepping it down. It differs fundamentally from an AC device, which relies on electromagnetic induction and requires alternating current to function.
AC devices operate on the principle of changing magnetic fields produced by AC, which induces voltage in a secondary winding. In contrast, devices do not use magnetic induction; they rely on electronic components like switching circuits, inductors, and capacitors to achieve voltage conversion. These circuits are often part of converters, such as buck (step-down), boost (step-up), or buck-boost converters.
Can DC transformers directly step up or step down voltage?
No, traditional electromagnetic devices cannot directly step up or step down voltage. This is because a device requires a changing magnetic field, which is only created by alternating current. To work with direct current, a converter circuit is used, often involving a switching mechanism to temporarily convert it to a pulsing signal that mimics AC for voltage transformation.
What are the primary applications?
- Consumer Electronics: Electricity supply units in smartphones, laptops, and other portable devices.
- Electric Vehicles (EVs): Voltage regulation for battery management and motor drives.
- Telecommunications: Powering equipment in remote installations.
- Industrial Automation: Providing appropriate voltage levels for sensors, actuators, and controllers.
- Solar Systems: Managing voltage from photovoltaic panels to match storage or grid requirements.
- Aerospace and Defense: Voltage conversion in space-constrained, high-efficiency systems.
How do you select the right DCPT for a specific application?
When selecting a, consider:
- Input and Output Voltage Range: Ensure compatibility with your source and load voltage levels.
- Power Rating: Choose a device that can handle the required electricity without overheating.
- Efficiency: Higher efficiency reduces energy loss and heat generation.
- Size and Form Factor: Especially important for compact or portable applications.
- Load Requirements: Consider whether the load is resistive, inductive, or capacitive.
- Regulation and Ripple: Check specifications for voltage stability and minimal output noise.
- Thermal Management: Look for designs with adequate cooling (e.g., heatsinks or fans) for high-electricity applications.
- Cost and Reliability: Balance cost against performance and durability.
- Certifications: Ensure compliance with relevant standards for safety and electromagnetic interference (EMI).
What are the advantages and limitations?
Advantages:
- Flexibility: Can be designed for a wide range of voltage and current levels.
- Compactness: Modern converters are smaller and more efficient than traditional AC devices.
- Efficiency: High efficiency, especially in switched-mode designs.
- Precise Regulation: Provides stable output voltage despite input fluctuations.
- Portability: Lightweight and suitable for mobile applications.
Limitations:
- Complexity: Requires more components (switching circuits, filters) than AC devices.
- Cost: Higher initial cost due to advanced electronics.
- Heat Generation: This can generate significant heat, necessitating robust cooling solutions.
- EMI: High-frequency switching can produce electromagnetic interference, requiring shielding.
- Durability: Sensitive to surges and may require protective circuits.
By understanding these aspects, you can effectively choose and utilize a DC Power Transformer for your specific needs.
A DC Power Transformer is a device used to convert electricity from one form to another, typically modifying voltage or current levels while maintaining a direct current output. Unlike traditional AC devices, which rely on alternating current for operation, it utilizes electronic components such as rectifiers, inverters, and switching circuits to achieve voltage regulation and conversion. These devices are widely employed in applications requiring stable electricity, such as in renewable energy systems, electric vehicles, and portable electronic devices. Their compact size, energy efficiency, and ability to handle varying loads make them indispensable in modern electrical and electronic systems.
On-Site Training
Interested in cost effective, professional on-site electrical training?
We can present an Electrical Training Course to your electrical engineering and maintenance staff, on your premises, tailored to your specific equipment and requirements. Click on the link below to request a Free quotation.
EF PARTNER MEDIA
Videos
Product Showcases
Shared Media