Electrical Explosion - Arc Flash
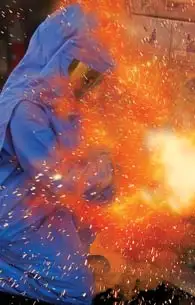
An electrical explosion is a sudden release of energy caused by a fault, arc flash, or short circuit. It produces intense heat, pressure, and light, often leading to fire, equipment damage, and injury. Proper PPE and training help reduce electrical explosion risks.
What is an Electrical Explosion?
An electrical explosion occurs when electrical energy is suddenly released due to a fault or arc event.
✅ Caused by arc flash, short circuits, or equipment failure
✅ Releases intense heat, sound, and pressure waves
✅ Can result in fires, injuries, and equipment damage
Electrical explosion incidents pose a significant threat to electrical engineering and maintenance professionals, making it crucial to understand their causes, risks, and preventive measures. These violent events result from faults in electrical systems that generate intense heat and pressure, leading to catastrophic failures, equipment damage, and life-threatening hazards. In industrial and commercial settings, explosions can disrupt operations, lead to financial losses, and pose a significant risk to workers. By identifying key risk factors and implementing effective safety measures, professionals can mitigate these risks and ensure compliance with safety standards, ultimately creating a safer work environment. Severe incidents like an arc flash fatality highlight the deadly consequences of inadequate hazard awareness and training.
Request a Free Training Quotation
One of the most well-documented and hazardous forms of electrical explosion is the arc flash, a sudden release of energy due to a fault in an electrical circuit. This phenomenon can produce temperatures hotter than the surface of the sun, vaporizing metal conductors and creating a massive pressure wave known as an arc blast. The intensity of these blasts can send molten metal fragments flying at high speeds, posing a deadly threat to anyone in the vicinity. Arc flashes are often caused by equipment failure, improper maintenance, or accidental contact with live components, making them one of the most pressing concerns in electrical safety. To understand how different PPE levels protect against intense heat and shrapnel, review our guide to arc flash PPE requirements.
Simply put, an electrical explosion is produced by ionized air and vaporized metal during a fault. Numerous toxic substances are produced, which can be inhaled. This, in addition to inhaling the intense heat, may increase the chance of death. For a deeper breakdown of energy release mechanics, see our explanation of arc blast explosion, where pressure waves accompany electrical discharges.
Physical Injuries May Include:
-
Shock Wave
-
Blinding light
-
Shrapnel
-
Intense heat
-
Contact with energized components
-
Toxic Smoke
-
Molten Metal
-
Noise Levels
-
Hearing Loss
-
Falling
-
Concussion
Causes
The underlying causes vary widely, but many stem from short circuits, overloaded circuits, and insulation failures. These faults create uncontrolled energy surges that generate excessive heat, leading to combustion or vaporization of surrounding materials. Another significant contributor is static electricity, particularly in environments where flammable gases, dust, or vapours are present. A single electrostatic discharge can be powerful enough to ignite an explosive atmosphere, making proper grounding and discharge control essential in such settings. Explore the root causes of arc-related accidents and how they escalate into explosions by reading how arc flash happens.
Preventing an electrical explosion requires a comprehensive approach to safety, including proper installation, routine maintenance, and adherence to industry standards. Grounding and bonding play a vital role in minimizing the buildup of static electricity and ensuring that electrical systems remain stable under normal operating conditions. Additionally, using arc-resistant switchgear, circuit breakers with fast fault interruption capabilities, and high-quality insulation materials can significantly reduce the likelihood of an explosion. Personal protective equipment (PPE) also serves as a critical last line of defence, shielding workers from the thermal and mechanical effects of arc flashes. Proper arc flash boundary calculations help ensure that workers maintain safe distances during energized tasks.
Real-world incidents serve as stark reminders of the consequences. Numerous industrial accidents have been attributed to failures in electrical systems, resulting in widespread destruction and loss of human life. Case studies often reveal a pattern of overlooked maintenance, improper wiring, or failure to follow established safety procedures. By studying these incidents, safety professionals can develop better strategies to mitigate risks and implement preventive measures that protect both workers and infrastructure.
Static electricity, often underestimated, plays a crucial role in electrical explosions, particularly in environments involving flammable or explosive substances. In industries such as oil and gas, chemical processing, and grain handling, even a minor static discharge can ignite explosive mixtures of dust, vapours, or gases. Implementing static control measures, such as humidity regulation, conductive flooring, and anti-static coatings, is essential in minimizing the potential for ignition and subsequent explosions.
An electrical explosion is not just a theoretical hazard—it is a real and recurring threat that demands vigilance, education, and proactive safety measures. While technological advancements have improved electrical system reliability, human error, lack of awareness, and substandard maintenance continue to contribute to devastating incidents. The key to preventing such disasters lies in rigorous training, proper equipment selection, and a strong culture of electrical safety. By recognizing the dangers and addressing them through strategic planning and adherence to best practices, industries can significantly reduce the risks associated with electrical explosions, ensuring safer working environments for all.
Frequency of Occurrance
Each day in North America, between five and 10 electrical explosions occur in commercial, industrial, and institutional electrical system equipment and machinery. Any electrical worker who is exposed to such an accident is at significant risk for serious injury or even death.
Arc flash, or explosion, is described by the National Fire Protection Association as “a dangerous condition associated with the release of energy caused by an electric arc.” A sufficient reduction of the insulation or the isolation distance between two energized components is the primary cause of an explosion.
Serious damage to equipment is a likely outcome in an explosion. Sometimes, affected equipment, such as a phase-to-phase circuit breaker, is so badly damaged that replacement is the only viable option. And, of course, the human body is equally capable of being destroyed or irreversibly damaged, with no replacement option.
Heat Radiation
Electric arc temperatures are considered to be approximately 4 times hotter than the sun’s surface. The temperature at arc terminals can reach 35,000°F (for reference, the surface temperature of the sun is ~9,000°F, and the temperature of a wood fire is ~900°F)
Heat radiation exposure is a function of:
-
Distance to arc
-
Available fault current
-
Fault clearing time
-
Equipment type
-
Gap between conductors (determined by equipment)
-
Vaporizes metals
-
Ignites clothing
-
200 degrees F - skin not curable (the point at which cell death occurs)
-
Possible to become fatally burned or seriously injured when working at a distance of 10 feet or more from an explosion.
Personnel Reaction
Some potential effects on personnel due to Heat Radiation:
-
External burns, potentially very severe
-
Internal burns, such as to the lungs due to ingestion of vaporized metal and superheated air
-
Health effects due to inhalation of toxic gases and heavy smoke due to the burning of paint, insulators, and other components
-
Partial or total loss of sight
-
Disability
-
Death
Gain insight into required procedures with our guide on NFPA 70E arc flash training to ensure compliance and reduce explosion risks.
Pressure Wave
An electrical blast (or explosion) is the result of the rapid expansion of air caused by an electric arc:
-
Peaks in the first ½ cycle of fault (~ 9msec)
-
Pressure levels of 2,160 pounds per square foot (psf) were detected near the explosion.
-
Caused by superheating of air and vaporizing of conductors (air expands to roughly 1670 times and copper expands to roughly 67,000 times its volume – i.e. 1 in3 becomes 1.4 yd3)
-
Function of arc fault gap and available fault current
Potential Effects on Personnel:
-
Injury due to blast
-
Collapsed eardrums leading to partial or near-total loss of hearing and possibly tinnitus – Sound levels of 141.5 decibels at 2 feet from the blast have been detected.
-
Collapsed lungs
-
Injuries due to shrapnel being ejected from equipment
-
One positive benefit: can lessen the effects of Heat Radiation due to personnel being thrown away from equipment, but this can also lead to other injuries
Learn the best practices for identifying risks with our comprehensive arc flash hazard analysis approach.
Related Resources
On-Site Training
Interested in cost effective, professional on-site electrical training?
We can present an Electrical Training Course to your electrical engineering and maintenance staff, on your premises, tailored to your specific equipment and requirements. Click on the link below to request a Free quotation.
EF PARTNER MEDIA
Product Showcases
Shared Media