How Often Should You Inspect an Extension Cord?
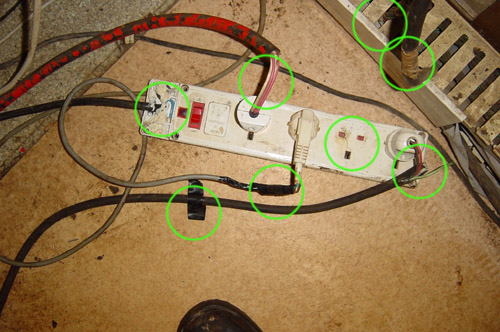
Inspect extension cords before each use to ensure safety. Look for damage such as frayed wires, exposed conductors, or cracked insulation. Regular checks help prevent electrical hazards and ensure compliance with workplace safety standards.
How often should you inspect an extension cord?
This refers to the recommended inspection frequency to ensure extension cords remain safe and functional in both home and industrial settings.
✅ Inspect before every use for visible damage
✅ Check monthly in low-risk areas and more frequently in industrial settings
✅ Replace immediately if damage is found
Request a Free Training Quotation
According to OSHA and best safety practices, extension cords should be inspected before each use to ensure there are no visible signs of damage, such as frayed wires, exposed conductors, or cracked insulation. Regular inspection helps prevent electrical shock, fire hazards, and equipment failure, especially in industrial or construction settings.
Extension cords are essential tools in both the workplace and at home, providing temporary power in various environments. However, improper use or failure to analyze them regularly can lead to hazardous situations, including electrical shocks, fires, or equipment failure. Conducting routine investigations ensures that extension cords remain in good working order and helps prevent dangerous incidents.To ensure the safe use of temporary power solutions, it is essential to avoid overloading an extension cord, as this can lead to overheating and increased fire risks. Always inspect the cord plug for signs of wear, discoloration, or damage, which may indicate internal faults. Regular inspections not only prevent safety hazards but also help extend the lifespan of extension cords by identifying issues before they become dangerous. Following proper usage guidelines is key to maintaining a safe and compliant work or home environment.
Let's address how often you should analyze extension cords, the signs of wear and damage to look for, relevant safety standards, and the importance of proper documentation and maintenance.If you work with industrial systems that frequently use extension cords, Electrical Safety Channel offers valuable guidelines and safety tips.
How Frequently Should You Inspect Extension Cords Used in the Workplace?
The frequency of analyzing an extension depends on how often it is used and the environment it operates in. In workplaces where cords are used daily, such as construction sites or manufacturing facilities, a regular investigation is recommended before each use. For environments where extensions are used only occasionally, a visual check before each use is typically sufficient. If cords are used outdoors, ensure they are weather-resistant and analyze them more frequently, as outdoor elements can accelerate wear and tear.
For more permanent setups where extension cords are used as part of daily operations, it’s also advisable to schedule a more thorough analysis at regular intervals, such as weekly or monthly, depending on the level of use and potential exposure to damage. Regular investigation of cords helps prevent power quality issues—get deeper insights on this in Power Quality Channel.
What Are the Signs of Wear and Damage When Inspecting an Extension Cord?
When investigating an extension cord, look for various signs of wear and damage that indicate it may be unsafe to use. Some of the key indicators include:
-
Frayed or exposed wires: The outer insulation should be intact without any tears, cuts, or missing sections that could expose live wires.
-
Damaged plug: Look for bent or broken prongs, which can affect the connection to power sources and increase the risk of shock or fire.
-
Burn marks or discoloration: These can be signs of overheating, indicating that the cord may have been overloaded or used improperly.
-
Loose connections: Analyze the plug to ensure it fits securely in outlets. Loose plugs can cause arcing, increasing the risk of fire.
-
Cracks or kinks: Repeated bending can weaken the structure, especially at the ends where the cord meets the plug.
By regularly checking for these issues, you can identify potential risks before they lead to equipment failure or injury.
Are There Specific Regulations or Standards For How Often Extension Cords Should Be Analyzed?
Yes, guidelines are set by organizations such as OSHA and other regulatory bodies that recommend specific analysis frequencies for electrical equipment, including extension cords. While these regulations may vary by industry, the general consensus is that if they are used in high-risk environments, such as construction sites, they should undergo daily visual investigations.
In industries where cords are used infrequently, investigations are recommended before each use and periodic audits are suggested. If it is used outdoors, ensure it is rated for outdoor use, and follow additional analysis protocols, as outdoor environments tend to increase wear and tear more rapidly.
Employers are also responsible for ensuring that employees are trained in proper investigation procedures and understand the risks associated with damaged or faulty cords. They can get training on proper cord inspection procedures Electrical Training Courses, which cover OSHA and NFPA-compliant practices.
How Should You Document Extension Cord Inspections, and Why Is It Important?
Proper documentation of investigations is essential for maintaining safety and compliance with regulations. Keeping a log of analysis ensures accountability and makes it easier to track the condition over time. This can help identify patterns of damage or failure, ensuring that necessary repairs or replacements are made in a timely manner.
When documenting an analysis, be sure to include the following details:
-
Date of the investigation
-
Name of the person performing the investigation
-
A checklist of potential hazards or issues, including frayed wires, damaged plugs, or signs of overheating
-
Any actions taken, such as repairing, replacing, or removing the cord from service
Documenting an investigation also helps employers demonstrate compliance with safety regulations during audits, reducing the risk of penalties for non-compliance.
What Risks Can Arise from Not Inspecting Extension Cords Regularly?
Failing to analyze regularly can lead to several significant risks, including:
-
Electrical shock: Damaged or frayed cords expose live wires, which can lead to electrical shocks, particularly if it is touched during operation.
-
Fire hazards: Overheating due to worn or damaged cords can ignite nearby materials, leading to potentially catastrophic fires.
-
Tripping hazards: Cords with damaged insulation or exposed wires can pose a physical hazard, increasing the risk of tripping or falling.
-
Equipment damage: Power fluctuations caused by faulty cords can damage tools and appliances connected to them, leading to costly repairs or replacements.
-
Non-compliance penalties: Safety standards often require regular investigations, and failure to comply with these requirements can result in fines or other penalties.
By conducting regular investigations and addressing any signs of wear or damage, businesses can reduce these risks and ensure a safer working environment for all employees.
Regularly analyzing extension cords is crucial to ensuring safety in both the workplace and home environments. They should be visually checked before each use, with more thorough investigation scheduled depending on the frequency of use and the environment they are operating in. Key signs of damage include frayed wires, damaged plugs, and overheating, all of which can pose serious safety risks, such as electrical shock or fire. About essential safety practices that go hand-in-hand with extension cord analysis by exploring Arc Flash Safety Channel.
Documenting each investigation is also important for maintaining safety records and demonstrating compliance with relevant regulations. Ultimately, taking the time to analyze and maintain cords properly reduces the risk of accidents and equipment failure, creating a safer environment for everyone involved.For detailed answers about arc flash hazards and analysis protocols, visit our Arc Flash Questions and Answers page.
Related Articles:
On-Site Training
Interested in cost effective, professional on-site electrical training?
We can present an Electrical Training Course to your electrical engineering and maintenance staff, on your premises, tailored to your specific equipment and requirements. Click on the link below to request a Free quotation.
EF PARTNER MEDIA
Product Showcases
Shared Media