What is Lockout Tagout? Energy Control
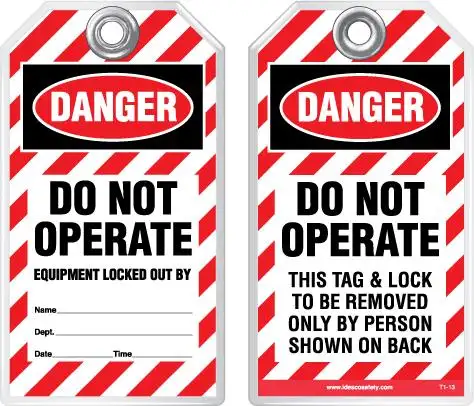
Lockout Tagout is a critical safety procedure that protects workers by controlling hazardous energy during equipment servicing. It ensures proper shutdown, isolation, and secure tagging to prevent accidental startup and electrical hazards.
What is Lockout Tagout?
Lockout Tagout (LOTO) is a safety system that prevents accidental machine startup and energy release during maintenance.
✅ Isolates electrical, mechanical, and other hazardous energy sources
✅ Uses locks and tags to secure equipment and warn personnel
✅ Ensures compliance with OSHA and NFPA 70E safety standards
Request a Free Training Quotation
Lockout Tagout in Practice
The process typically involves five critical steps: identifying energy sources, shutting down equipment, applying lockout devices, attaching warning tags, and verifying that energy has been isolated. Authorized employees apply locks and tags, while affected employees are trained to recognize and respect them. These steps ensure that equipment remains safely disabled until maintenance is complete and locks are removed by the same worker who applied them.
Learn More About Lockout Tagout
This short definition provides a basic overview, but a complete understanding requires a deeper look at procedures, standards, and training requirements.
For a comprehensive guide, visit our Lockout Tagout Pillar page.
Related Articles
On-Site Training
Interested in cost effective, professional on-site electrical training?
We can present an Electrical Training Course to your electrical engineering and maintenance staff, on your premises, tailored to your specific equipment and requirements. Click on the link below to request a Free quotation.
EF PARTNER MEDIA
Product Showcases
Shared Media