Lockout Tagout Devices Explained
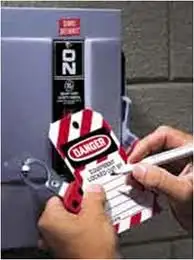
Lockout tagout devices secure hazardous energy sources during maintenance, preventing accidental startup. These OSHA- and NFPA 70E-compliant safety tools include padlocks, tags, hasps, and circuit breakers for effective worker protection.
What are Lockout tagout devices?
Lockout tagout devices are tools designed to isolate energy sources and protect workers during maintenance. They:
✅ Prevent accidental machine startup and energy release
✅ Ensure OSHA and NFPA 70E compliance with proper isolation
✅ Include padlocks, tags, hasps, breaker locks, and valve covers
Request a Free Training Quotation
Why LOTO Devices Matter
They are more than just compliance tools—they are essential safeguards that protect workers from life-threatening injuries. By physically isolating energy sources, these devices eliminate the risk of accidental startup during servicing. They also ensure compliance with OSHA and NFPA 70E standards, helping employers avoid costly fines and liability. Beyond safety, effective lockout tagout practices reduce equipment downtime, minimize accidents, and build a culture of trust where employees know their well-being is prioritized.
Training and Compliance
Workers can gain essential skills through OSHA Lockout Tagout Training, designed to meet federal safety expectations. Proper training ensures that employees understand how to select and apply LOTO devices, recognize hazardous energy sources, and follow OSHA and NFPA 70E requirements. Training also helps employers maintain compliance, reduce the risk of costly violations, and create a safer, more efficient workplace.
They are essential for controlling hazardous energy during machine and equipment maintenance or servicing. These devices are applied to energy-isolating devices—such as disconnect switches, valves, or plugs—to ensure that machinery cannot be inadvertently energized, preventing serious injuries or fatalities. Understanding the different types of devices, their applications, and OSHA requirements is critical to building a compliant and effective LOTO program. If you’re new to the concept, see What is Lockout Tagout? to understand the fundamentals and how they apply in industry.
To meet the requirements outlined in CFR 1910.147, employers must implement lockout tagout practices using devices that prevent the unexpected startup of machines during servicing. This includes securing not only primary energy isolating mechanisms but also secondary controls such as a push button that could accidentally energize equipment. A wide range of lockout devices is available to accommodate different equipment types and control configurations, ensuring that facilities can tailor their energy control strategies to match specific operational needs. Compliance depends on knowing the OSHA Lockout Tagout Standard, which defines the rules for hazardous energy control.
Lockout Devices vs Tagout Devices
While both are used to prevent the unexpected startup or release of stored energy, they serve different functions and offer varying levels of protection:
-
Lockout Devices are physical restraints—typically padlocks or mechanical attachments—that hold an energy isolating device in a safe or "off" position. They provide a positive means of securing energy isolation.
-
Tagout Devices are warning labels or signs attached to energy-isolating devices. While they don’t provide physical restraint, they communicate that the equipment must not be operated. OSHA allows tagout alone only when an energy isolation method is not feasible and when additional safety measures are in place.
Whenever possible, OSHA mandates that lockout is preferred over tagout because it provides a more secure form of energy control. A closer look at OSHA Lockout Tagout Requirements reveals the specific steps employers must follow for compliance.
Types of Lockout Tagout Devices
There is no one-size-fits-all device. Each type is designed for specific energy control points and must be selected based on the nature of the equipment and the energy involved. Every facility needs a documented Lockout Tagout Program to integrate policy, procedures, and training into daily operations.
1. Electrical Plug Locks
Used to cover and secure electrical plugs on portable equipment. These devices prevent the plug from being reinserted into the outlet during servicing.
2. Circuit Breaker Locks
These are applied directly to circuit breakers, preventing them from being switched back to the "on" position. Models vary based on breaker type and manufacturer.
3. Valve Locks
-
Ball Valve Lockouts: Encase the valve handle to prevent rotation.
-
Gate Valve Lockouts: Fit over the valve wheel and are usually adjustable by diameter.
-
Butterfly Valve Lockouts: Clamp over the valve handle and block it from movement.
4. Pneumatic Locks
Used on air compressor lines to block airflow. These devices typically clamp directly to the air hose connection or the fitting.
5. Plug and Cord
Enclose power cords or plugs to block access. This is useful in environments where machinery is powered by a simple power cord.
6. Group Lockout Boxes
These allow multiple workers to apply their personal locks to a central box holding the primary lockout key. It ensures that no single worker can re-energize the equipment until all locks are removed. When several employees are involved, Group Lockout Tagout provides a method to protect everyone working on shared equipment.
7. Lockout Hasps
These metal loops allow multiple padlocks to be applied to a single isolation point, which is common in team-based maintenance scenarios.
8. Tagout Devices
OSHA-compliant warning tags that identify the machine lock's authorized worker, date, and purpose. Tags must be durable, securely fastened, and legible.
Choosing the Right Device for the Job
Selecting the correct lockout device depends on the type of hazardous energy present and the energy isolating mechanism used. A proper match ensures effectiveness and compliance.
-
For electrical panels, circuit breaker safety locks are essential.
-
For compressed air systems, pneumatic safety locks or plug safety locks are appropriate.
-
Choosing between ball, gate, or butterfly valve safety locks for valves depends on the valve type and handle configuration.
When unsure, refer to the equipment manufacturer’s documentation or conduct a hazard assessment. OSHA mandates that devices must be standardized, durable, and substantial enough to prevent accidental removal. Step-by-step guidance is covered in our Lockout Tagout Procedure, outlining how to properly shut down, isolate, and secure equipment.
Examples of Correct and Incorrect Applications
- Correct: Use a gate valve safety lock that completely covers the handwheel and apply a padlock through its designated latch point.
- Incorrect: Placing a tag on a valve without any physical restraint when a lockout tagout device could have been applied.
Improper device use can lead to OSHA violations and, more importantly, create unsafe conditions for workers. Therefore, it’s essential to train authorized employees on proper device selection and use.
LOTO devices are more than safety accessories—they’re essential tools for preventing unintended energy releases. Selecting and applying the right device for each energy isolating point is central to LOTO effectiveness. By understanding the types of hazardous energy and choosing compliant, task-specific equipment, employers can meet OSHA standards while protecting workers from harm.
For a full overview of the topic, start with our Lockout Tagout guide, which explains why energy control is critical for workplace safety.
To clear up common issues, explore Lockout Tagout Questions, where frequently asked topics are explained in detail.
Related Articles
-
To clear up common issues, explore Lockout Tagout Questions, where frequently asked topics are explained in detail.
To ensure compliance and worker protection, The Electricity Forum offers specialized Construction Electrical Safety Training, including NFPA 70E Training and CSA Z462 Arc Flash Training courses. Request a free training quotation today to equip your team with the knowledge and skills they need to stay safe on the job.
On-Site Training
Interested in cost effective, professional on-site electrical training?
We can present an Electrical Training Course to your electrical engineering and maintenance staff, on your premises, tailored to your specific equipment and requirements. Click on the link below to request a Free quotation.
EF PARTNER MEDIA
Product Showcases
Shared Media