Which Procedures Should You Follow to Protect Against Electrocution?
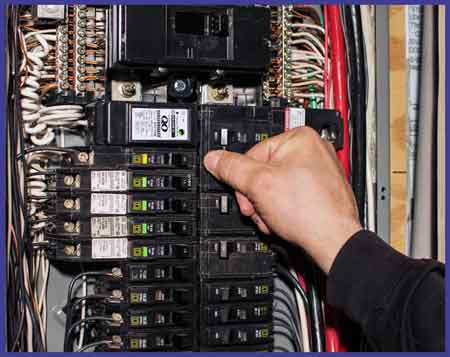
Which procedures should you follow to protect against electrocution? Use lockout/tagout practices, wear insulated PPE, and verify power is de-energized. These essential steps reduce the risk of electric shock during maintenance, repair, or installation of electrical equipment.
Request a Free Training Quotation
Which procedures should you follow to protect against electrocution?
This question addresses the vital safety practices necessary to avoid electric shock hazards in electrical work.
✅ Follow lockout/tagout (LOTO) procedures before starting any work
✅ Always wear appropriate insulated personal protective equipment (PPE)
✅ Use voltage testers to confirm that circuits are fully de-energized
Understanding and implementing the right safety protocols is crucial for preventing fatal incidents and ensuring worker safety and protection. Every step plays a vital role in minimizing the risk of electrical shock, from lockout/tagout procedures to the proper use of personal protective equipment (PPE) and adherence to NFPA 70E standards. This article outlines the essential procedures that electrical professionals must follow to create a safe working environment and maintain compliance with regulatory requirements in both the United States and Canada.
Frequently Asked Questions
What Are the Essential Lockout/Tagout (LOTO) Procedures to Prevent Electrocution During Electrical Maintenance?
Lockout/tagout (LOTO) procedures are essential for ensuring that energized systems are safely de-energized and cannot be accidentally re-energized during maintenance. These procedures involve isolating the power source from the equipment and placing locks and tags on switches or circuit breakers to prevent accidental activation.
The steps include:
-
Identifying all power sources connected to the system.
-
De-energizing the equipment by shutting off circuit breakers and disconnecting power supplies.
-
Applying locks and tags to the disconnecting devices. These locks ensure that only authorized personnel can reactivate the system.
-
Verifying that the system has been fully de-energized by performing a test.
-
Communicating with other workers to ensure everyone is aware of the LOTO procedures in effect.
By following these steps, workers can prevent accidental electrocution, which is often caused by unexpected re-energization of systems. For details on how OSHA defines electrocution risks and compliance expectations, visit our OSHA electrical safety resource.
How Does Proper Grounding of Electrical Equipment Help Prevent Electrocution?
Proper grounding is a key safety procedure for protecting against electrical hazards. Grounding ensures that any unintended contact with energized components does not lead to severe injury. A grounded system provides a safe pathway for electrical currents, redirecting them away from workers and reducing the risk of electrical shock. Grounding systems must be properly installed and regularly inspected, as outlined in our guide on electrical safety grounding.
Ground fault circuit interrupters (GFCIs) are essential devices that detect an imbalance in the electrical current and shut off the power when necessary, thus preventing hazards like electrical shock. Grounding also applies to power tools, ensuring that these devices remain safe to use. Equipment that is not grounded or poorly maintained may become dangerous over time, increasing the risk of electrocution.
What Personal Protective Equipment (PPE) Should Be Worn to Protect Against Electrocution?
Using the correct personal protective equipment (PPE) is vital for preventing injury from electrical hazards. Workers must wear protective gear appropriate for the task and voltage level they are working with. Key PPE includes:
-
Insulated gloves and boots that protect against electrical shock.
-
Flame-resistant clothing protects against burns from an arc flash.
-
Double-insulated power tools and equipment provide an extra layer of protection.
-
Hard hats and face shields are required to guard against falling debris and sparks during work on electrical circuits.
In addition to PPE, using proper power cords and extension cords is necessary to minimize the risk of electrical hazards. Damaged cords must be replaced immediately to avoid potential shock or electrocution. Learn how OSHA's lockout/tagout requirements align with best practices by reviewing the OSHA lockout tagout standard.
Why Is Maintaining Safe Distances from Energized Electrical Systems and Overhead Power Lines Critical in Preventing Electrocution?
Maintaining safe working distances from energized systems, particularly overhead power lines, is essential to reduce the risk of contact with live parts. Workers in low-voltage environments can still face serious risks, making low voltage certification essential for safety assurance. Many electrocution incidents occur because workers unintentionally come too close to high-voltage lines while using ladders, scaffolds, or heavy machinery. Overhead power lines pose significant hazards, including electric shock and arc flash, particularly when protective distances are not maintained.
To prevent such accidents, workers should:
-
Always assume power lines are live unless confirmed otherwise.
-
Use insulated tools and maintain a safe distance when working near power lines.
-
Implement barriers or markers to indicate the location of overhead power lines in work zones.
These precautions can prevent accidental contact and reduce the risk of severe injuries or fatalities. When evaluating protective gear, it's essential to understand the role of arc flash labels in hazard communication and personal protective equipment (PPE) selection.
What Role Do Regular Safety Inspections and Audits Play in Reducing the Risk of Electrocution?
Regular safety inspections and audits are vital in identifying and mitigating electrical hazards before they lead to serious incidents. Inspections should include checking all electrical equipment, wiring, and permanent wiring installations to ensure they meet safety standards and are in good condition.
Some key areas to inspect include:
-
Power tools and their power cords for any signs of wear or damage.
-
Grounding systems must be properly installed and maintained.
-
Circuit breakers and other protective devices to confirm they are working correctly.
Additionally, audits should review the use of extension cords, ensuring they are not overloaded or used as permanent wiring solutions. Conducting regular safety audits can also help ensure that LOTO procedures and other safety protocols are followed correctly. Ensuring all wiring is code-compliant is part of a robust electrical safety program; explore our section on electrical safety procedures.
By implementing these inspection and audit practices, businesses can proactively identify and address potential electrical hazards, thereby reducing the risk of accidents.
Protecting against electrocution involves a combination of effective procedures, proper equipment, and ongoing vigilance. Following lockout/tagout protocols, using proper grounding techniques, wearing appropriate PPE, maintaining safe distances from energized equipment, and conducting regular safety inspections are critical steps in ensuring workplace safety. By adopting these practices, workers and employers can significantly reduce the risks associated with electrical hazards and create a safer working environment for all. For general protection guidelines across industries, see our dedicated article on electrical safety.
Related Articles:
On-Site Training
Interested in cost effective, professional on-site electrical training?
We can present an Electrical Training Course to your electrical engineering and maintenance staff, on your premises, tailored to your specific equipment and requirements. Click on the link below to request a Free quotation.
EF PARTNER MEDIA
Product Showcases
Shared Media