Wind power blades energize composites manufacturing
- The world’s growing appetite for wind energy is transforming wind blades into one of the hottest composite applications around. The huge build-up of wind-power generating capacity — particularly in the U.S, China, and Spain — has raised a bumper crop of new plants for manufacturing these composite parts.
The global wind energy market has grown 23% annually for the last 10 years, says Charles Kazmierski, project manager for Lucintel, a consulting firm in plastics, composites, and other industrial markets. He expects the global wind energy market for composites to be worth about $6 billion by 2012.
The U.S. wind industry has historically experienced a roller-coaster growth cycle dictated largely by the federal governmentÂ’s production tax credit, which subsidizes the industry. Chronic uncertainty over periodic renewals of the tax credit led to costly boom and bust cycles for the industry from 2000 to 2005, according to the American Wind Energy Association (AWEA). Availability of the credit spurred dramatic growth from 2005 to 2007. The market could experience a setback in 2009 if U.S. lawmakers fail to renew the credit by the end of 2008.
Even with the fate of federal tax incentives still unknown, the U.S. wind industry moved forward with new manufacturing installations at breakneck pace in the first quarter of 2008, putting 1400 Megawatts (MW), or about $3 billion worth, of new generating capacity in place, reports AWEA.
This ramp-up in production has put intense pressure on suppliers of resins, reinforcements, and core materials like balsa wood and PVC foam. Suppliers are focused on meeting quality and delivery objectives as wind-turbine makers globalize their operations to meet growing demand. “Until now this was primarily a European business, but now it’s a global business with supply in every major region,” explains Paul Langemeier, director of global market development for epoxy supplier Hexion Specialty Chemicals.
Most observers agree that long-term growth will require technical innovation to make wind more competitive with other forms of energy. One of the key trends is the push to improve productivity. Blade manufacturing via vacuum infusion or prepreg molding is labor intensive and producers are seeking ways to reduce cycle time and cut costs.
Robotic lay-up, enhanced finishing techniques, two-piece or segmented blades, and on-site manufacturing are potential tools to trim labor and logistics costs. New prepreg molding techniques are said to improve surface appearance and facilitate finishing. And resin and prepreg suppliers are introducing materials that cure faster and at lower temperatures.
As wind generating capacity increases, there is also a trend to bigger and lighter blades.
Observers envision greater use of carbon fiber — despite disadvantages of higher cost and tight supplies — due to its higher stiffness and lighter weight than standard E-glass.
Meanwhile, traditional E-glass and specialty glass products are holding off competition from carbon fiber through new chemistry and optimization to meet higher performance requirements.
A wind turbine is composed of several composite parts; but the blades, made of fiber-reinforced epoxy or unsaturated polyester, represent the largest use of material. Other turbine parts made of polyester include the nacelle (housing for the gearbox, generator, and other components) and the hub. The dominant processing method is vacuum resin infusion. It generates low VOCs and can evenly wet out large parts with a controlled amount of resin, thus facilitating production of lighter and less expensive blades.
Prepreg molding with a woven or unidirectional glass fabric is more costly but offers greater consistency because it already contains the matrix material (typically epoxy). Depending on blade size, either vacuum infusion or prepreg molding takes 12 to 24 hours.
Typically composed of 70% to 75% glass by weight, these aerodynamically designed blades must meet very strict mechanical requirements such as high rigidity and resistance to torsion and fatigue. High static and dynamic loads over a wide temperature range are typical during a 20-year service life. A standard 35- to 40-meter blade for a 1.5-MW turbine weighs 6 to 7 tons.
Both epoxy and polyester, and to a lesser extent vinyl ester, shared the wind blade business in the early days but epoxy earned preferred status as blades grew longer. Polyester is easier to process and is less expensive, but epoxy offers stronger mechanical performance — particularly tensile and flexural strength — for blades longer than 26 m (85 ft). Unlike epoxy, polyester needs no post-curing but the blades are generally heavier.
E-glass is by far the most used reinforcement, while more costly carbon fiber is employed on a limited basis for greater stiffness and reduced weight in longer blades.
The barriers to entry for wind blade manufacturing are formidable. They include the physical scale of the parts, the need for competitive technology and manufacturing know-how, a good supply base, global presence, and heavy investment. There are about 12 global wind turbine suppliers and the top four hold about 72% of the market, according to Kazmierski.
Most of these top manufacturers make their own blades, but some, like GE Energy, contract out to firms like Molded Fiber Glass Companies (MFG), Ashtabula, Ohio, and TPI Composites Inc., Scottsdale, Ariz. The worldÂ’s leading wind turbine maker is DenmarkÂ’s Vestas Wind Systems A/S (23% market share), followed by GE Energy, SpainÂ’s Gamesa (17%), GermanyÂ’s Enercon, IndiaÂ’s Suzlon (10.5%), and GermanyÂ’s Siemens.
The worldÂ’s leading blade maker is Danish-based LM Glasfiber A/S, which makes between 8,000 and 9,000 blades/year and has 25% market share. The company started manufacturing in 1978 and has expanded operations worldwide with new U.S. plants in Grand Forks, N.D., and Little Rock, Ark. It claims to have the largest total installed base of blades today: Every third turbine worldwide is fitted with its blades.
LM uses vacuum infusion and what it calls “smart engineering” to produce polyester wind blades that are less costly than epoxy but still boast high performance. The process has been optimized to create a strong, uniform laminate with more rapid hardening, which reduces production time by several hours, according to Steen Broust Nielsen, communications director.
LM has adapted its technology to produce the industryÂ’s longest wind blade. The 61.5-m (202-ft) blade, built for a 5-MW turbine from GermanyÂ’s REpower Systems, weighs 17.8 tons. The turbine has a rotor diameter of 126 m (413 ft) and the three blades cover an area almost the size of two football fields. Most remarkable is LMÂ’s ability to use E-glass for stiffness and light weight above the threshold length of 40 m where carbon fiber is generally considered.
LM uses robots and other automation to lay up glass mat in the molds and to glue the blade shells together. To streamline its process and reduce cycle time, LM is investing in new blade technology based on an undisclosed new fiber that reportedly will cut blade production time in half.
Half the $12-million budget of LM’s “Blade King” research program comes from the Danish National Advanced Technology Foundation. New technology is expected to boost efficiency of fiber lay-up and molding. LM is partnering with Denmark’s Aalborg Univ. and Risoe DTU on fiber development and with Comfil, a Danish specialist in thermoplastic composites.
In the U.S, MFG will soon open a new facility in Aberdeen, S.D., to produce blades for GEÂ’s popular 1.5-MW turbines. MFG entered the market by making 9-m blades in the late 1980s and has watched sales climb eight-fold over the last six years, according to Carl LaFrance, wind energy manager.
Like most other blade makers, MFG uses vacuum infusion to mold glass-reinforced blades from 34 to 49 m long. Design and process optimization play a critical role, according to LaFrance.
“It’s all in the details; it’s how you lay up the fabric, charge the mold, and how you get the resin to fill the mold.” Since production volumes are just now providing opportunities for automation, MFG relies on lean manufacturing techniques and 6-Sigma principles to wring out every possible process improvement.
TPI Composites is another strong player in the U.S., with new expansions in the U.S., Mexico, and China. The company is supplying GE Energy from a new 190,000-sq.ft. facility in Taicang, China, and a new 316,000-sq.ft. plant in Newton, Iowa. VienTek, TPIÂ’s joint venture with JapanÂ’s Mitsubishi Power Systems, recently tripled its blade-making capacity in Ciudad Juarez, Mexico, to about 500,000 sq.ft.
TPI uses its patented SCRIMP technology, a form of vacuum infusion available for licensing. Components made with the SCRIMP process are claimed to have higher fiber content than conventionally laid-up components. TPI says glass-to-resin ratios of 70:30 or higher can be achieved, compared with the typical 50:50 ratio, resulting in lighter and stronger parts.
Most turbine makers are globalizing their operations at a rapid pace. GermanyÂ’s Siemens Wind Power opened a wind blade plant in Fort Madison, Iowa, last year. Meanwhile, DenmarkÂ’s Vestas announced plans in August to build a blade plant in Brighton, Colo., to supplement its existing plant in Windsor, Colo. The two facilities are expected to produce 3,600 blades/year when the Brighton plant starts up in 2010.
Siemens has an innovative process that makes blades in one piece, unlike the typical blade that is made in two shells and glued together. SiemensÂ’ IntegralBlade technology uses vacuum infusion to make glass/epoxy blades in a closed process.
The molding system has a closed outer mold and an expanding, flexible inner bladder. Epoxy resin is injected under a vacuum and the blade is cured at high temperature in the mold. After curing, the blade is removed from the outer mold while the inner bladder is collapsed with a vacuum and pulled from the blade. The result is a seamless one-piece blade.
The IntegralBlade system reportedly offers several advantages, including shorter cycles and more efficient use of manpower and space. Only one mold set is required, notes Hendrik Stiesdal, chief technology officer for Siemens Wind Power. Additionally, there are no tolerance issues between the shells and structural spars.
Most important is that the blade is an integral structure with no glued joints that could weaken and potentially expose the structure to cracking, water entry, and lightning strikes. The process is used to make blades 30 to 52 m long.
SpainÂ’s Gamesa, which has blade plants in Ebensburg and Fairless Hills, Pa., molds about 4,500 blades/year. The company is one of only two leading suppliers (Vestas is the other) that utilize epoxy prepreg molding. Resin is distributed more homogeneously and in consistent amounts in prepreg molding, according to Emmanuel Garcia De La Pena, vice president of industrial operations. This ensures consistent thickness, better fiber orientation, and fewer weak points, he says, resulting in better mechanicals and lower weight than with vacuum infusion.
A smaller player in blade manufacturing is Knight & Carver, National City, Calif., a former custom boat builder that transformed itself into a wind blade repair and production specialist almost 10 years ago. The company has found a niche in the blade replacement market, producing 25-m epoxy prepreg blades in Howard, S.D. A unique feature is a pultruded spar cap that provides high strength and stiffness, according to Gary Kanaby, director of business development.
Knight & Carver also made 9-m blades for now-defunct U.S. Wind PowerÂ’s 100-kw wind turbine. These were made of vinyl ester for faster curing, via a one-piece bladder molding process. In a current project with the U.S. Dept. of Energy and Sandia National Laboratories (Albuquerque, N.M.), Knight & Carver developed a 27-m blade to work better at low wind speeds but not increase loads on the turbine in strong winds.
Blade makers struggling to meet burgeoning demand are looking to new materials to help raise overall productivity, reduce cycle time, and cut costs. For example, the new Airstone system of epoxy resins and hardeners from Dow Epoxy Systems expands DowÂ’s offerings for wind blades beyond just resins.
The company expects to broaden its market share by offering systems that tailor resin formulations for specific blade performance, according to Bernd Hoevel, global technology leader for wind energy. DowÂ’s new Airstone 780 E line of epoxy infusion materials offers extended pot life, faster curing, and improved cycle time.
Hexion is working with customers to develop new products that reduce weight, improve mechanicals, and deliver “more blades per unit time,” says Langemeier.
Meanwhile, Huntsman Advanced Materials is developing new epoxies that provide better crack and aging resistance for longer blades. Epoxies are also the dominant adhesive for gluing blade halves. Huntsman says its new toughened system is easy to process and offers improved resistance to aging and crack propagation.
Polyester and vinyl ester suppliers are working on new formulations with improved mechanical properties. At Reichhold Inc., a new Dion vinyl ester grade provides 10% to 15% more fatigue resistance and greater overall toughness for longer, lighter blades, according to Bill Schramm, director of global business development.
Ashland Composite Polymers Div. supplies Aropol G300 and M300 polyesters to LM Glasfiber and other blade makers. The companyÂ’s Derakane 601-200 vinyl ester recently won certification from Germanischer Lloyd in Germany, which oversees global standards for safety and performance of wind energy systems. The materialÂ’s physical properties are reportedly better than polyester and approach those of epoxy.
A key advantage over epoxy is shorter post-cure time. And a new polyester from AOC is being used by an undisclosed blade manufacturer. AOC declined to provide further details.
Glass suppliers have responded to the carbon-fiber competition for making longer and lighter blades. OCV Reinforcements came out with WindStrand direct rovings and knitted fabric based on a special glass that is said to be nearly 30% stronger, 15-20% stiffer, and 8-10% lighter than the companyÂ’s current E-glass. This gives blade makers a less costly solution than carbon fiber for blades 40-m long or longer, according to Wisdom Dzotsi, Americas marketing leader. In an exclusive arrangement, a leading blade maker uses WindStrand in a vacuum infusion application.
Chemistry and sizing improvements have resulted in higher-performing glass products like new Hybon 2026 roving from PPG Industries, which boasts 10% greater fatigue resistance than standard products. PPG is also working on stiffer reinforcements that fill the gap between E-glass and more costly carbon fiber.
FinlandÂ’s Ahlstrom Corp. (U.S. office in Windsor, Conn.) has launched CombiFlow, a special E-glass fabric with a PET flow layer for easier and faster resin infusion. The PET is sandwiched between two glass layers. Ahlstrom also announced plans to double capacity for specialty reinforcements in the U.S. by 2011. The capacity, aimed primarily at wind energy, will be added in two phases at Bishopville, S.C.
To reduce the cost of wind energy, developers want to maximize the amount of wind power they can capture. This has spurred demand for turbines with larger MW capacity and a corresponding increase in blade length. Over the last decade, average wind turbine capacity has doubled, thus cutting by 50% the number of turbines and blades necessary to generate a certain amount of power.
The average turbine generating capacity is moving from 1.5 MW to 2 to 2.5 MW. The future holds even larger turbines of 3 MW and up, particularly for offshore use. Today, the largest unit is a 7.5-MW prototype offshore turbine developed by Clipper Windpower Plc, Carpinteria, Calif. It has 50- to 60-m blades.
Many industry observers believe larger turbines will require carbon fiber to provide the necessary stiffness and light weight. Global carbon-fiber use in wind power today is only about 10 million to 12 million lb/yr, vs. over 200 million lb of glass. Vestas and Gamesa are the only top-tier firms using carbon fiber, primarily in the structural spar cap (central spine) of longer blades (40-m and up). Most carbon fiber use is in Europe, and it is applied sparingly with glass.
At a price of $10 to $13/lb, carbon fiber costs 5 to 20 times more than E-glass. So the goal is to use carbon fiber selectively for strength and stiffness without incurring high cost, says Robb Klawonn, president and CEO of Toho Tenax America, a maker of 24K tow product.
In vacuum infusion, carbon fiber is hampered by its inability to wet out efficiently, though more experienced blade makers have learned to overcome this problem. Consequently, more costly prepreg molding is the preferred and most efficient method to utilize carbon fiber. At the same time, carbon fiber historically suffers cost and availability issues.
However, carbon-fiber makers argue that new capacity puts supply more in balance today. Zoltek Inc., the leading carbon-fiber supplier for wind energy, has doubled capacity at its Hungarian plant every year since 2005, reaching 26 million lb this year. Zoltek sells a 50K tow product called Panex 35 for use in wind blades.
Depending on design, the economics of carbon fiber can be favorable in blades longer than 40 m, says Tim McCarthy, Zoltek vice president of marketing and sales. Conversely, other sources point to optimized design and engineering that allow use of E-glass in longer blades like LM Glasfiber’s 61.5-m behemoth. “It will be a long time before carbon fiber is used broadly, due to its cost,” says Siemens’ Stiesdal, whose company is working on 52-m blade made with E-glass.
The other supplier of 50K tow carbon fiber is GermanyÂ’s SGL Group. The company has a strategy of forward integration, which includes the 2007 acquisition of German prepreg maker Epo and the recent purchase of a 51% stake in GermanyÂ’s Abeking & Rasmussen Rotec GmbH Co., a leading independent wind blade maker. SGL also has a majority stake in glass fabric maker SGL Kumpers GmbH, Lathen, Germany. SGL plans to double its carbon fiber capacity to 24 million lb by 2012.
Productivity improvements also highlight the latest developments in prepreg molding. Hexcel Composites Ltd. launched a new epoxy prepreg thatÂ’s said to reduce cure time by 15% to 20%. A major advantage of HexPlyM19 is its low risk of uncontrolled exotherm in thick sections.
HexPly M19 reportedly reduces hot spots and allows more aggressive ramp-up rates to reach maximum cure temperature. The dwell is at a higher temperature and for a shorter time than with conventional prepregs. Faster overall cure cuts mold costs by up to 10% because less expensive tooling resins and coatings can be used, along with a less expensive tooling support system. Mold service life can also be increased, Hexcel says.
The company is working on a prepreg system with improved surface appearance to reduce finishing. To meet greater U.S. demand, Hexcel will open a new glass prepreg plant in Colorado in the second half of 2009.
Another leading prepreg supplier, Gurit in the U.K., is focused on optimizing glass content and reducing voids in cured laminates. To solve surface appearance problems, Gurit has developed Sprint IPT, an in-mold primer film that facilitates finishing and painting. Also, Gurit has developed Sprint prepregs, which consist of alternating layers of dry fabric and epoxy film, offering breathability and reduced void content.
A small Spanish manufacturer of wind turbines and blades has developed an automated blade production process that reportedly reduces labor, cuts cycle time by 75%, and produces more consistent blades.
MTorres (U.S. office in Santa Ana, Calif.) devised a patent-pending vacuum infusion process that imposes no limitation on blade length. It infuses the mold with epoxy in one shot, as opposed to multiple infusions with current systems, and also uses cool molds to manage exotherm.
The infusion system has a special head and tackifier that initially adds epoxy in small amounts to stabilize the glass lay-up, according to David Champa, general manager of the U.S. division.
The turnkey system requires just five workers to run five stations for lay-up, bagging, curing, joining, and painting. A gantry system automates glass lay-up. There is also automated bagging, a special bonding fixture to join the two blade halves, and self-powered moving molds.
Champa describes an almost cleanroom environment with extensive temperature-control systems and robotic finishing operations. The company is working with leading turbine makers in the U.S. and Europe and expects to commercialize it next year in the U.S. The processing system will cost between $5 million and $6 million with a two-year return on investment, according to Champa.
An extensive EU-funded research program called Upwind involves more than 40 wind energy specialists who will examine new materials and manufacturing methods for large blades from 70 to 120 m. The project is looking at natural materials like wood and bamboo and cellulose fibers from hemp, flax, and wood. These offer the same stiffness-to-weight ratio as glass and similar strength but are difficult to process, according to Povl Brondsted, head of research programs for the Risoe National Laboratory for Sustainable Energy at the Technical University of Denmark. Thermoplastics like PET and PP and bio-based resins are also being examined.
Upwind is also considering new assembly solutions to build blades in multiple sections. Also under investigation are better process controls and automation.
Related News
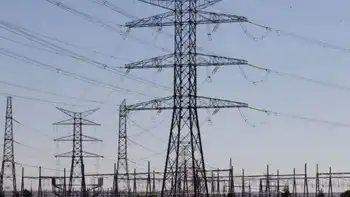
Electricity in Spain is 682.65% more expensive than the same day in 2020
MADRID - Electricity in Spain's wholesale market will rise in price once more. Once again, it will set a historical record in Spain, reaching €339.84/MWh. With this figure, it is already the fifth time that the threshold of €300 has been exceeded.
This new high is a 6.32 per cent increase on today’s average price of €319.63/MWh, which is also a historic record. Monday’s energy price will make it 682.65 per cent higher than the corresponding date in 2020, when the average was €43.42.
According to data published by the Iberian Energy Market Operator (OMIE), Monday’s maximum will be between the hours of…