High Resistance Grounding
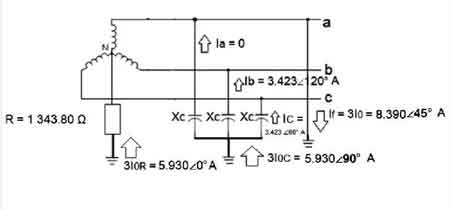
High resistance grounding limits fault current to a low level in electrical systems, reducing arc flash hazards and equipment damage. It enhances system reliability, safety, and uptime in industrial power distribution networks.
What is High Resistance Grounding?
High resistance grounding (HRG) is an advanced electrical grounding method designed to limit fault current in industrial and commercial power systems, offering enhanced safety and operational reliability.
✅ Limits ground fault current to safe levels, reducing arc flash and equipment damage.
✅ Improves system uptime by allowing continued operation even in the event of a single ground fault.
✅ Supports fault detection and coordination with grounding and bonding systems.
Grounding and Bonding and the NEC 250 Training
Electrical Grounding and the CE Code Training
Request a Free Power Quality Training Quotation
By connecting the system's neutral point to the ground through a neutral ground resistor, HRG restricts fault current to a low, manageable level during ground faults. This reduces the risk of equipment damage, minimizes downtime, and protects against dangerous conditions such as arc flash energy and arcing ground faults. HRG systems are particularly beneficial in environments where continuous operation is critical, as they enable the detection and localization of faults without interrupting the entire system. This method is a preferred solution in modern electrical distribution, striking a balance between safety and system efficiency.
Frequently Asked Questions
What Is High Resistance Grounding, and How Does It Work?
HRG is a system that connects the neutral point of an electrical power system to the ground through a neutral ground resistor. This resistor limits the current during an arcing ground fault, reducing the risk of equipment damage and increasing system reliability. Unlike solidly grounded systems, which allow high fault currents, HRG systems maintain low fault currents, making it easier to detect and locate ground faults without shutting down the entire system.
In HRG systems, when a fault occurs, the neutral voltage rises, allowing fault detection equipment to identify the issue. These systems work well with detection techniques such as how to check if an area is grounded. The key component, the neutral ground resistor, is designed to handle the fault current until the fault is cleared.
What Are the Advantages of Using High Resistance Grounding in Electrical Systems?
One of the main benefits of HRG systems is their ability to limit arc flash energy during faults. In solidly grounded or ungrounded systems, ground faults can generate high fault currents, resulting in hazardous conditions such as phase-to-phase faults and substantial equipment damage. By using HRG, the fault current is controlled, minimizing the chance of catastrophic failures and improving safety for personnel.
Another advantage is continuous operation. Since HRG systems limit the fault current, they enable the system to continue running during a fault, providing operators with time to safely locate ground faults and address the issue without incurring costly downtime. This makes HRG especially valuable in grounding systems where shutting down the power supply could lead to significant financial losses.
HRG also reduces stress on the system, improving equipment longevity. By limiting fault currents, the wear and tear on electrical components are minimized, reducing the risk of damage during faults.
How Does High Resistance Grounding Differ from Other Methods?
HRG differs significantly from both solidly grounded and ungrounded systems. In a solidly grounded system, the neutral is directly connected to the ground, allowing for large fault currents during a ground fault. While this method provides good fault detection, the high fault currents can cause extensive damage.
In contrast, ungrounded systems lack a direct connection between the neutral and the ground. This can lead to unpredictable fault conditions, where fault currents fluctuate, causing difficulty in ground fault detection and increasing the risk of insulation breakdown and multiple faults.
HRG systems strike a balance by using a resistor to limit fault current, reducing the risks associated with both methods. In terms of energy delivery, HRG interacts with the system’s apparent power, maintaining balance during faults.
What Types of Electrical Systems Are Best Suited for High Resistance Grounding?
HRG systems are ideal for capacitive load scenarios and earthing of industrial and commercial power systems, particularly where line-to-neutral loads are minimal. Industrial settings, such as manufacturing plants, chemical facilities, and power generation plants, benefit from HRG due to the need for continuous operation and safety during fault conditions.
In these environments, HRG helps prevent hazardous situations, such as arcing ground faults, which can lead to equipment failure and injuries. By reducing the fault current, HRG systems protect expensive machinery and ensure that operations continue even when a fault is detected. High-resistance grounded power systems are particularly useful in industries where electrical faults can lead to fires or explosions.
What Are the Maintenance and Monitoring Requirements for High Resistance Grounding Systems?
To ensure that an HRG system functions properly, regular maintenance and monitoring are essential. This includes inspecting the neutral ground resistor for signs of wear or damage, ensuring it functions correctly to limit fault current.
Monitoring includes evaluating apparent power vs. real power to track system stability, as well as routine testing of fault detection systems. These checks are vital to ensure the electrical grounding infrastructure remains reliable over time.
Maintaining HRG systems requires attention to fault-detection equipment, like ground fault relays, which should be calibrated to ensure precise fault detection. Proper monitoring allows for early fault detection, minimizing downtime and preventing damage to equipment.
High resistance grounding systems offer significant advantages for industrial and commercial power applications. By limiting fault current and controlling arc flash energy, HRG systems enhance safety, reduce the risk of damage, and allow operations to continue during fault conditions. Compared to solidly grounded and ungrounded systems, HRG offers a balanced solution that minimizes both the risk of high fault currents and the unpredictability associated with ungrounded systems.
For industries where operational continuity and safety are crucial, high-resistance grounding is the ideal solution. Regular maintenance and monitoring ensure the system operates correctly, enabling the quick detection and resolution of faults. As a result, high-resistance grounded power systems remain a trusted and effective method for fault protection in modern electrical distribution networks.
Related Pages
On-Site Training
Interested in cost effective, professional on-site electrical training?
We can present an Electrical Training Course to your electrical engineering and maintenance staff, on your premises, tailored to your specific equipment and requirements. Click on the link below to request a Free quotation.
EF PARTNER MEDIA
Product Showcases
Shared Media