SCADA Integration
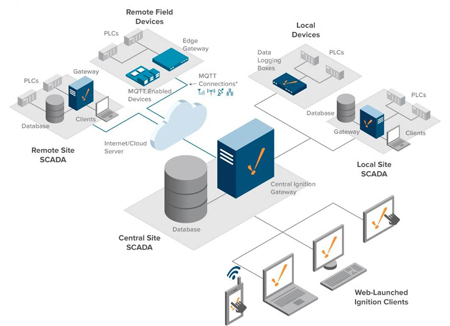
SCADA integration connects supervisory control systems with enterprise data platforms, enabling real-time monitoring, automation, and control of industrial or utility operations. It improves system efficiency, data flow, and decision-making across electrical grids, substations, and critical infrastructure.
What is SCADA Integration?
SCADA Integration refers to connecting SCADA systems with other devices, software, or platforms to enhance functionality, visibility, and control.
✅ Integrates field devices with central control systems
✅ Enables real-time data sharing and automation
✅ Supports better decision-making and operational efficiency
Integrating supervisory control and data acquisition within industrial automation environments has become essential to achieving operational efficiency, reliable monitoring and control, and optimized industrial processes. Thoughtful network design, industrial control strategies, and modern communications protocols enable seamless SCADA system integration anywhere in the world. For a foundational overview of Supervisory Control and Data Acquisition in electrical systems, visit our page on what is SCADA.
Key Elements of SCADA System Integration
Component / Concept | Description | Role in Integration |
---|---|---|
Programmable Logic Controller (PLC) | Industrial computer for automation and real-time control | Interfaces with field devices and executes logic instructions |
Human Machine Interface (HMI) | Visual interface for operators to monitor and control processes | Displays real-time data, alarms, and performance metrics |
Control Panel | Central hardware for housing and managing control systems | Physical hub for operator interaction and system wiring |
Distributed Control Systems (DCS) | Multi-level control structure across various process locations | Enables scalability and real-time decision-making |
Communications Protocols | Standards like Modbus, DNP3, IEC 61850 | Facilitate secure, reliable communication across devices and networks |
SCADA Software / Solutions | Platform for centralized control, data logging, and visualization | Manages process automation, trending, and remote access |
Real-Time Data Monitoring | Continuous collection of sensor and status information | Enables responsive control and predictive maintenance |
Network Design | Architecture of LAN, WAN, edge, and cloud systems | Ensures connectivity, redundancy, and security |
Cybersecurity Measures | Network segmentation, encryption, and authentication | Protects critical infrastructure from cyber threats |
Operational Efficiency Gains | Reduced downtime, improved response times, and automation of manual tasks | Lowers operating costs and enhances system reliability |
Real-Time Data and Distributed Control
At its core, integration leverages real-time monitoring and real-time data collected from programmable logic controllers and remote terminal unit networks. These devices feed telemetry into a control panel or human machine interfaces (HMI), forming the backbone of distributed control systems. Industrial control depends on accurately detecting sensor readings and sending commands instantaneously—essential for electrical engineering projects such as power grids, substations, and smart factories. To understand how these systems manage data and control equipment remotely, see our detailed explanation: How does SCADA work ?
Communications Protocols and Network Design
Selecting the correct communications protocols—such as Modbus, DNP3, IEC 60870, or IEC 61850—is critical to successful integration. These protocols support reliable, secure communications between devices and across networks. DNP3 and IEC standards, for example, are widely adopted in utility networks for their ability to prioritize packets, ensure time synchronization, and handle complex automation scenarios. Robust communication design is essential to maintaining synchronized, responsive operations in real time, even across geographically dispersed facilities.
Control Panels and Human-Machine Interfaces
A responsive control panel, integrated with modern human-machine interfaces, allows engineers and operators to visualize industrial control environments in intuitive ways. HMI dashboards convert raw data into actionable insights—displaying system health, status alarms, trend analytics, and operational statistics. When paired with powerful SCADA software and custom SCADA solutions, HMIs can support:
-
Alarm/event management and prioritization
-
Historical data logging and charting
-
Operator acknowledgment and decision support
-
Remote access to distributed assets
Design and Implementation Strategies
The design and implementation of a successful integration project begins with a modular system architecture. Field devices such as PLCs and RTUs gather localized data and transmit it securely to centralized servers. These servers, typically located in control rooms or network operations centers, manage supervisory control functions and interface with enterprise systems. Critical to this design is redundancy—dual communication paths, failover hardware, and backup data streams must be incorporated to minimize downtime. If you're designing or upgrading a system, our guide to SCADA architecture outlines the key components and communication layers involved.
Cybersecurity in SCADA Integration
Cybersecurity is another fundamental aspect. As SCADA integration increasingly involves connections with enterprise IT networks and remote access points, systems become more vulnerable to cyber threats. Effective security practices include:
-
Network segmentation and firewalls
-
Encryption and VPN tunnelling
-
Role-based access control and authentication
-
Intrusion detection and patch management
-
Air-gapped or unidirectional gateways for legacy assets
Enhancing Operational Efficiency Through Automation
Connecting dynamic field devices, embedded logic, and centralized oversight drives measurable gains in operational efficiency. With intelligent automation, SCADA integration enables:
-
Predictive maintenance based on sensor trends
-
Condition-based alarms for immediate fault isolation
-
Load balancing and energy optimization
-
Closed-loop automation that reduces manual intervention
By automating routine processes and creating a holistic view of system performance, engineers can proactively respond to anomalies, optimize resource allocation, and meet stringent uptime requirements.
Legacy Modernization and Future Readiness
For many facilities, one challenge is modernizing legacy infrastructure that was not designed for internet-connected or cloud-enabled operations. Older control panels and proprietary systems often lack the flexibility or security standards required for modern integration. Retrofitting these systems with interface modules or secure gateways can extend their functionality without necessitating a full replacement.
Meanwhile, newer SCADA solutions often support hybrid architectures, combining edge computing, local processing, and cloud-based analytics. This offers scalability and responsiveness across global operations, letting engineers and stakeholders view dashboards, configure alarms, and manage processes from anywhere in the world. Utilities seeking greater automation and control at the substation level can explore the benefits of Substation SCADA for real-time operations.
Best Practices for Successful Projects
To ensure a successful integration project, several best practices should guide the process:
-
Conduct a detailed network design plan with defined zones, IP structures, and protocol mappings
-
Implement phased rollouts, starting with a testbed environment
-
Validate HMI functionality and alarm priorities through user testing
-
Document all components, logic flows, and communication paths for ongoing maintenance
-
Train operators and technicians on both the software and hardware aspects of the system
For an in-depth look at how SCADA platforms enable system-wide visibility, read our coverage of SCADA monitoring in modern grid infrastructure.
The Future of SCADA Integration
As the future of industrial automation continues to evolve, SCADA integration is increasingly becoming a platform for edge analytics, AI-driven anomaly detection, and real-time collaboration between operational and business systems. Technologies such as OPC UA, MQTT, and RESTful APIs now enable open interoperability between smart field devices, controllers, and cloud environments.
By aligning system design with enterprise goals, integrating legacy systems with next-gen tools, and embedding security and flexibility into every layer, organizations can unlock the full potential of supervisory control and data acquisition. SCADA integration is not just about connecting devices—it’s about building a responsive, intelligent, and future-ready industrial ecosystem.
Related Articles
On-Site Training
Interested in cost effective, professional on-site electrical training?
We can present an Electrical Training Course to your electrical engineering and maintenance staff, on your premises, tailored to your specific equipment and requirements. Click on the link below to request a Free quotation.
EF PARTNER MEDIA
Product Showcases
Shared Media