SCADA Monitoring
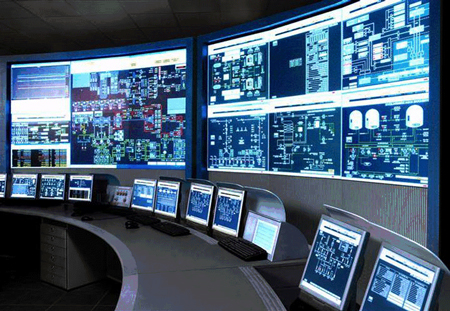
SCADA monitoring provides real-time data acquisition, system diagnostics, and remote control for power systems. It improves operational efficiency, enhances reliability, and enables preventive maintenance for substations, industrial facilities, and utility grids using smart automation.
What is SCADA Monitoring?
SCADA monitoring refers to the continuous observation and management of automated systems across electrical and industrial networks. It plays a key role in modern energy infrastructure.
✅ Real-time tracking of power system performance and grid conditions
✅ Remote diagnostics and control of substations and assets
✅ Enables predictive maintenance and faster fault response
SCADA monitoring plays a central role in the supervision and operation of modern industrial systems. By integrating hardware, software, and communication infrastructure, operators can monitor and control critical equipment across vast physical distances remotely. In today’s power, manufacturing, and oil and gas sectors, the ability to gather and act on real-time data is essential for maintaining system efficiency, reliability, and safety. If you're new to the topic, start with our introductory guide that explains what is SCADA and why it's essential for utility operations.
At its core, SCADA monitoring is a component of a broader control system that provides visibility into ongoing processes. It enables centralized operators to observe equipment status, collect performance data, respond to alarms, and adjust operational settings — all through intuitive user interfaces. As industrial demands have grown more complex, so too have the expectations placed on monitoring systems. What was once a simple network of field devices has evolved into a fully integrated, highly responsive SCADA solution. For a deeper understanding of how SCADA systems collect and transmit real-time data, see our detailed explanation how does SCADA work.
SCADA Monitoring Components
A typical SCADA system relies on several essential components working together. Remote terminal units (RTUs) and programmable logic controllers (PLCs) are deployed at field sites to interact with sensors, actuators, and other physical devices. These units gather input data and execute control functions in response to system conditions. Information from RTUs and PLCs is transmitted to central servers running SCADA software, which organizes and displays the data in real time.
The interface between the operator and the system is managed through a human-machine interface (HMI). Modern HMI software presents visual representations of plant operations, allowing operators to interact with the system, adjust controls, and respond to alerts. The integration of HMI SCADA platforms ensures that both the data and the control logic are accessible through a single, cohesive display.
SCADA Monitoring Overview Table
Category | Description |
---|---|
System Purpose | Supervises and manages industrial operations remotely using real time data and automation. |
Core Components | - Remote Terminal Units (RTUs) - Programmable Logic Controllers (PLCs) - SCADA Software - Human Machine Interface (HMI) |
Key Functions | - Real-time monitoring - Alarm management - Trend logging - Centralized control |
Industries Using SCADA | - Oil and Gas - Electric Power - Water Treatment - Manufacturing |
Technologies Involved | - Industrial Control Systems (ICS) - HMI SCADA integration - Edge computing - Open protocols |
Human Role | Operators use HMI software and user interfaces to analyze data, respond to alarms, and optimize system performance |
Benefits | - Improved operational efficiency - Enhanced system reliability - Reduced downtime - Remote access and control |
Modern Trends | - Cloud integration - Predictive maintenance - IoT connectivity - Scalable architectures |
SCADA in Automation Strategy | Acts as the supervisory layer that connects field-level hardware to centralized decision-making platforms in industrial automation environments |
Functionality in Industrial Control Systems
SCADA monitoring is a vital layer within larger industrial control systems. It does not operate equipment directly in most cases, but instead supervises the devices that do. This distinction is important because it reflects the supervisory nature of the system, observing, logging, and managing the behaviour of field-level automation through feedback loops and control logic.
This supervisory capability allows centralized personnel to monitor and control widely distributed infrastructure without needing to be physically present. In industries like oil and gas, where equipment may be hundreds of kilometres from the nearest operator, this functionality is not merely convenient — it is indispensable.
In a system running environment where downtime can mean safety hazards or financial loss, SCADA monitoring provides early warning through alarm management, trend analysis, and historical logging. Operators can analyze deviations in pressure, temperature, voltage, or flow rates, and make timely decisions to correct them.
Integration with Modern Technologies
Modern SCADA systems go beyond traditional control and visualization. They are increasingly integrated with enterprise systems, cloud platforms, and industrial IoT technologies. These advancements allow greater scalability, data sharing, and machine learning applications to support predictive maintenance and operational optimization.
Flexible architectures support diverse communication protocols and open standards, which means that newer computer systems and devices can be easily integrated into existing networks. This adaptability is crucial for organizations seeking to future-proof their investments in industrial automation.
Today’s SCADA monitoring environments often include edge computing devices that can process data locally before sending it to central servers. This not only reduces network load but also enables faster decision-making. The result is a monitoring system that is both responsive and resilient. To explore how communication layers and devices interact in modern systems, visit our overview of SCADA architecture.
Enhancing Human Interaction
While the system itself may be automated, the human role remains critical. The quality of user interfaces, including the design and layout of the human machine interface HMI, significantly affects operational performance. Intuitive dashboards reduce cognitive load, allowing operators to make faster, more accurate decisions.
Clear visualization, logical grouping of controls, and streamlined alarm handling are essential features of modern HMI software. Effective SCADA monitoring depends on the user’s ability to interpret information quickly and respond appropriately. For this reason, many organizations invest in interface customization and operator training to maximize the value of the technology.
Application Across Sectors
SCADA monitoring is used across virtually every industrial sector. In oil and gas, it tracks pressure, flow, and valve status in pipelines and production sites. In power transmission and distribution, it supports the operation of substations, switching systems, and grid infrastructure. In water treatment facilities, it ensures the proper balance of chemicals and the functioning of pumps and filters. And in manufacturing, it oversees assembly lines, robotics, and material handling.
Regardless of the application, the purpose remains the same: to provide accurate, timely, and actionable insights into system operations, enabling operators to maintain safety, efficiency, and reliability. Learn how SCADA is applied specifically to substations in our in-depth look at substation SCADA and its role in grid automation.
SCADA monitoring represents the convergence of computer systems, field devices, and human oversight. It empowers operators to manage complex processes in real time, even from a distance, using data-rich SCADA software and visual user interfaces. Whether applied to oil and gas, power grids, or production lines, it is an essential tool in any modern industrial automation strategy. As technologies evolve, the capabilities of SCADA monitoring will continue to expand — but its core value will remain the same: turning data into control.
Related Articles
On-Site Training
Interested in cost effective, professional on-site electrical training?
We can present an Electrical Training Course to your electrical engineering and maintenance staff, on your premises, tailored to your specific equipment and requirements. Click on the link below to request a Free quotation.
EF PARTNER MEDIA
Product Showcases
Shared Media