What is an Affected Employee's Responsibility During LOTO?
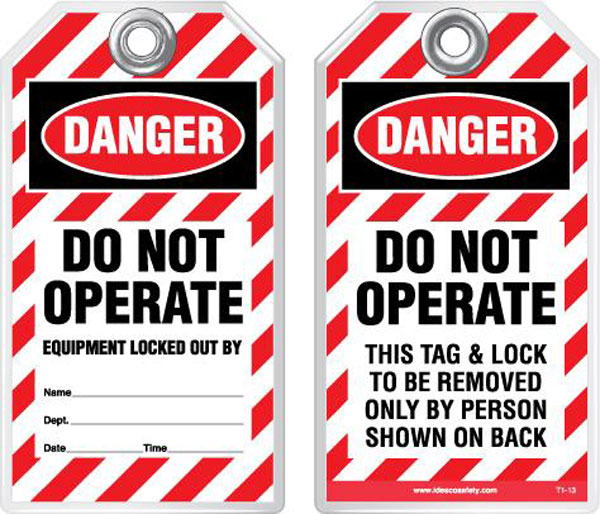
Affected employees play a vital role in lockout tagout by recognizing hazardous energy, respecting energy control procedures, and ensuring safe equipment use during servicing or maintenance.
What is an affected employee's responsibility during a lockout tagout?
An affected employee must understand and follow lockout tagout (LOTO) procedures to ensure their own safety and that of others.
✅ Recognize when lockout tagout is in place and never attempt to restart machines or equipment.
✅ Follow all energy control procedures to protect against hazardous energy during maintenance.
✅ Stay alert to lockout devices, tags, and instructions, ensuring safety for themselves and others.
What is an Affected Employee's Responsibility During a Lockout/Tagout? Understanding the role of an affected employee is crucial for maintaining workplace safety during lockout/tagout (LOTO) procedures. An affected employee is someone whose job requires them to operate or use a machine or equipment on which servicing or maintenance is being performed under lockout or tagout, or whose job requires them to work in an area where such servicing or maintenance is being conducted. To fully understand the safety process, see our overview on Lockout Tagout.
Their primary responsibilities include recognizing when LOTO procedures are in effect, refraining from attempting to start or use equipment that has been locked or tagged out, and understanding the purpose and use of energy control procedures. By adhering to these guidelines, affected employees play a vital role in preventing accidents and ensuring compliance with Occupational Safety and Health Administration (OSHA) standards. Affected employees must understand their role in OSHA’s lockout/tagout standard 29 CFR 1910.147, which outlines how to prevent the unexpected startup of equipment.
CSA Z460 Lockout Tagout Training
Request a Free Training Quotation
In the context of occupational safety, lockout/tagout (LOTO) procedures are essential for ensuring that machines and equipment are properly shut off and cannot be restarted until maintenance or servicing activities are complete. Both authorized and affected employees play critical roles in this safety process. While authorized workers have the duty to implement the energy control procedures, affected personnel have specific roles to ensure safety during these operations. NFPA 70E arc flash training provides affected employees with the knowledge to stay safe around energized equipment. If you’re new to the concept, start with What is Lockout Tagout for a complete introduction.
To ensure compliance with Occupational Safety and Health Administration (OSHA) regulations, any employee becomes an authorized worker when their duties include servicing or maintaining that machine or equipment. Before beginning work, they must secure the area to perform servicing or maintenance on the machine or equipment, following lockout/tagout procedures to prevent unexpected startup or energy release. OSHA defines the requirements in detail under the OSHA Lockout Tagout Standard.
If a worker needs to operate equipment to perform servicing or maintenance on the equipment, they must adhere to strict safety protocols. Proper training ensures that all servicing or maintenance covered under OSHA guidelines is performed safely, reducing the risk of workplace injuries. Canadian facilities can benefit from CSA Z462 Arc Flash Training, which includes the responsibilities of affected employees under LOTO. Workers can build essential skills by completing OSHA Lockout Tagout Training.
Frequently Asked Questions
How Does an Affected Employee Know When a Lockout Tagout Procedure Is in Place?
Communication is vital during any lockout or tagout event. Affected individuals are notified about the energy control procedures through multiple means, including visual indicators like tags and locks, as well as verbal or written communication from authorized personnel. The presence of locks and tags on machines signals that the equipment is locked out to prevent unexpected energization. For companies building compliance strategies, our guide to Lockout Tagout Programs explains best practices.
In addition, proper training required by occupational safety standards ensures that each worker is aware of the significance of the devices used. They should understand that the machine or equipment being locked out is under maintenance or servicing and that any attempt to bypass these controls could lead to exposure to hazardous energy sources. A clear Lockout Tagout Procedure helps ensure workers remain protected during servicing.
What Should an Affected Employee Do if They Notice a Problem With the Lockout Tagout Procedure?
If an affected worker notices any problems or inconsistencies with the lockout or tagout procedure, such as missing tags, improperly secured locks, or unauthorized use of equipment, they must report the issue immediately to a supervisor or the authorized employee in charge. This is a key responsibility for maintaining a safe work environment. Any malfunction or misuse of locks or tags could lead to the accidental release of stored energy, posing severe risks to those working in the area.
The employee's duties include being vigilant and proactive in identifying potential issues during maintenance activities. Ensuring that all energy control procedures are properly followed is essential to preventing injuries. To see the step-by-step process, review our detailed Lockout Tagout Steps.
Can an Affected Employee Remove a Lockout or Tagout Device?
No. Only an authorized employee who initiated the lockout or tagout can remove the device. Under no circumstances should an affected worker attempt to remove a lockout or tagout device, even if they believe the servicing is complete. Removing these devices without authorization could cause significant safety hazards, as equipment may still be in an unsafe condition or energized with hazardous energy.
Each worker must understand their role in these situations to avoid potential accidents. A lockout or tagout device should remain in place until the authorized worker verifies that all maintenance activities have been completed and the equipment is safe to use.
What Should an Affected Employee Do if They Need to Access Equipment Under Lockout Tagout for Non-Operational Reasons?
If an affected worker needs to access equipment for non-operational reasons during a lockout or tagout procedure, they must first communicate with the authorized employee responsible for the lockout or tagout. Under no circumstances should they bypass the locks or tags to gain access. The person performing the servicing or maintenance is responsible for ensuring that any access is safe and appropriate.
The training required by safety regulations ensures that all personnel, including those affected, understand the proper steps to follow in such situations. Communication with authorized workers is crucial to avoid unnecessary risks associated with stored energy or incomplete maintenance.
The Role of Authorized and Affected Employees
While an affected worker does not perform the energy isolation tasks, their awareness of the process is just as important for overall workplace safety. In contrast, an authorized worker is responsible for executing the energy control procedures, locking out the machine or equipment, and verifying that the system is free from hazardous energy sources before performing any servicing. If the affected individual undergoes additional training, they can become an authorized worker and take on a more direct role in energy control procedures.
Training is a vital part of occupational safety for both authorized and affected personnel. Understanding how to properly lock out or tag out equipment and the associated duties ensures that the risks of hazardous energy are minimized for everyone working in the vicinity of the machinery.
In summary, affected workers play crucial roles during lockout or tagout procedures, although their responsibilities are more passive compared to those of authorized workers. Their duties involve adhering to energy control procedures, being aware of equipment that is locked out, and reporting any issues with locks or tags. They must never attempt to remove locks or tags or interfere with the lockout or tagout process in any way. By understanding their roles and cooperating with authorized workers, affected personnel contribute significantly to maintaining a safe working environment during servicing or maintenance activities.
Ensuring that both authorized and affected individuals are properly trained and informed about their duties under energy control procedures is essential in preventing workplace accidents. By following the correct safety protocols, including the use of locks and tags, workers can protect themselves and their colleagues from the dangers of hazardous energy sources. Arc flash analysis helps determine which equipment requires lockout/tagout procedures based on the level of energy exposure.
Related Resources
To explore more about lockout tagout safety and compliance, see the following resources:
To fully understand the safety process, see our overview on Lockout Tagout.
If you’re new to the concept, start with What is Lockout Tagout for a complete introduction.
OSHA defines the requirements in detail under the OSHA Lockout Tagout Standard.
Workers can build essential skills by completing OSHA Lockout Tagout Training.
For companies building compliance strategies, our guide to Lockout Tagout Programs explains best practices.
A clear Lockout Tagout Procedure helps ensure workers remain protected during servicing.
To see the step-by-step process, review our detailed Lockout Tagout Steps.
For Canadian workplaces, CSA Z460 Lockout Tagout Training outlines the national standard for hazardous energy control.
In addition, CSA Z462 Arc Flash Training helps ensure compliance with Canadian electrical safety requirements.
On-Site Training
Interested in cost effective, professional on-site electrical training?
We can present an Electrical Training Course to your electrical engineering and maintenance staff, on your premises, tailored to your specific equipment and requirements. Click on the link below to request a Free quotation.
EF PARTNER MEDIA
Product Showcases
Shared Media