Lockout Tagout Program Explained
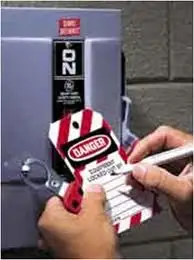
A Lockout Tagout Program ensures worker safety by controlling hazardous energy during equipment maintenance. OSHA and NFPA 70E compliance requires written procedures, employee training, and regular audits to prevent accidental startup.
What is a Lockout Tagout Program?
A Lockout Tagout Program is more than just locks and tags—it is a complete safety management system that ensures hazardous energy is controlled during servicing or maintenance.
✅ Creates a written framework for energy control procedures
✅ Assigns roles, responsibilities, and training requirements
✅ Ensures OSHA and NFPA 70E compliance through inspections and audits
To understand the fundamentals, start with our overview of Lockout Tagout, which explains how energy control protects workers. For a deeper foundation, see What is Lockout Tagout.
Request a Free Training Quotation
Why a Lockout Tagout Program Matters
Under OSHA’s 29 CFR 1910.147 standard, employers are required to implement a comprehensive energy control program that safeguards workers from hazardous energy during maintenance. This includes developing specific procedures for isolating all potential energy sources, not just those including electrical systems, but also hydraulic, pneumatic, chemical, thermal or other sources that could lead to unexpected startup or the release of stored energy. A well-structured lockout tagout LOTO plan ensures that all machines or equipment are properly secured, and that hazardous energy lockout tagout methods are applied consistently to protect workers across every environment where servicing occurs.
OSHA consistently lists Lockout Tagout violations among its top ten workplace safety infractions. A well-structured program prevents serious injuries caused by unexpected startup or stored energy release. Beyond compliance, it:
-
Builds a safety-first culture that reduces downtime and liability
-
Strengthens employee confidence in workplace protection
-
Supports regulatory compliance with OSHA, NFPA 70E, and CSA Z462
To strengthen safety culture further, explore Lockout Tagout Training, which ensures authorized and affected employees fully understand their responsibilities.
Core Elements
While step-by-step isolation methods are covered in the Lockout Tagout Procedure, the program itself provides the governance structure that keeps those procedures consistent. A compliant LOTO program should include:
1. Written Energy Control Policies
Employers must document policies that define how hazardous energy is controlled across the facility. Policies should reference regulatory standards and apply consistently across all equipment types.
2. Hazard Assessment and Energy Source Inventory
Each machine or system must be assessed, and every energy source—electrical, mechanical, chemical, or thermal—must be identified. This inventory ensures no source is overlooked during servicing.
3. Assignment of Roles
Programs must clearly define the responsibilities of:
-
Authorized employees – apply locks, tags, and perform verification
-
Affected employees – operate or use the equipment under control
-
Other employees – understand restrictions when working near controlled equipment
When multiple employees are involved, Group Lockout Tagout procedures ensure every worker applies a personal lock.
4. Lockout/Tagout Devices
Employers must provide standardized devices that are durable and used exclusively for energy control. For practical applications, review our section on Lockout Tagout Devices.
5. Training and Competency
The program must specify training requirements for each role, including initial instruction, refresher courses, and retraining when procedures or equipment change. For regulatory details, see the OSHA Lockout Tagout Standard.
6. Program Inspections and Audits
Annual program-level audits ensure compliance and effectiveness. These reviews must be documented and performed by individuals other than the employees currently executing the procedures.
7. Continuous Improvement
Programs should adapt when equipment, processes, or regulations change. Employers must review and update documentation regularly to maintain accuracy.
Suggested Program Checklist
Here’s a simple reference table to illustrate program elements and their purpose:
Program Element | Purpose | Frequency | Responsible Party |
---|---|---|---|
Written policies | Define rules and responsibilities | Reviewed annually | Safety Manager |
Energy source inventory | Identify all hazardous energy sources | Ongoing | Maintenance Supervisor |
Employee training | Ensure competency by role | Annual refresher | Training Coordinator |
Device management | Provide and maintain lockout devices | As needed | Safety/Procurement Team |
Program audits | Verify compliance and effectiveness | Annually | Qualified Auditor |
Procedure updates | Keep methods current with equipment changes | As required | Program Administrator |
Implementing an Effective Lockout Tagout Program
An effective LOTO program integrates safety into daily operations:
Hazard Assessment
Conduct a comprehensive review of all equipment that may release hazardous energy. This assessment forms the foundation of the program.
Detailed Documentation
Develop clear, equipment-specific energy control procedures. Visual aids, diagrams, or machine-specific tags can make them easier to follow.
Training Requirements
Ensure new hires are trained before work begins, and provide refresher training annually. For formal instruction, see OSHA Lockout Tagout Training.
Device Maintenance and Availability
LOTO devices should be accessible, properly maintained, and replaced if damaged. Inadequate devices compromise both safety and compliance.
Audits and Oversight
Conduct scheduled audits to ensure procedures are followed. Document results and address deficiencies promptly.
Recordkeeping
Maintain accurate logs of training, inspections, audits, and procedural updates. This demonstrates compliance during OSHA inspections and reinforces internal accountability.
Frequently Asked Questions
What is the difference between a LOTO Program and a Procedure?
The program is the administrative framework (policies, roles, audits), while the procedure is the step-by-step method applied to each piece of equipment. See our Lockout Tagout Procedure for details.
Who is responsible for maintaining a LOTO Program?
Employers must create, enforce, and maintain the program, provide devices, and ensure employee training.
How often should a LOTO Program be reviewed?
Programs must be reviewed annually, but updates should occur whenever new equipment or processes are introduced.
For common concerns, explore Lockout Tagout Questions, where frequently asked topics are explained in detail.
Related Articles
-
To clear up common issues, explore Lockout Tagout Questions, where frequently asked topics are explained in detail.
To ensure compliance and worker protection, The Electricity Forum offers specialized Construction Electrical Safety Training, including NFPA 70E Training and CSA Z462 Arc Flash Training courses. Request a free training quotation today to equip your team with the knowledge and skills they need to stay safe on the job.
On-Site Training
Interested in cost effective, professional on-site electrical training?
We can present an Electrical Training Course to your electrical engineering and maintenance staff, on your premises, tailored to your specific equipment and requirements. Click on the link below to request a Free quotation.
EF PARTNER MEDIA
Product Showcases
Shared Media