OSHA Lockout Tagout Requirements Explained
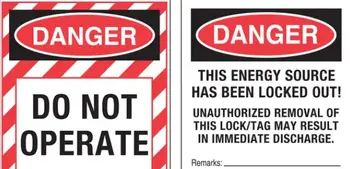
OSHA lockout tagout requirements help prevent accidental energization during maintenance. These rules mandate isolating energy sources, using locks and tags, and training workers. Compliance reduces electrical hazards, ensuring safer work environments in industrial and commercial settings.
What are OSHA Lockout Tagout Requirements?
OSHA Lockout Tagout requirements for hazardous energy control, outlined in 29 CFR 1910.147, are designed to prevent injuries caused by the unexpected release of hazardous energy during maintenance.
✅ Protects workers by isolating energy sources before maintenance
✅ Requires locks, tags, and written procedures for compliance
✅ Mandates training and periodic inspections to prevent injuries
Employers must implement a written energy control program, train authorized personnel, and use approved lockout/tagout devices to ensure compliance. This standard is critical for protecting workers in industrial settings and avoiding costly violations. If you need a solid foundation, start with What is Lockout Tagout? to grasp the core purpose and definitions behind every LOTO program.
The Occupational Safety and Health Administration enforces regulations under lockout/tagout (29 CFR) to protect workers from injuries caused by the unexpected startup or release of hazardous energy during the servicing or maintenance of machines or equipment. The standard, formally known as tagout 29 CFR 1910.147, outlines procedures for controlling various forms of energy, including electrical, mechanical, hydraulic, pneumatic, chemical, and thermal. Dive deeper into the regulatory details by reviewing the OSHA Lockout Tagout Standard, which unpacks each clause of 29 CFR 1910.147.
These energy types can pose serious risks if not properly controlled, which is why hazardous energy lockout tagout procedures are critical. Effective lockout tagout programs require employers to establish and enforce detailed protocols to isolate and secure energy sources. By following the requirements set out in lockout tagout 29, facilities can ensure that maintenance personnel are protected from accidental energy release while working on machines or equipment.
Purpose of OSHA's LOTO Standard
The primary objective of OSHA’s lockout/tagout requirements is to ensure that machines are properly shut down, isolated from energy sources, and secured so that they cannot be re-energized during maintenance. Compliance helps prevent serious injuries, amputations, and fatalities in industrial and manufacturing settings.
Key Requirements of OSHA Standard 29 CFR 1910.147
1. Written Energy Control Program
Employers must establish a formal energy control program that includes policies, procedures, and responsibilities for controlling hazardous energy during maintenance activities. If you’re building company controls, our template-driven Lockout Tagout Program shows how to structure policies, responsibilities, and audits.
2. Energy Control Procedures
Detailed, equipment-specific procedures must be developed and documented for shutting down, isolating, locking out, and verifying de-energization of equipment before servicing begins. When it’s time to write machine-specific instructions, follow the step-by-step guidance in the Lockout Tagout Procedure article.
3. Training for Employees
-
Authorized employees: Those who perform maintenance must be trained in recognizing hazardous energy sources and the proper application of energy control procedures.
-
Affected employees: Workers who operate or work near the machines must be trained to understand the purpose of lockout/tagout and recognize when it is in use.
-
Other employees: Must receive awareness training to avoid interference with lockout/tagout devices.
4. Lockout/Tagout Devices
Employers must provide appropriate devices, such as padlocks, hasps, tags, valve lockouts, and breaker lockouts, to isolate energy sources. These devices must be durable, standardized, and substantial enough to prevent accidental removal. Selecting compliant hardware is easier with our comparison guide to Lockout Tagout Devices, covering locks, tags, and isolation tools.
5. Periodic Inspections
Each energy control procedure must be inspected at least annually by an authorized employee not directly involved in the procedure being evaluated. The purpose is to verify proper execution and identify deficiencies.
6. Recordkeeping
Employers are required to maintain written procedures, a current list of authorized personnel, and documentation of training and periodic inspections.
7. Retraining Requirements
Retraining is required whenever there is a change in job assignments, equipment, energy control procedures, or if an employee is found not complying with procedures.
Hazardous Energy Types Covered by the Standard
The OSHA standard applies to various forms of hazardous energy, including:
-
Electrical
-
Mechanical
-
Hydraulic
-
Pneumatic
-
Chemical
-
Thermal
-
Stored or residual energy (e.g., compressed springs, charged capacitors)
Exemptions to the Standard
OSHA provides a few exemptions to the lockout/tagout standard, including:
-
Work on cord-and-plug-connected equipment where unplugging provides complete energy isolation
-
Minor tool changes or adjustments during normal production operations, provided they are routine, repetitive, and integral to the process (and alternative measures provide equivalent protection)
Why OSHA Compliance Matters
Failure to follow OSHA's lockout/tagout requirements can result in severe penalties and tragic workplace incidents. According to OSHA, violations of this standard remain among the top ten most frequently cited each year.
Maintaining compliance with 29 CFR 1910.147 not only protects employees but also enhances operational efficiency by preventing costly accidents and equipment damage.
Frequently Asked Questions (FAQ)
What does OSHA require for lockout tagout?
OSHA requires employers to develop and implement a written energy control program, train authorized and affected employees, provide appropriate lockout/tagout devices, and conduct periodic inspections. These requirements are outlined in OSHA standard 29 CFR 1910.147 to prevent the accidental release of hazardous energy during servicing and maintenance.
Who needs to be trained in LOTO procedures?
All employees who may be exposed to hazardous energy must receive training. This includes authorized employees who perform maintenance, affected employees who work near locked-out equipment, and all other personnel who may encounter LOTO devices. Retraining is required when procedures change or when non-compliance is observed.
How often are periodic inspections required under 29 CFR 1910.147?
Periodic inspections must be conducted at least once per year for each energy control procedure. These audits verify that employees are following proper procedures and that lockout/tagout practices remain effective. Inspections must be documented and performed by someone other than the person using the procedure. For a quick field reference, the Lockout Tagout Steps page breaks down the eight critical actions every technician must complete.
Finally, ensure workforce competence with instructor-led OSHA Lockout Tagout Training that aligns classroom learning with real-world maintenance scenarios.
Learn More
To ensure your facility is meeting OSHA LOTO requirements, explore:
Compliance with OSHA lockout/tagout regulations is not just a legal requirement—it's a critical safeguard for worker safety and organizational integrity.
On-Site Training
Interested in cost effective, professional on-site electrical training?
We can present an Electrical Training Course to your electrical engineering and maintenance staff, on your premises, tailored to your specific equipment and requirements. Click on the link below to request a Free quotation.
EF PARTNER MEDIA
Product Showcases
Shared Media