VFD Programming: Crucial Role in Motor Control
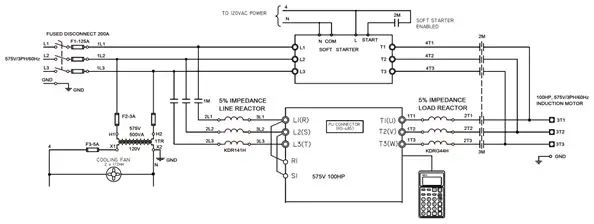
In industrial applications, Variable Frequency Drive (VFD) programming plays a crucial role in motor control and energy efficiency. VFD programming involves configuring and optimizing the settings of a VFD to achieve desired motor performance and reduce energy consumption. With the right programming techniques, users can remotely control motor speed, improve energy efficiency, and leverage common VFD communication protocols for seamless operation.
The VFD service industry has long faced a safety dilemma. Traditionally, VFDs with a high arc flash risk potential were housed within the same cabinet as live 600-volt power. This dangerous combination required technicians to wear protective clothing when programming the VFD, increasing the risk of accidents due to limited dexterity and poor visibility. Fortunately, innovations like the JZB1000 MCC by Higrid Power Corp. have mitigated these risks by isolating the VFD from high-energy power sources during programming.
Figure 1. Typical VFD with 30 to 60kA short circuit capability
The JZB1000 MCC features two design versions that eliminate arc flash incidents during VFD programming. In the first version, the complete VFD and necessary options are mounted in a draw-out unit that can be disconnected from the vertical bus. A low-energy control power supply, typically 24VDC or AC, powers up the microprocessor and keypad while the unit is physically disconnected from the 600-volt bus. This setup allows technicians to program the VFD safely without needing face shields or gloves.
The second version also involves a draw-out cell but uses a separate cell for the fused switch or circuit breaker. Once this feeder cell is padlocked in the disconnected position, the arc flash risk is reduced.
To understand the intricacies, becoming familiar with specific VFD parameters and concepts is essential. These include motor nameplate data, motor overload protection, full-load amperage, and analog inputs. Additionally, technicians should know how to reset the drive to factory or default settings when necessary and be able to navigate parameter numbers to configure the VFD for optimal performance.
Motor nameplate data is crucial for ensuring proper VFD configuration. The motor's nameplate provides essential information, such as voltage, current, and speed ratings, to determine suitable VFD settings. Motor overload protection is also crucial to prevent damage to the motor due to excessive current or overheating. Full load amperage refers to the current a motor draws when operating at its rated horsepower. At the same time, analog inputs allow for remote motor speed control through a proportional signal from an external device.
Figure 2. Typical VFD with 30 to 60kA short circuit capability with Draw out isolation
The numerous benefits include energy savings, remote motor speed control, and improved motor performance. By optimizing the VFD parameters, technicians can ensure the motor operates at the most efficient point on its torque-speed curve, resulting in substantial energy savings. Moreover, with modern VFD communication protocols, users can monitor and control motor speed remotely, adding flexibility to industrial operations.
It is an essential skill in the industrial sector. With innovations like the JZB1000 MCC, technicians can program VFDs more safely while understanding key parameters and concepts that will ensure optimal motor performance and energy efficiency. Whether you're an experienced engineer or new to VFDs, mastering these skills will undoubtedly prove invaluable in today's demanding industrial landscape.
Read More VFD Articles Here
On-Site Training
Interested in cost effective, professional on-site electrical training?
We can present an Electrical Training Course to your electrical engineering and maintenance staff, on your premises, tailored to your specific equipment and requirements. Click on the link below to request a Free quotation.
EF PARTNER MEDIA
Product Showcases
Shared Media