VFD Sizing: The main onsiderations
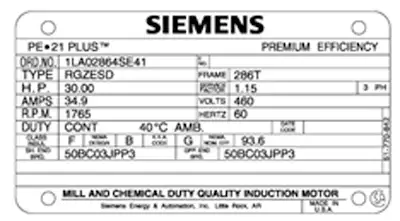
VFD sizing matches a drive’s current rating to motor amperage. Consider load type, torque demands, and conditions to choose a drive that prevents overheating and ensures long-term motor performance.
Quick Definition: VFD Sizing
-
✅ Definition: The process of selecting a Variable Frequency Drive (VFD) that matches the motor's electrical and operational requirements.
-
✅ Key Considerations: Motor full-load amperage, application type (constant or variable torque), overload capacity, and environmental conditions.
-
✅ Importance: Proper VFD sizing prevents equipment damage, ensures energy efficiency, and extends the lifespan of both the motor and the drive.
Proper VFD sizing is critical to ensure optimal motor performance, energy efficiency, and equipment protection. When sizing a Variable Frequency Drive (VFD), it is essential to consider the motor's full-load amperage, the application type, overload requirements, and environmental factors. Selecting a correctly sized Variable Frequency Drive prevents overheating, improves system reliability, and maximizes the lifespan of both the drive and the motor. When considering Variable Frequency Drive sizing, it's important also to understand how different VFD drives operate and the impact they have on motor control performance.
When selecting a Variable Frequency Drive, it’s essential to match the drive’s current rating to the motor’s full load amps (FLA) as listed on the motor nameplate. The horsepower (hp) rating alone is not enough, because different motors with the same hp can have varying current requirements based on efficiency, design, and application. Always use the motor nameplate data for accurate sizing to ensure the Variable Frequency Drive can handle the full operational load without overheating or tripping during normal operation.
In VFD Sizing, the main considerations are:
1. The Variable Frequency Drive continuous current shall be higher than the motor’s current at maximum load. It is not necessary to size the Variable Frequency Drive to the motor Full Load Amps (FLA) rating if the motor application is oversized. A motor that operates under worst-case conditions at 80% FLA current flowing only requires a Variable Frequency Drive that can continuously supply this 80% current value.
2. For Variable Torque Applications, the intermittent current shall be 115% greater than the motor current rating for the worst case starting scenario. If the motor rated current is 65 amperes, then the intermittent current rating should be greater than 74.8 amperes (65A x 115%).
For Constant Torque Application, the intermittent current shall be 150 to 200% of the motor rated current. The equipment OEM can provide the actual worst-case starting torque that they would normally expect for the application. By ensuring that the intermittent current capability of the Variable Frequency Drive is higher than this value, the ac drive will produce sufficient torque to start the HP motor under abnormal situations. Accurate VFD programming ensures that a properly sized drive operates within the correct voltage and current limits, protecting connected equipment.
3. The single-phase input voltage tolerance rating for the Variable Frequency Drive shall be higher than the highest line voltage and lower than the lowest line voltage that lasts longer than two seconds in the facility. Variable Frequency Drives have a 100% voltage rating of 200, 230, 460 or 575 Volts. Each site has different high and low line levels that the Variable Frequency Drive must be able to safely operate at without being damaged. If the measured low line voltage is 550 volts and the high line voltage is 625 volts, then we need a 575-volt-rated Variable Frequency Drive with a voltage tolerance of 575 volts plus 10.9% (625 volts), minus 4.6% (550 volts), or greater. Actual common tolerance values for Variable Frequency Drives are as follows: -5 %, 10%, 12%, 15%, and 20%. Some 575v commercial-rated Variable Frequency Drives are 575v +5%, -10% (518v to 603v), whereas an industrial-rated Variable Frequency Drive may be rated 575v +/- 15% (489v to 660v). If the tolerance rating of the Variable Frequency Drive does not meet the high-line actual site voltage condition, then the Variable Frequency Drive is subject to potential catastrophic failure. In some cases, a frequency converter may be necessary in conjunction with a Variable Frequency Drive to manage input or output frequencies that affect proper sizing.
Other Variable Frequency Drive equipment to be upgraded or changed:
Many factors need to be considered when conducting Variable Frequency Drive Sizing in an existing application:
-
Is the existing motor suitable for the speed range, and is the insulation designed to withstand the dv/dt stress caused by the fast switching of the voltage pulses to the motor? If not, use a NEMA MG1 Part 31 designed motor.
-
All VFD manufacturers recommend replacing the motor feeder cable with a shielded, symmetrical cable for the Variable Frequency Drive.
Motor specifications:
In North America, NEMA MG1 standards are used to specify motors. In 1992, a new section (Part 31) was added to specifically address the motor design requirements to work on a Variable Frequency Drive application without installing motor feeder filtering. The original Part 30 design motor nameplate specification allowed for Variable Frequency Drive (VFD) operation if properly sized motor filters were installed in the VFD package.
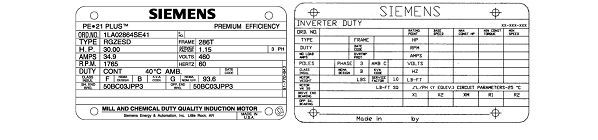
Figure 1: NEMA Part 30 & 31 Nameplates
Since each application required a custom-engineered solution for the proper selection of motor filters, most users and Variable Frequency Drive distributors were not qualified to select the filters properly, thereby increasing the risk of a successful filter selection. By installing the NEMA MG1 Part 31 designed motor, there is no requirement to install a motor filter. The deletion of the requirement for a motor filter typically offsets the slight cost increase associated with the Part 31 motor. The Part 31 motor has an enhanced nameplate that provides motor performance data when the motor is operated at the lowest operating speed, the base 60Hz speed, and the highest speed above 60Hz.
System component used with Variable Frequency Drives:
Many factors are required when the decision for installing a Variable Frequency Drive is made: The Variable Frequency Drive solution should be supplied with all the necessary equipment to provide for a long life and reliable Variable Frequency Drive solution:
-
Circuit Breaker,
-
Transient Surge Protection,
-
Line Filtering, Harmonics and Power Factor
-
Standard or High-Performance Variable Frequency Drive chassis, as needed for the application.
-
VFD cable
-
NEMA MG1 Part 31 motor should always be used
-
Ambient Temperature
-
Derating the VFD
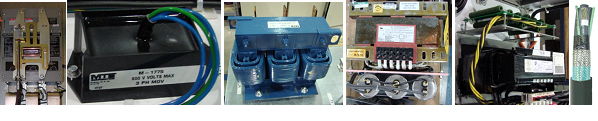
Figure 2: Circuit breaker, MOVs, Reactor, Harmonic Filter, and Variable Frequency Drive Cable
For Variable Frequency Drives used in building systems, review the special considerations outlined in Variable Frequency Drive HVAC applications.
Related Variable Frequency Drives Articles:
On-Site Training
Interested in cost effective, professional on-site electrical training?
We can present an Electrical Training Course to your electrical engineering and maintenance staff, on your premises, tailored to your specific equipment and requirements. Click on the link below to request a Free quotation.
EF PARTNER MEDIA
Product Showcases
Shared Media