Core Current Transformer Explained
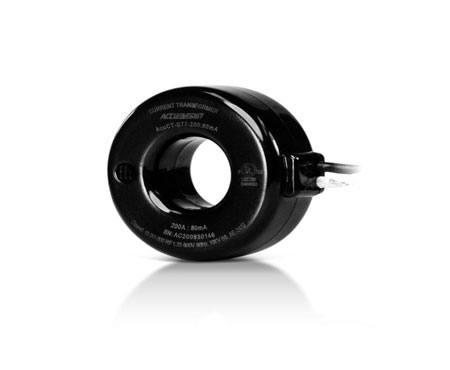
A core current transformer measures alternating current by producing a scaled secondary current that is proportional to the primary current. It ensures accurate metering, protection, and monitoring in electrical systems, commonly used in power distribution and industrial applications.
What is a Core Current Transformer?
A core current transformer (CCT) is a crucial component in the field of electrical systems, commonly used for monitoring and controlling electrical circuits.
✅ Converts high primary currents into safe, measurable secondary currents.
✅ Enhances accuracy for metering and protective relays.
✅ Used in electrical substations, industrial control systems, and power distribution networks.
To understand the basic function of transformers, see our guide on what is a transformer.
Electrical Transformer Maintenance Training
Substation Maintenance Training
Request a Free Training Quotation
The core current equipment works by measuring the current flowing through conductors and ensuring the' safe and efficient operation of electrical networks. It generates a proportional secondary current in response to the magnetic field induced by the primary current. Electricians will learn the importance of core CTs in industrial applications, the various types available, and how to properly install and maintain them for optimal performance. With this knowledge, professionals can enhance their troubleshooting skills, prevent costly downtime, and improve overall electrical safety in industrial settings. A current transformer plays a vital role in scaling down high primary currents to safe, measurable levels for monitoring and protection.
Types of Core Current Transformer: Solid Core vs. Split Core
The types of CTs vary based on their configurations and intended applications. In particular, the two most common types are the solid-core and split-core current transformer. The solid core design is typically preferred for fixed installations where the wiring configuration does not need to be altered after installation. The core is a single, continuous piece of material that provides a stable and durable structure for the equipment. On the other hand, the split core current equipment allows for easy installation around existing conductors. The ability to "split" the core open makes this configuration ideal for retrofit applications, where adding new wiring or modifying existing circuits would be impractical. Comparing designs such as delta and wye connections, our delta vs wye article explains key differences in configuration and performance.
Comparison of Core Current Transformers: Solid Core vs. Split Core
Feature | Solid Core Current Transformer | Split Core Current Transformer | Best Applications |
---|---|---|---|
Design | Single, continuous magnetic core | Core opens/closes for easy placement | Solid core for fixed installs, split core for retrofits |
Installation | Requires disconnecting conductors during setup | Installs without removing existing wiring | Split core preferred in existing systems |
Durability | More robust and stable structure | Slightly less durable due to openable core | Solid core for high-durability needs |
Accuracy | High measurement accuracy | Slightly lower accuracy compared to solid core | Solid core in precision metering |
Cost | Generally lower cost | Typically higher cost due to design flexibility | Split core for convenience-focused projects |
Maintenance | Minimal maintenance required | Also low, but hinges may need periodic check | Both for industrial and commercial use |
Applications
CCTs are widely used in different sectors, particularly in environments where safety and reliability are paramount. Their applications span commercial, industrial, and residential settings, where they serve to protect circuits and ensure the proper functioning of control systems. In commercial buildings, a CCT is often integrated into power distribution panels, enabling the monitoring and control of energy usage. They also find applications in industrial environments, such as factories, where accurate current measurement is critical for optimizing machinery operation and preventing equipment failures. Industrial applications often pair core CTs with instrument transformers to enhance precision in electrical metering systems.
Fire Safety and Environmental Protection
The use of CCTs extends to areas where fire safety and environmental protection are significant concerns. In settings such as hospitals, schools, and chemical plants, where maintaining operational safety is crucial, the design of dry-type equipment becomes particularly important. Dry-type equipment, including CT equipment, is often used in these environments due to its lower risk of fire. Since they don't rely on liquid insulation materials, they present fewer fire hazards compared to liquid-filled transformers. This makes them a preferred choice for sensitive applications that require both reliable current measurement and safe operation. For installations needing both current and voltage measurement, a potential transformer works alongside CTs to step down voltages safely.
Advantages and Disadvantages of Core Current Equipment
While a CCT offers various advantages, it is also essential to consider the limitations it may present. One of the primary benefits of this equipment is its minimal maintenance requirements. The absence of liquid insulation and the use of robust materials in the core and enclosure design ensure that the equipment requires less frequent maintenance than other types. Moreover, dry-type core current equipment is environmentally friendly as it avoids the use of toxic substances, contributing to a greener, more sustainable energy system.
However, this equipment may experience higher operational temperatures when compared to liquid-filled types, which could potentially affect their longevity if not properly managed. While effective in many situations, the air-cooled design may not always be sufficient for very high-load applications. Therefore, engineers must carefully assess the operating environment to ensure that the transformer can perform optimally under the expected conditions.
Standards and Compliance for CT
Moreover, CTs must comply with established industry standards to ensure their performance and safety. Standards set by organizations such as ANSI, NEMA, and IEEE help manufacturers produce equipment that meets the requirements of modern electrical systems. Compliance with these standards is critical in maintaining the reliability of control systems that depend on this equipment. For instance, ensuring that the equipment meets the required accuracy class is crucial in applications where precise current measurement is essential for system protection or load balancing. Learn about step-down transformers, which reduce high voltages for safe operation in electrical equipment.
Frequently Asked Questions
What is a core current transformer?
A CCT is the central component of current equipment, typically made of a magnetic material, such as iron or silicon steel. The core serves as the pathway for the magnetic flux generated by the current passing through the primary conductor. The core's main purpose is to produce a proportional output current in the secondary winding, which can then be measured for monitoring or protection purposes in electrical systems. See how autotransformers offer cost-effective voltage regulation for industrial applications.
What is the difference between CCT and PT?
The main difference between a CCT and a Potential Transformer (PT) lies in their function and application:
-
CCT: A CT is used to measure the current flowing through a conductor by producing a reduced, proportional current in its secondary coil, which is easily measured and monitored.
-
PT: A PT, also known as a voltage transformer (VT), is used to step down high voltage levels in electrical systems to a lower, safer level for measurement and monitoring purposes. It provides a proportional voltage to its secondary winding.
In short, CCTs measure current, while PTs measure voltage.
What are the 3 types of transformer cores?
The three primary types of transformer cores are:
-
Shell-type: In this type, the windings are placed around the central core, which is a continuous structure. This configuration provides enhanced magnetic coupling and minimizes leakage flux.
-
Core-type: The windings are placed around the legs of the core, which is typically rectangular. This design is commonly used for power equipment.
-
Toroidal: This type of core is ring-shaped, allowing the windings to be placed around it. The toroidal design offers low core losses and is used in applications where compactness and efficiency are crucial. For a more comprehensive overview of various transformer designs, visit our page on different types of transformers.
A core current transformer is an electrical device used to measure the current flowing through a conductor by producing a proportional output current or voltage. It typically consists of a magnetic core around which the primary conductor passes, with the secondary winding placed around the core. When current flows through the primary, it generates a magnetic field that induces a current in the secondary winding. Core CTs are widely used in power systems for protection, measurement, and monitoring purposes, offering benefits such as electrical isolation, accuracy, and the ability to safely measure high currents without direct contact. Dive into detailed transformer types in our section on electrical power transformers.
Related Articles
On-Site Training
Interested in cost effective, professional on-site electrical training?
We can present an Electrical Training Course to your electrical engineering and maintenance staff, on your premises, tailored to your specific equipment and requirements. Click on the link below to request a Free quotation.
EF PARTNER MEDIA
Videos
Product Showcases
Shared Media